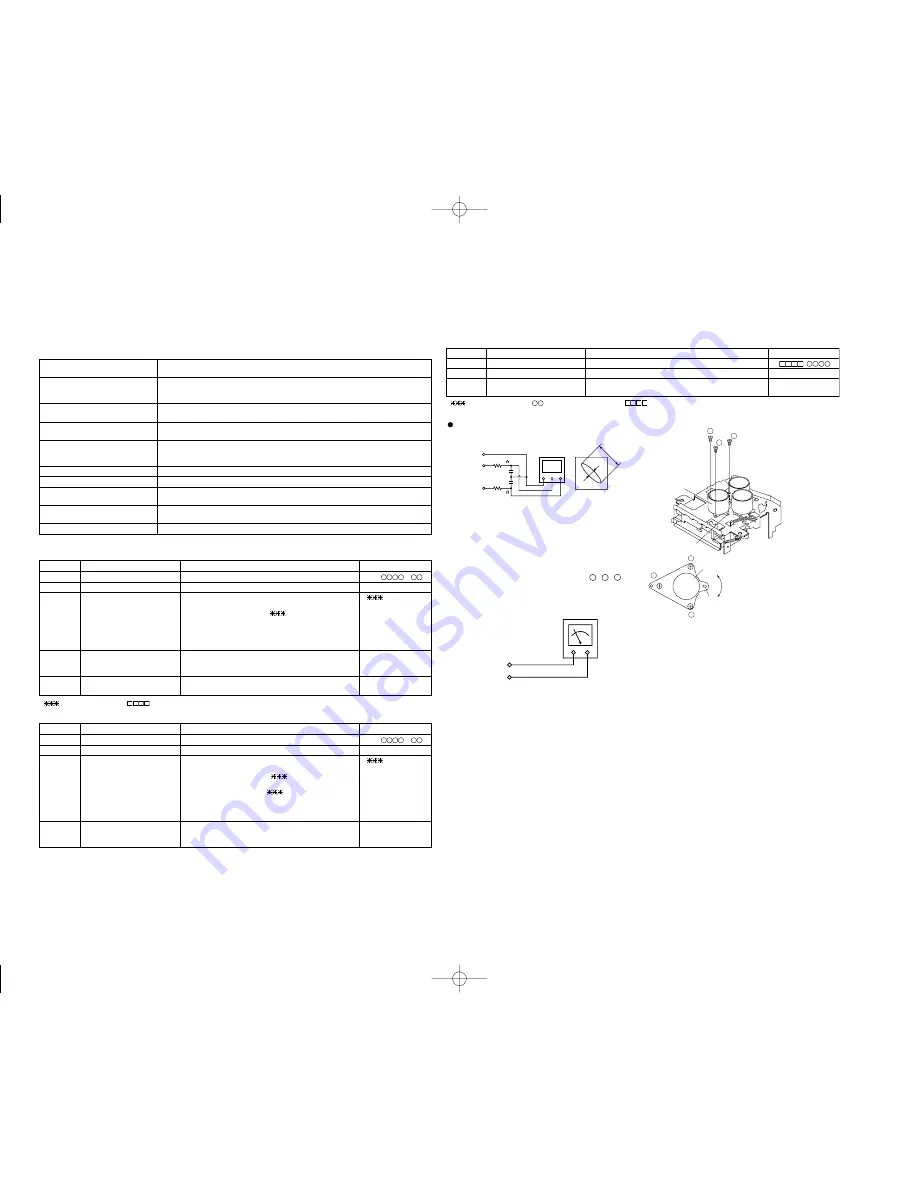
RXD-M31MD
9
CIRCUIT DESCRIPTION
2. AUTO adjustment mode
Step No.
Setting Method
Remarks
Display
Step 1
Test mode STOP state
[ t s m
e
]
Step 2
Press the MD REC button two times.
AUTO adjustment menu
[ A U T O _ A J S T _ ]
Step 3
Press once the MD PLAY button. The slide moves to the innermost periphery, and automatic
[
: _ _ _ _ _ _ ]
adjustment is started.
• In case of high reflection disc
changes as follows.
PEG
→
HAG
•In case of low reflection disc
changes as follows.
PEG
→
LAG
→
GCG
→
GEG
→
LAG
End of adjustment
If adjustment is OK, Step 4.
If adjustment is NG, Step 7.
Step 4
Adjustment value output
[ _ C O M P L E T E _ ]
Press the MD PLAY button.
STEP 5
Press the MD STOP button.
STEP 2
1. AUTO pre-adjustment mode (Low reflection disc only)
Step No.
Setting Method
Remarks
Display
Step 1
Test mode STOP state
[ t s m
e
]
Step 2
Press once the MD REC button.
AUTO pre-adjustment menu
[
ATU YOBI
]
Step 3
Press once the MD PLAY button. The slide moves to the innermost periphery, and automatic
[
: _ _ _ _ _ _ ]
pre-adjustment is started.
• During automatic adjustment
changes as follows.
HAo
→
RFg
→
SAg
→
SBg
→
PTG
→
PCH
→
GTG
→
GCH
→
RCG
→
SEG
→
RFG
→
SAG
→
HAO
→
HEO
→
TCO
→
LAO
End of adjustment
If adjustment is OK, Step 4.
If adjustment is NG, Step 5.
Step 4
Grating adjustment,
[ _ C O M P L E T E _ ]
adjustment value output
Press once the MD STOP button. STEP 2
Step 5
Adjustment value output
[ A U T Y O B I ]
Press once the MD STOP button. STEP 2 AUTO pre-adjustment menu
•
: Adjustment name,
: Address
• Test Mode
1. AUTO pre-adjustment mode
• Automatic pre-adjustment is performed. (After adjustment the grating adjustment mode is set.)
• The adjustment value is output with the aid of system controller interface.
2. AUTO adjustment mode
• Automatic adjustment is performed.
• The adjustment value is output with the aid of system controller interface.
• Continuous playback is performed. (Error rate indication, jump test)
3. RESULT sub-mode*
• The measurement value, set value and calculated value are indicated.
• The set value is changed manually (in servo OFF state).
4. RESULT mode (final adjustment)*
• The set value (after calculation) is indicated.
• The set value is changed manually (in servo OFF state).
5. MANUAL pre-adjustment mode*
• RF side manual adjustment is performed.
• Focus and tracking signal ATT manual adjustment is performed.
• Focus and tracking signal offset setting is performed.
6. MANUAL adjustment mode*
• Focus
• Don't adjust.
and tracking signal ATT manual adjustment is performed.
7. EEPROM setting mode*
8. TEST-PLAY mode*
• Continuous playback from the specified address is performed.
• C1 error rate measurement,
* This mode is not used for service.
9. TEST-REC mode*
• Continuous recording from the specified address is performed.
• Change of record laser output (servo gain is also changed according to laser output)
10. EJECT mode*
• TEMP setting (of EEPROM setting)
Step 5
Continuous playback (groove section)
[ a
c
]
Step 6
Press the MD STOP button.
STEP 2 AUTO adjustment menu
Step 7
Adjustment value output
[ C a n ' t _ A D J . ]
Press the MD STOP button.
STEP 2 AUTO adjustment menu
•
: Adjustment name,
: Measurement value,
: Address
Step No.
Setting Method
Remarks
Display
Figure 1-1 Optical Pickup Grating Deviation
Measuring Method
Mechanism Adjustment
1. Optical pickup grating inspecting method
After the automatic adjustment is performed in the AUTO
mode (test mode) with the aid of high refection MD disc
("COMPLATE" is displayed), the Lissajous's waveform (x-y) is
adjusted.
1. Slightly loosen the 3 screws of spindle moto, and maken an
adjustment, observing the Lissajous's waveform.
2. After adjustment tighten the screw in order of 1 , 2 , 3 .
OSILLOSCOPE
GND CH1
CH2
X
Y
43 pin of IC 1101
GND
26 pin of IC 1101
EOUT
25 pin of IC 1101
FOUT
100K
470p
470p
a
b
LISSAJOUS'S WAVEFORM
Less thana:b = 3:1
100K
Figure 1-2
1
2
3
1
2
3
adjusting
hole
Spindle motor
Check the Lissajou's waveform,
shifting the mounting position with
a screwdriver (to be fitted into the
disc motor adjusting hole).
Spindle Motor
Adjusting hole
2. Jitter adjustment and checking method
Figure 1-3 Jitter connection diagram
jitter Meter
3pin of IC 1201 (TP1274)
EFMMON
13 pin of IC 1201 (TP1275)
GND
After performing automatic adjustment in AUTO mode of
TEST mode using the low reflection MD disc, check this jitter
in pit continuous playback and groove continuous playback
mode.