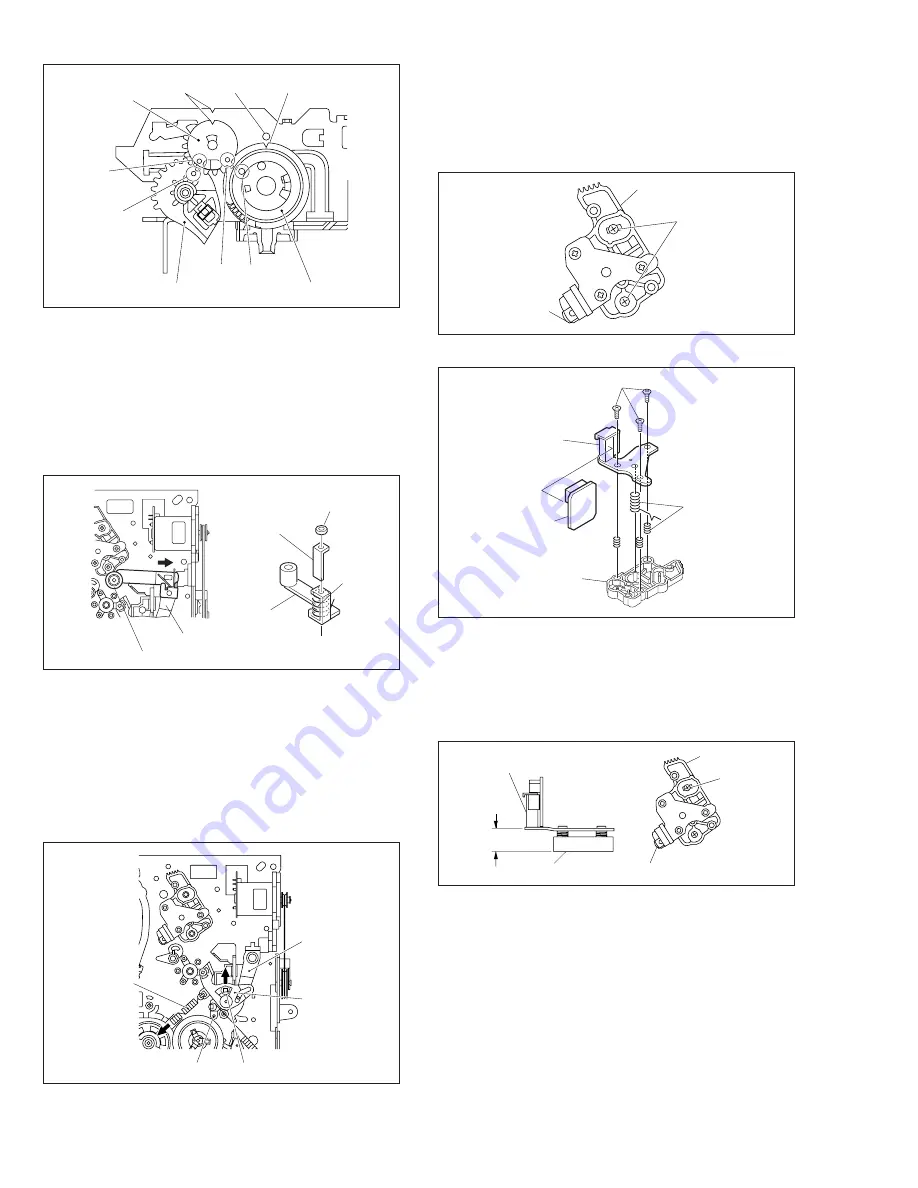
2-8
2.2.7
Loading motor
1. How to remove
(1) Remove the belt wound around the worm gear.
(2) Open the two lugs of the motor guide and remove the
loading motor, loading motor board assembly and motor
guide altogether by pulling them up.
(3) When replacing the loading motor board assembly, take
care with the orientation of the loading motor. (Install so
that the loading motor label faces upward.)
(4) When the motor pulley has been replaced, choose the
fitting dimension as indicated in Fig.2-2-7a.
2.2.4
Pinch roller arm assembly
1. How to remove
(1) Remove the spring from the hook of the press lever as-
sembly.
(2) Remove the slit washer and remove the pinch roller seat
2. (See Fig.2-2-4a.)
(3) Remove the pinch roller arm assembly by pulling it up.
Fig. 2-2-5a
2.2.6
A/C head
1. How to remove
(1) Remove the two screws (A) and remove the A/C head
together with the head base.
(2) When replacing only the A/C head, remove the three
screws (B) while controlling the compression spring.
Fig. 2-2-6a
Fig. 2-2-6c
Fig. 2-2-4a
2.2.5
Guide arm assembly and press lever assembly
1. How to remove
(1) Remove the spring and expand the lug of the lid guide in
the arrow-indicated direction. Then remove the guide arm
assembly by pulling it up.
(2) Remove the press lever assembly by pulling it up. (See
Fig.2-2-5a.)
Tension
spring
Press lever
assembly
Guide arm
assembly
Lug
Lid guide
Head base
Screws(A)
A/C head
Compression
springs
Head base
A/C head board
assembly
A/C head
Screws(B)
Fig. 2-2-6b
2. How to install
(1) To make the post-installation adjustment easier, set the
temporary level as indicated in Fig.2-2-6c. Also make sure
that the screw center (centre) is brought into alignment
with the center (centre) position of the slot.
Head base
Head base
Screw
A/C head
A/C head
12.4 mm
Pinch roller seat2
Pinch roller arm
assembly
Pinch roller arm assembly
Slit washer
Spring
Press lever assembly
Fig. 2-2-3i
Relay gear
Drive gear
Limit gear
Guide hole
Notches
Notch
B
A
A
B
Содержание HR-J3008UM
Страница 23: ......
Страница 24: ...VICTOR COMPANY OF JAPAN LIMITED VIDEO DIVISION Printed in Japan S40894 ...