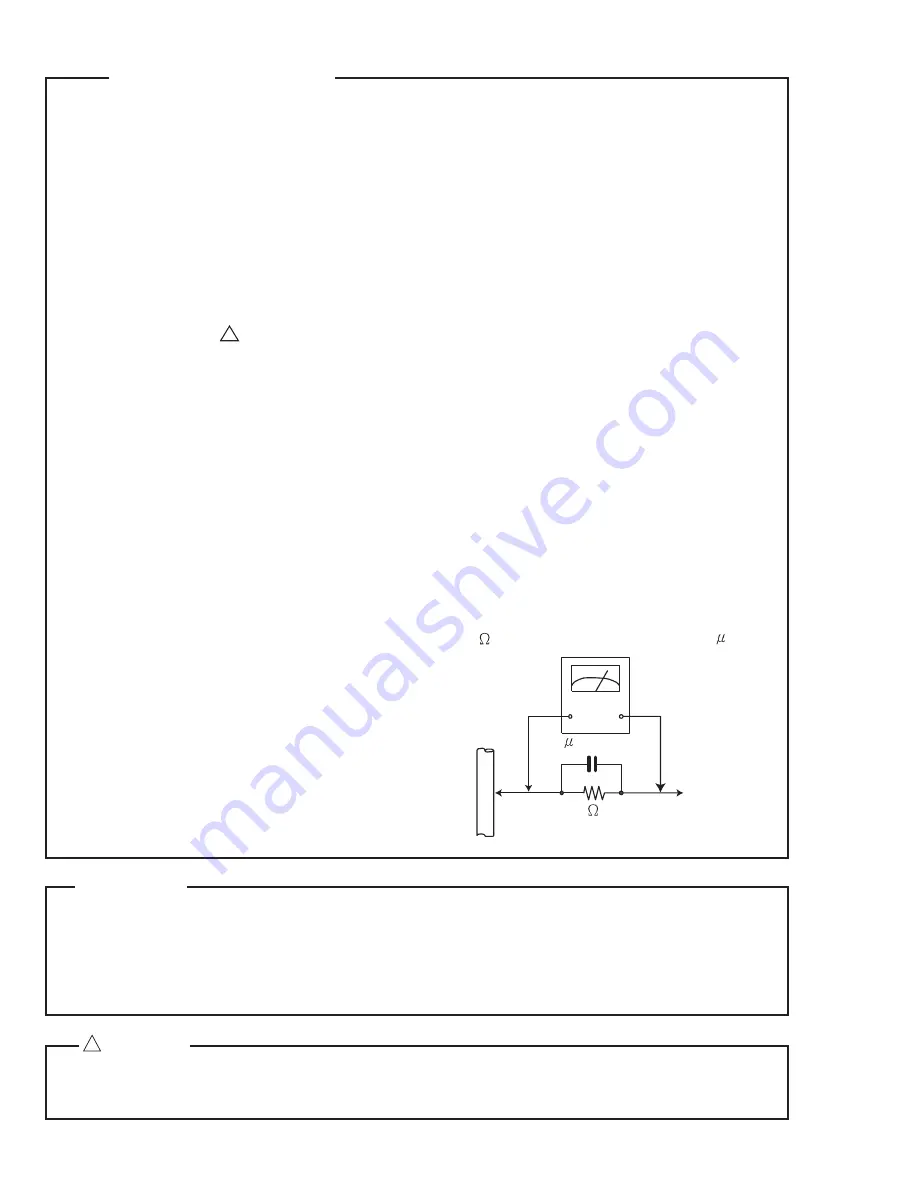
TH-A35
1-2
Warning
!
CAUTION
Good earth ground
Place this
probe on
each exposed
metal part.
AC VOLTMETER
(Having 1000
ohms/v
1500 10W
olts,
or more sensitivity)
0.15 F AC TYPE
Safety Precautions
1. This design of this product contains special hardware and many circuits and components specially for
safety purposes. For continued protection, no changes should be made to the original design unless
authorized in writing by the manufacturer. Replacement parts must be identical to those used in the
original circuits. Services should be performed by qualified personnel only.
2. Alterations of the design or circuitry of the product should not be made. Any design alterations of the
product should not be made. Any design alterations or additions will void the manufacturer's warranty
and will further relieve the manufacture of responsibility for personal injury or property damage resulting
therefrom.
3. Many electrical and mechanical parts in the products have special safety-related characteristics. These
characteristics are often not evident from visual inspection nor can the protection afforded by them
necessarily be obtained by using replacement components rated for higher voltage, wattage, etc.
Replacement parts which have these special safety characteristics are identified in the Parts List of
Service Manual. Electrical components having such features are identified by shading on the
schematics and by (
!
) on the Parts List in the Service Manual. The use of a substitute replacement
which does not have the same safety characteristics as the recommended replacement parts shown in
the Parts List of Service Manual may create shock, fire, or other hazards.
4. The leads in the products are routed and dressed with ties, clamps, tubings, barriers and the like to be
separated from live parts, high temperature parts, moving parts and/or sharp edges for the prevention
of electric shock and fire hazard. When service is required, the original lead routing and dress should
be observed, and it should be confirmed that they have been returned to normal, after re-assembling.
5. Leakage currnet check (Electrical shock hazard testing)
After re-assembling the product, always perform an isolation check on the exposed metal parts of the
product (antenna terminals, knobs, metal cabinet, screw heads, headphone jack, control shafts, etc.)
to be sure the product is safe to operate without danger of electrical shock. Do not use a line isolation
transformer during this check.
Plug the AC line cord directly into the AC outlet. Using a "Leakage Current Tester", measure the
leakage current from each exposed metal parts of the cabinet, particularly any exposed metal part
having a return path to the chassis, to a known good earth ground. Any leakage current must not
exceed 0.5mA AC (r.m.s.)
Alternate check method
Plug the AC line cord directly into the AC outlet. Use an AC voltmeter having, 1,000 ohms per volt or
more sensitivity in the following manner. Connect a 1,500 10W resistor paralleled by a 0.15 F AC-
type capacitor between an exposed metal part
and a known good earth ground. Measure the AC
voltage across the resistor with the AC voltmeter.
Move the resistor connection to each exposed
metal part, particularly any exposed metal part
having a return path to the chassis, and meausre
the AC voltage across the resistor. Now, reverse
the plug in the AC outlet and repeat each
measurement. Voltage measured Any must not
exceed 0.75 V AC(r.m.s.). This corresponds to 0.5
mA AC(r.m.s.).
1. This equipment has been designed and manufactured to meet international safety standards.
2. It is the legal responsibility of the repairer to ensure that these safety standards are maintained.
3. Repairs must be made in accordance with the relevant safety standards.
4. It is essential that safety critical components are replaced by approved parts.
5. If mains voltage selector is provided, check setting for local voltage.
Burrs formed during molding may be left over on some parts of the chassis. Therefore,
pay attention to such burrs in the case of preforming repair of this system.
Содержание TH-A35
Страница 12: ...TH A35 1 12 2 PIN CONFIGURATION WM8770 U1 8 channel code c volume control 1 ...
Страница 13: ...TH A35 1 13 1 Block Diagram UPD78F0034A IC 401 CPU ...
Страница 14: ...TH A35 1 14 2 Outline of Function ...
Страница 15: ...TH A35 1 15 1 BLOCK DIAGRAM UPD 16315 IC904 VFD control ler driver Description of major ICs ...
Страница 16: ...TH A35 1 16 2 Pin Layout AK4112BVF AK4112 U17 Digital audio receiver 1 BLOCK DIAGRAM ...
Страница 20: ...TH A35 1 20 Wiring connection ...
Страница 21: ...TH A35 1 21 M E M O ...