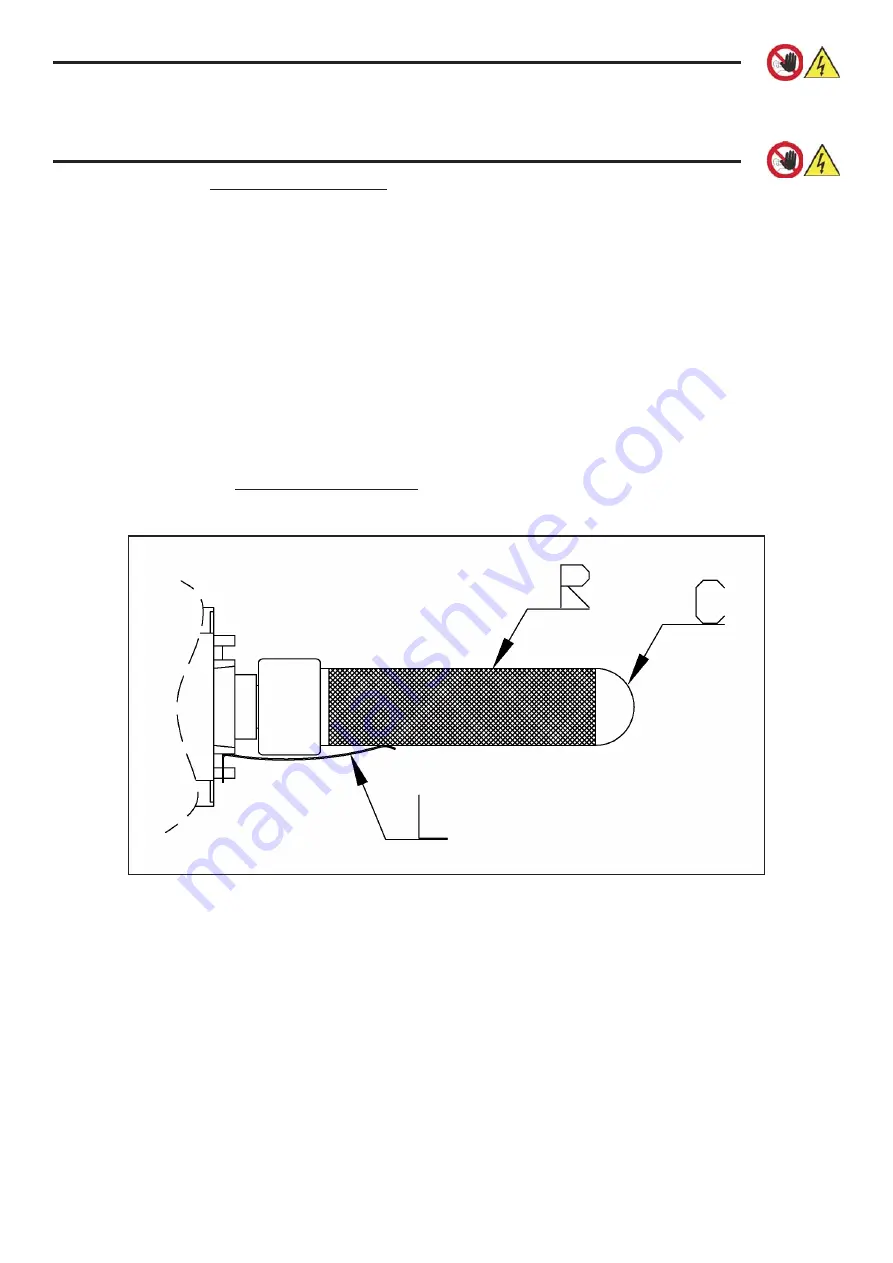
7.3 Yearly checks
• Verification of the whole electrical installation and in particular the tightening of the cable connections.
• Verification of the tightening of all bolts, nuts, flanges and water connections that could be loose because of vibrations.
7.3.1 BIOX-DX purifying system check
Once a year at least or when a drop in purifying efficiency is felt cleaning of capacitor shall be done.
In order to service BIOX-DX system, following instructions shall be carried out :
• Switch off the whole unit (main power supply off)
• Unscrew the 4 fixing screws of BIOX-DX system, operating from the lower side of the unit close to supply air duct connection
• Drop off the module (accomodating its fall) until the quartz capacitor is fully out of the unit
• Unlock the electric connector
• After laying the module on a flat surface, unscrew carefully the quartz capacitor (
C
)
• Remove the external net (
R
); if it should be difficult, rotate it lightly around the capacitor
• Clean the capacitor with a wet cloth.
• Wash the net with a jet of hot water and dry thoroughly with a dry cloth
• If the pipe is damaged, it shall be replaced with a new one
• As soon as a whitish layer is over the metal grille inside the pipe, capacitor shall be replaced. Usual time for replacement is 18-24 months
• Fit the net on the pipe and over the internal grille.
• Check that tab (
L
) is in contact with the metal net and push it against the glass of the capacitor (
C
)
• Clean the equipment all around outside
• Screw softly the capacitor in its seat
• Insert the module across the lower hole and lock the electric connector
• Screw the fixing screws
• Check if the system is working. Now a light noise might be audible.
pag.
2
9
Содержание KRE-1000DX1
Страница 1: ...KRE 500DX1 KRE 1000DX1 INSTALLATION USER MAINTENANCE MANUAL Cross flow heat recovery ...
Страница 32: ......