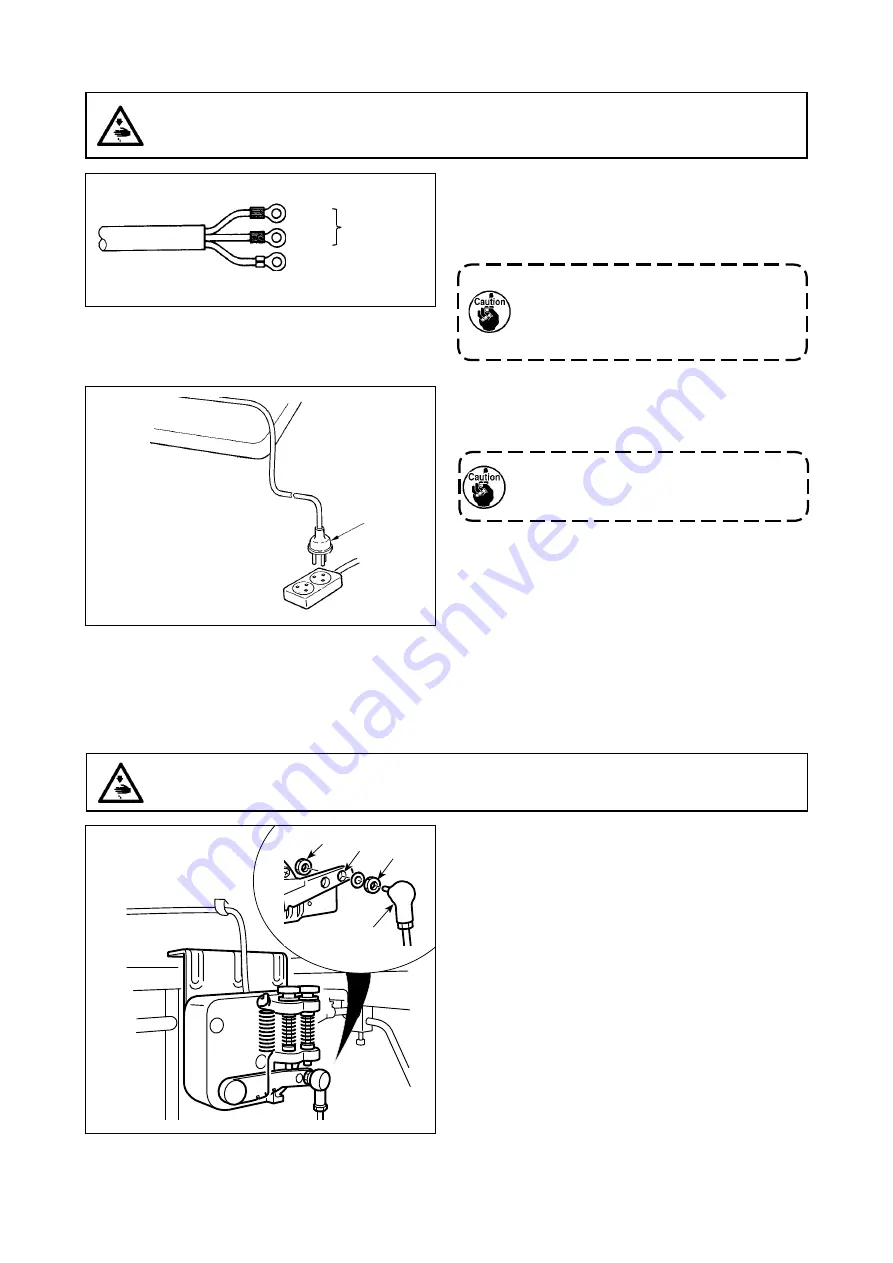
– 6 –
6. Attaching the connecting rod
Fix connecting rod
❶
to installing hole of pedal lever
❷
with nut
❸
.
5. How to install the power plug
WARNING :
1. Be sure to attach the ground wire (green/yellow) to the specified location (on the ground side).
2. Take care not to allow terminals to come in contact with each other.
WARNING :
To protect against possible personal injury due to abrupt start of the machine, be sure to start the
following work after turning the power off and a lapse of 5 minutes or more.
❶
❷
❸
❸
1) Connect the power cord to power plug
❶
. Con-
nect the blue and brown wires (1ø) to the power
supply side and the green/yellow wire to the
earth side as illustrated in the figure.
1. Be sure to prepare the power plug
❶
which conforms to the safety standard.
2. Be sure to connect the ground lead
(green/yellow) to the grounding side.
Blue
Brown
Green / Yellow
(ground wire)
AC 220-240V
1ø 220-240V
2) Check that the power switch is in the OFF state.
Then, insert the power plug
❶
coming from the
power switch into the plug receptacle.
In prior to the connection of the power
plug
❶
, re-check the supply voltage spec-
ification indicated on the control box.
* The power plug
❶
is different in shape ac-
cording to the destination of the sewing
machine.
❶
Содержание DDL-900A
Страница 1: ...COVERI DDL 900A INSTRUCTION MANUAL ...