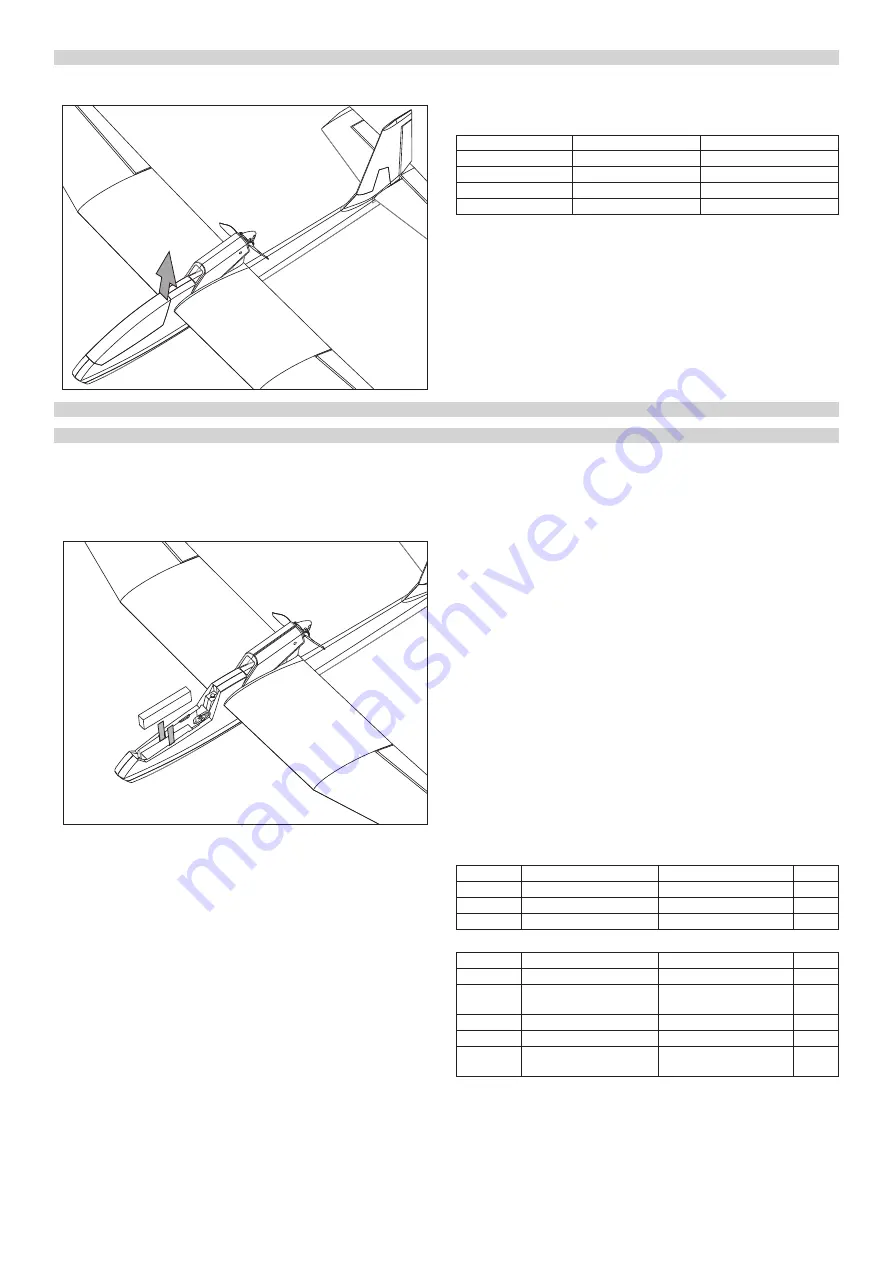
4
PREFLIGHT CHECK
CHECKING THE CURRENT SET-UP
1. Assure that the transmitter is turned on (both the LEDs are on with the
T8FB), place all the trims in their neutral positions and set the throttle stick
into the lowest position. Connect the flight pack to the ESC - the red LED on
the receiver must glow. If it blinks or does not glow at all, the receiver and
transmitter require establishing their link by the binding procedure - refer to
the page 6 in this manual.
2. Checking the control surface neutrals
Please check all the control surfaces are in the neutral position if the corre-
sponding transmitter sticks and trims are in the centre position. If not, please
loosen the setting screw of the corresponding push rod connector and set
the control surface to the neutral position. The elevator and rudder has to be
flush with the horizontal stabilizer resp. the fin, both two ailerons have to be
flush with the wing trailing edge. Once satisfied, apply a drop of threadlocker
to the setting screw a tighten it.
CAUTION:
If the quick link got loose during flight, your model could become
partly or completely uncontrollable. Therefore, you should check the linkage
regularly.
3. Testing the Ailerons
A) Move the aileron stick to the left; (looking from the tail to the nose) the left
aileron must move up and the right aileron must drop down simultaneously.
B) Move the aileron stick to the right; the left aileron must drop down and the
right aileron go up simultaneously.
C) Return the aileron stick to the centre (neutral) - both two ailerons will re-
turn to the neutral position.
Note: If the ailerons are moving in the opposite direction, you will have to
reverse the direction by flipping the aileron reverse switch (AIL) on your
transmitter.
4. Testing the Rudder
A) Move the rudder stick to the left; (looking from the tail to the nose) the
rudder must move to the left.
B) Move the rudder stick to the right; the rudder must move to the right.
C) Return the ruder stick to the centre (neutral) - the rudder will return to the
neutral position.
Note: If the rudder is moving in the opposite direction, you will have to re-
verse the direction by flipping the rudder reverse switch (RUD) on your trans-
mitter.
5. Testing the Elevator
A) The elevator stick is located on the left side on the Mode 1 transmitter or
on the right side on the Mode 2 transmitter. Pull the elevator stick down; the
elevator must move up).
B) Push the elevator stick up; the elevator must move down.
C) Return the elevator stick to the centre (neutral) - the elevator will return to
the neutral position.
Note:
If the elevator is moving in the opposite direction, you will have to
reverse the direction by flipping the elevator reverse switch (ELE) on your
transmitter.
6. Control Surface Throws
If you carefully followed the instruction in the previous sections of this man-
ual, the correct default control surface throws has been set automatically.
The control throws are set by the ratio between the length of the servo arm
and the control surface throw - the actual throws set this way are listed in the
column “Normal Rate” in the table below. (
The throws are always measured
in the widest point of the particular control surface.
) It is always better to try
to reach the requested throws mechanically, adjusting the arm/horn length
ratio - even if you have got a fancy computer radio. If you got such a transmit-
ter you can use the function “Dual Rate” (D/R) to get even more forgiving set-
up - please refer to the “Low Rate” column. You can also do it mechanicaly
- simply move the push rod Z-bends on the servo arms closer to the centre.
A. A radio featuring only one aileron channel
Control
Low Rate
Normal Rate
Expo*
Aileron
7 mm up and down
10 mm up and down
10-20%
Rudder
10 mm left and right
12 mm left and right
0-10%
Elevator
6 mm up and down
8 mm up and down
20-30%
B. A radio featuring 2 independent aileron servo channels
Control
Low Rate
Normal Rate
Expo*
Aileron
8 mm up/4 mm down
10 mm up/5 mm down 10-20%
Aileron
(Airbrake)
13 mm up
13 mm up
-
Rudder
10 mm left and right
12 mm left and right
0-10%
Elevator
6 mm up and down
8 mm up and down
20-30%
Elevator
(Airbrake)
2 mm up
2 mm up
-
*Expo – set to decrease the sensitivity around the neutral (Futaba, Hitec, Radi-
olink, Multiplex: -10/-20, Graupner: +10/+20 etc.)
7. Testing the Power system
KAVAN T8FB/R-20B: Check the throttle channel reverse switch (THR) is in the
“N“ (up) position on the transmitter. Now perform the throttle range calibra-
tion procedure as described in the KAVAN R-20B manual (refer to the attach-
ment) and check the motor brake function has been turned on.
A) Turn on the transmitter, set the throttle stick to the lowest position, con-
nect the flight pack to the ESC in the model (ESC has to be set to the “Brake
RC SET INSTALLATION
Now you have to install/connect your receiver, servos and electronic speed
controller (ESC).
1. Remove the canopy; lift the rear part up to disengage the magnetic lock.
2. Following you radio instruction manual connect the servos and ESC to
your receiver – the table shows the channel assignment of the T8FB radio
supplied in the RTF kit:
Connector Label
Function
Receiver Channel (T8FB)
AILE
Ailerons
CH1
ELEV
Elevator
CH2
ESC
Throttle
CH3
RUDD
Rudder
CH4
3. Put your receiver into the fuselage (into the rear part of the cockpit); you
can secure it using a strip of hook-and-loop tape to the fuselage.
4. The flight battery pack is to be inserted into the nose of your BETA 1400
and secured by the hook-and-loop tape to the fuselage - the exact po-
sition of the battery pack will be determined later during the Centre of
Gravity position check.
CAUTION: Always turn on your transmitter first and only then connect
the flight pack to the ESC. From now on always handle your model as if
the motor might burst into life and the propeller start to spin anytime!