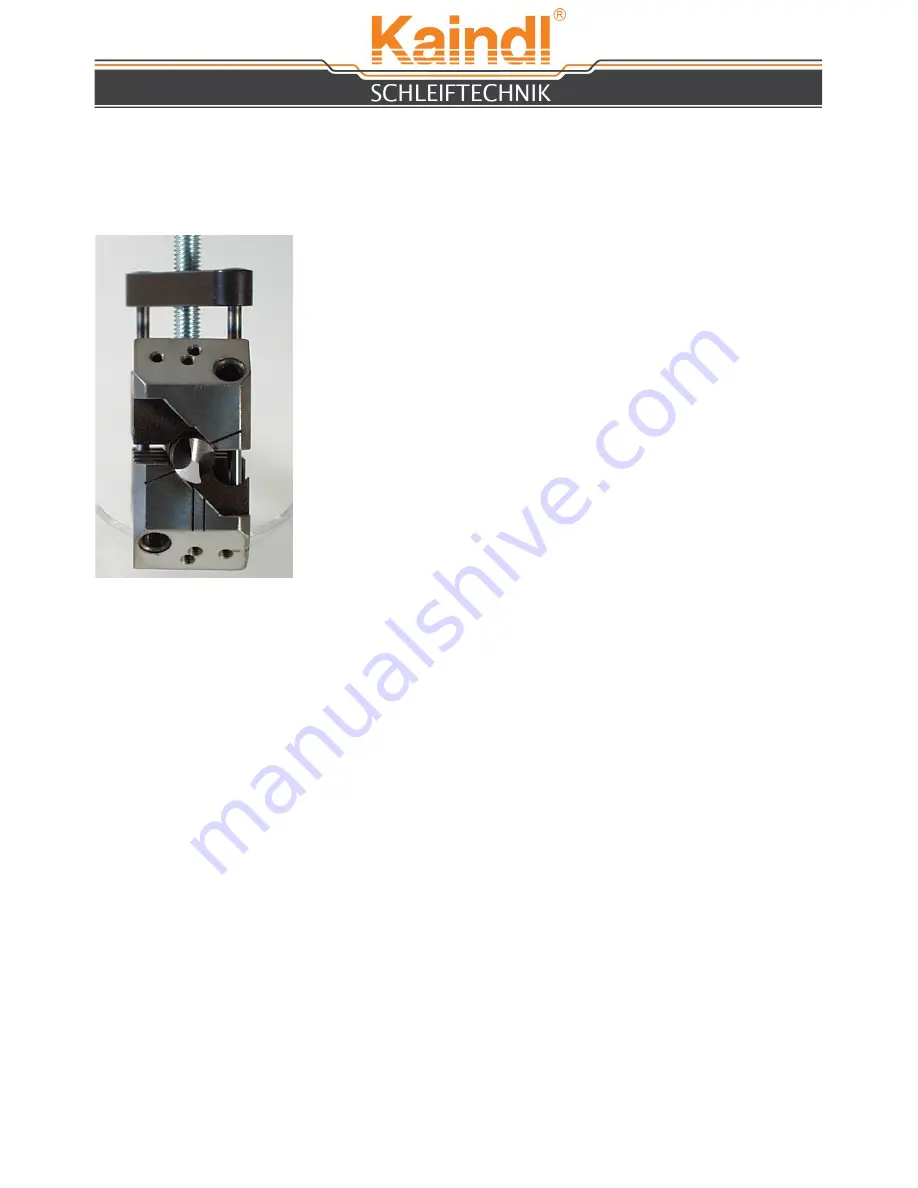
1 3.
GRINDING OF DRILLS
PLACING AND ADJUSTMENT OF DRILLS
The reversing prism comprised a range of 2-20 mm. The
insertion and alignment of the drill is achieved in the most
simple manner conceivable. Open the prism by means of the
knurled head screw, provided for this purpose. Now insert the
drill to be ground inside the prism.
Keep the drill projecting about 1 5 - 20 mm beyond the prism
edge. The prism jaws are pressed together by a slight turn of
the knurled screw. The thus inserted drill is held tight in this
position, but it can still be turned easily as this is important for
the alignment. Now it is only neccessary to align the cutting
edge of the drill in parallel to the two indicated marks
(
Mark A
= right-hand drills;
Mark B
= left-hand drills).
The prism is to be tightened by hand only a hereafter, the
grinding operation can be started.
1 2
In order to work always in conformity with the properties of the material, you have the
opportunity no adjust every top angle that is imaginable.
The common top angle are 11 8°, 1 30° and 1 80° degrees.
The angles are solidly marked on the prism slide. They can easily adjusted by opening
the clamping lever (see picture on page 5, No. 6) and by moving the prism rest.
1 4.
ADJUSTMENT OF THE TOP ANGLE
Deviating from this basic adjustment, you can change your relief angle depending on the
material to be drilled.
You want a higher clearance angle - a higher cutting capacity, then revolve the drill
slightly to the left (shorter graduation mark on the prism). If you want less relief - a lower
cutting capacity, then revolve the drill slightly to the right (longer graduation mark on the
drill). You will thus obtain the correct cutting edge and angle for every kind of material.
In case of a broken drill, having no cutting edge for adjustment, grind the drill to get a
truncated end. Align the cutting corners as closely as possible to the adjustment marks
and regrind the drill until a new cutting edge apears. Thereafter the adjustment is to be
carried out as before.
B
B
A