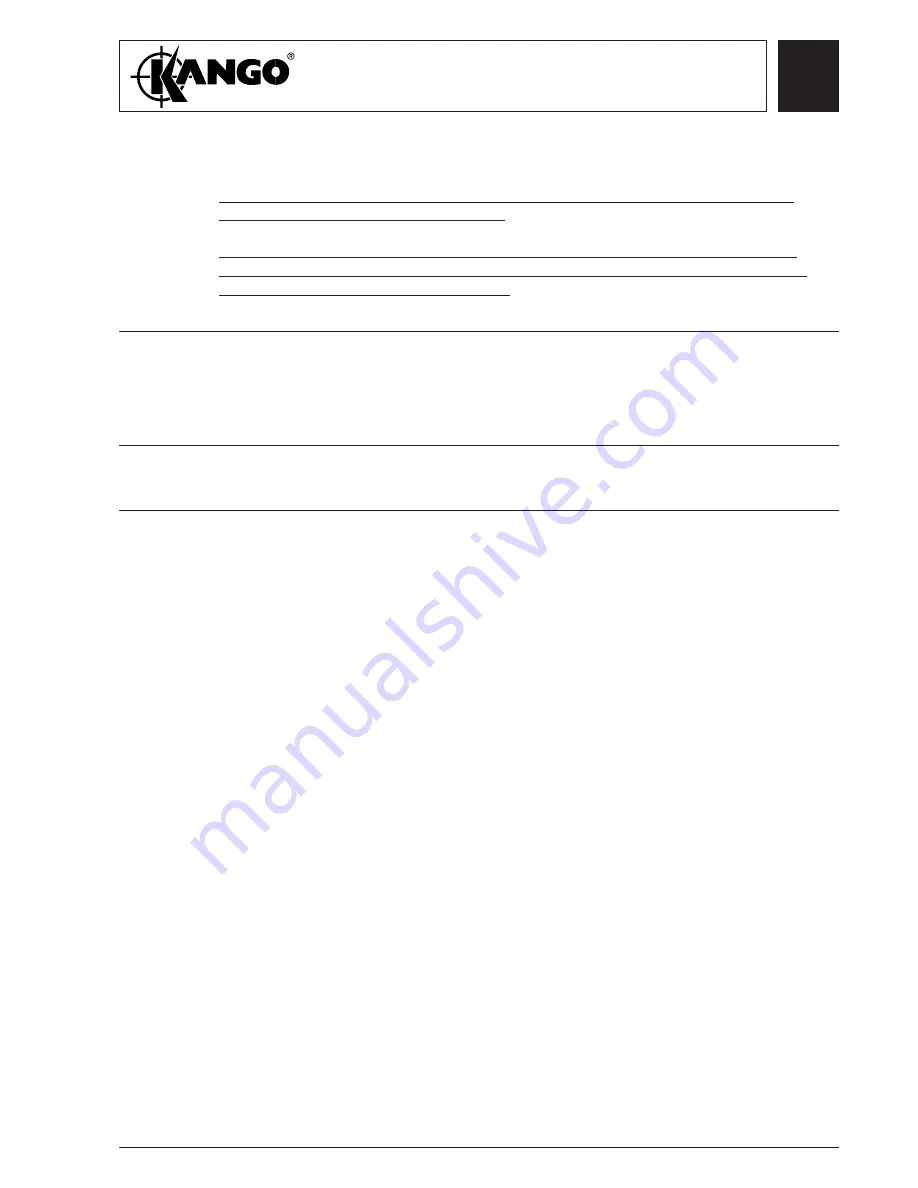
13
Service and Repair Manual
Model 810V
General
For best performance hammers should be serviced at regular intervals, any indication that the hammer is
not performing as specified should be investigated to prevent any adverse damage occurring.
ALL SEALS, GASKETS, GREASE OR OTHER PARTS DEEMED NECESSARY FOR
SERVICING ARE IN THE SERVICE KIT.
ALL NEEDLE ROLLER BEARINGS SHOULD BE PRESSED WITH THE ROUNDED
EDGE ENTERING THE BORE FIRST, AND THE PRESS TOOL PRESSING AGAINST
THE FLAT SURFACE OF THE BEARING.
Cleaning
All mechanical parts with the exception of any sealed bearings should be cleaned in a suitable cleaning
fluid. Electrical parts should be cleaned by the use of compressed air.
PRECAUTIONS MUST BE TAKEN FOR PERSONAL SAFETY THE USE OF EYE
PROTECTION AND GLOVES IS RECOMMENDED.
Inspection
All mechanical and electrical parts should be inspected for wear and replaced as required.
Содержание 810
Страница 1: ......