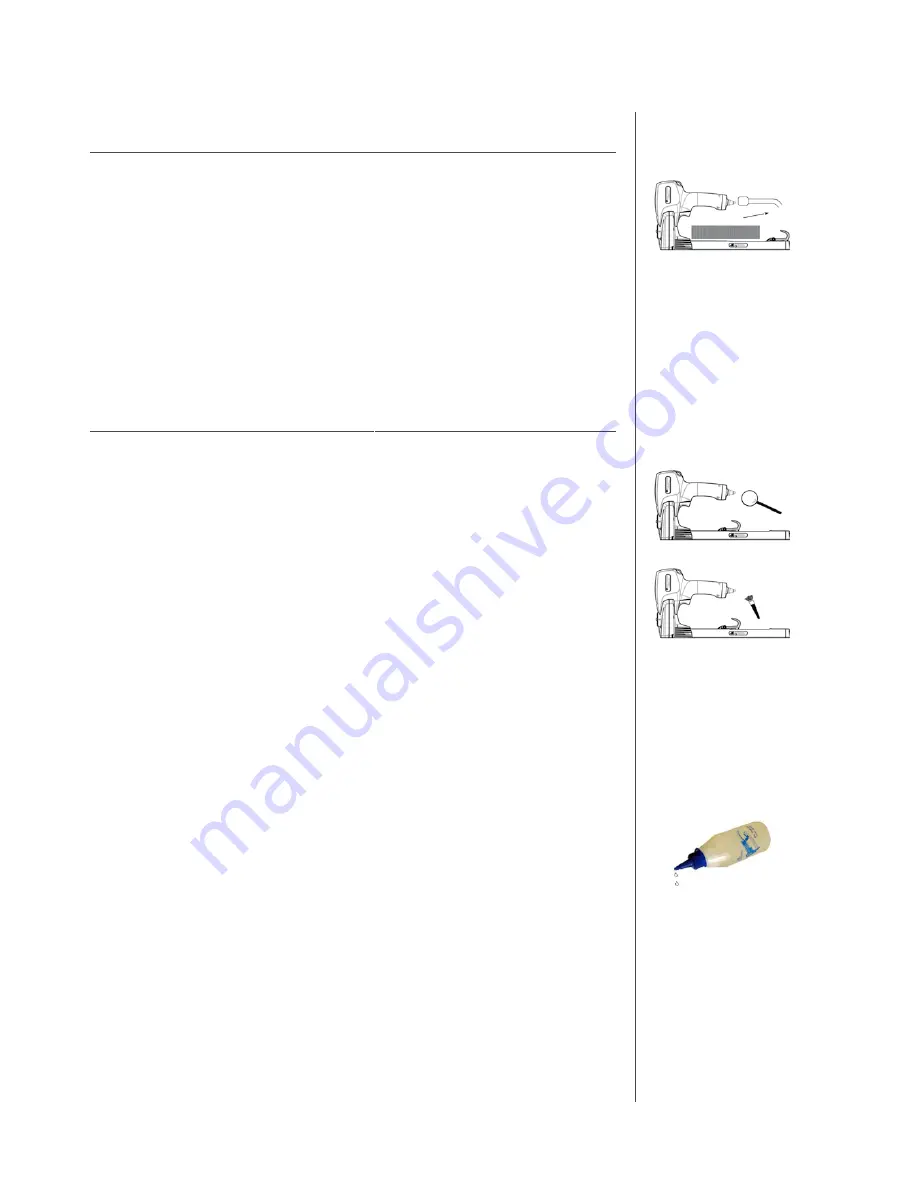
8
© Josef Kihlberg AB 2007
Troubleshooting
Always disconnect the tool from the air supply, empty the
magazine and read the
Safety precautions
section before
you begin troubleshooting. Normally it is not necessary to
dismantle any parts in order to remove a defective staple
from the front nozzle plate. Grip the staple with a pair of flat-
nosed pliers at the exit from the front nozzle plate. Carefully
pull out the staple.
All safety devices must be inspected daily to ensure that
they are working properly. Make especially sure that:
the trigger and safety yoke move freely without binding;
all screws and nuts are securely tightened.
This tool does not require special servicing. It only needs
regular cleaning with a non-aggressive cleaning agent. Do
not remove any parts for cleaning purposes.
Apply a small amount of lubricating oil to the nipple of the
tool every day or approximately 10 drops once a week to
maximize the life and utility of the tool. For high-frequency
stapling, we recommend oil-mist lubrication. Please contact
our agent for advice. Oil recommendation.
Part no.:
1 litre
184314
0.2 litre
733007
Sliding parts have been lubricated with multipurpose
grease at the factory. We recommend using multipurpose
grease on moving parts after they have been cleaned or
replaced.
•
•
Maintenance
EN