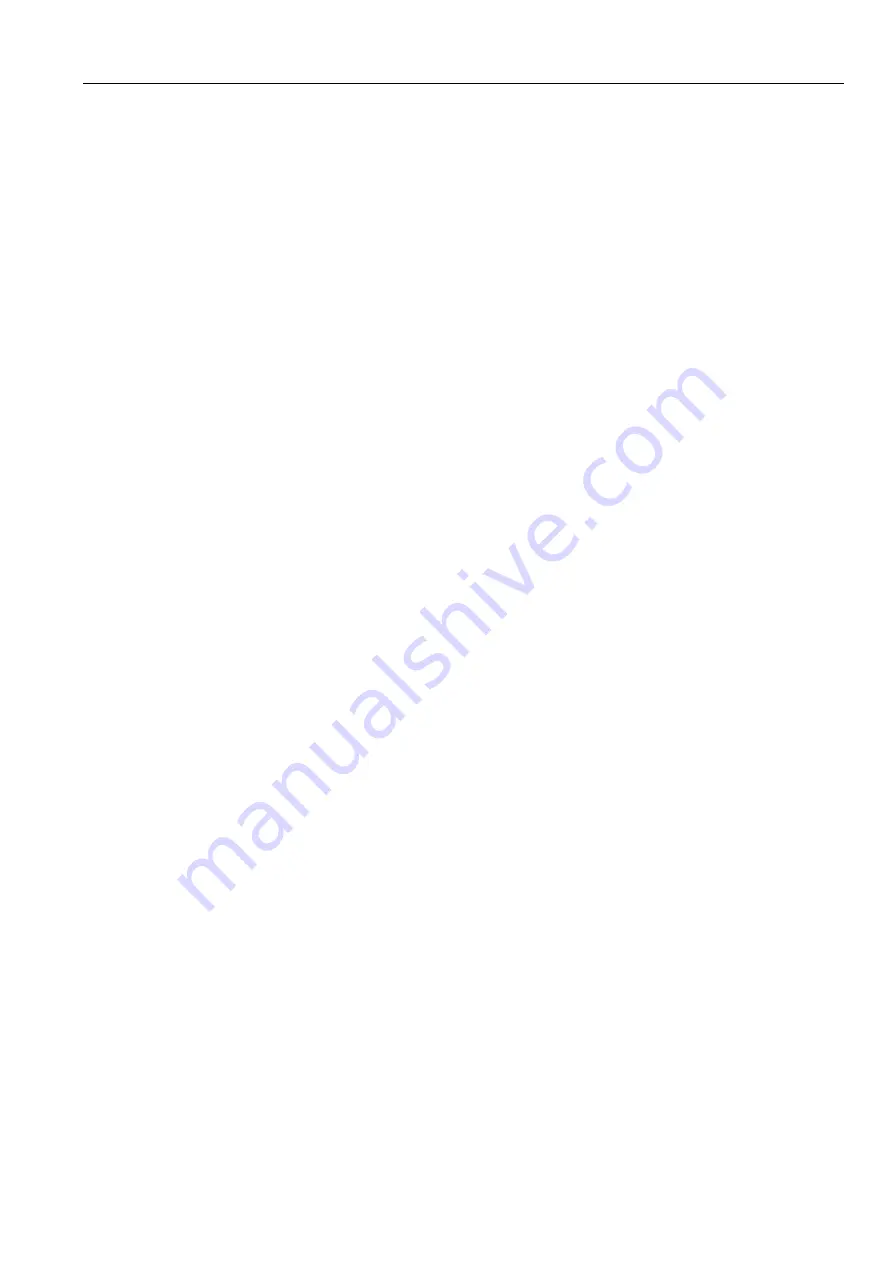
Kelly KLS8080N/NPS Sinusoidal Brushless Motor Controller User
’s Manual
V 1.10
19
function only helps motor stop rolling back too fast.
Suggestion: factory default is Disable.
(28)Change Direction:
If the direction is not what you expected after finish the Identification angle operation, please
just choose Change Direction item.
Please click Write button to activate Change Direction function. The motor direction will be what
you expected after the power supply is reset.
Suggestion: factory default is Disable.
4.2 Step 2
(1)Motor Nominal Curr: When the controller is doing identification angle operation without load
on the motor shaft, there is a current requirement for identification operation. If the motor rated
power is very high, please increase this parameter to a higher value. Otherwise please keep it
at 80 by default. If the motor power is very low such as hundreds of watts, please reduce this
parameter to lower value to match the low power motor for identification angle operation.
(2)Motor Poles: Motor Poles, The pair pole number*2. Range: 2~128
Suggestion: Set according to the real motor poles on the nameplate of the motor, factory default
is at 8.
(3)Speed Sensor Type: Speed Sensor Type, 2:Hal, 3:Resolver(Reservation), 4:Line Hall. Range:
2 or 4
Different sensors type. By defualt,it is set at 2
If you have a motor with 5V,Sin/Cosin, GND speed sensors, please choose it at 4.And please
inquire the KLS-8080NPS model before ordering.KLS-8080NPS can not support Resolver
sensor type for now.
(4)Resolver Poles: Resolver Poles, The pair pole number*2. Range: 2~32
It is only used for the Resolver sensor type which is not accepted by KLS-8080NPS controller
for now.
(5)Motor Temp Sensor: Motor Temp Sensor, 0
:
None,1:KTY84-130 or 150,2:KTY83-122.Range
0-2
High Temp Cut Out
°
C: Motor High Temp Cut Out, nominal value 130
°
C. Range: 60~170
Resume
°
C: Motor High Temp Resume Temp, nominal value 110
°
C. The controller will
resume work when the motor temp is at 110 degrees inside. Range: 60~170
(6)Line Hall Zero: It is only useful when the speed sensor is at 4.
Zero-Crossing point of Sine/Cosine linear hall sensors output signal. Usually the Sine/Cosine
speed sensor supplier provided sensors with 2.5V or 3.0V zero-crossing point.
You can change it back between 2.5V and 3.0V if the motor can not run.