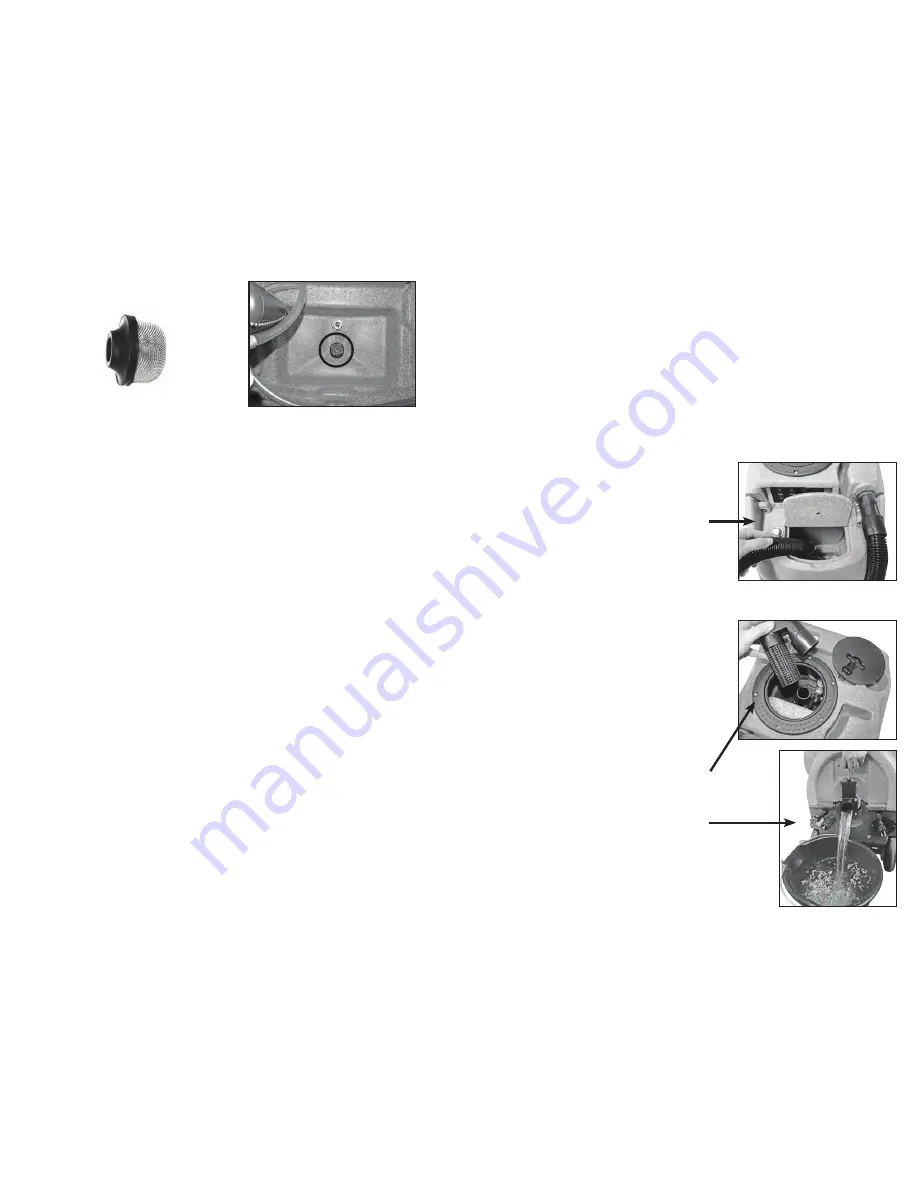
(10) 12-Gallon, 100 PSI Carpet Extractor
12-Gallon, 100 PSI Carpet Extractor (7)
4.0 Shutdown Procedures
• If using the auto-fill system, turn the water supply OFF before finishing each job.
This will allow use of the water and chemicals already in the tank and will reduce the
amount of excess water to be disposed of later.
• When finished cleaning, turn OFF all switches.
• If the auto-fill system was used and there is still water in the solution tank, push the
float down to release the water inlet hose pressure before disconnecting the hose from
the faucet. Disconnect the water inlet hose from the quick disconnect on the front of
the machine.
•
Disconnect the solution hose and vacuum hose from the cleaning tool. Pull the valve
trigger to release pressure from the hose before disconnecting the solution hose from
the cleaning tool.
• Disconnect the clear view in-line filter from the vacuum hoses and clean the filter as
needed.
•
Disconnect the vacuum hose and solution
hose from the machine.
•
If water remains in the solution tank, use
the short vacuum hose and vacuum the
excess water from the tank.
• If the auto-fill system was utilized, place the
chemical feed hose back into the solution
tank.
•
If the dump-out system was used: turn the
waste pump switch ON to pump out any
remaining water from the recovery tank;
turn switch OFF, remove the dump pump-
out hose from the outlet fitting and replace
the cap; roll up the hose toward drain to
remove the remaining water from the hose;
connect ends of hose together to prevent
dirty water from dripping from hose during
transport.
•
Disconnect the power cords from the outlets
and from the machine.
• Remove the float assembly from the
recovery tank and clean filter as needed.
Replace float assembly and tank lid.
•
Drain any remaining water from the recovery
tank and dispose of in a sanitary drain. DO
NOT use the same bucket to drain the tank
that you used to fill the tank.
•
Roll up all hoses and tools. Collect and store
extractor, all tools and accessories.
5.4 Clean Pump Inlet Filter Continued
1/4” Acorn Strainer
Part No. 10-0845
5.5 WD-40 Vacuum Motors
Should moisture ever enter the vacuum motors, completely drain the recovery tank,
open the recovery tank lid, remove the vacuum float assembly, turn on both vacuum
motors and spray a five (5) second burst of WD-40 into the standpipe. Continue to
run the vacuum motors for at least three (3) minutes.
To prevent moisture from damaging the vacuum motors during storage, empty the
recovery tank and store with the lid open.
6.0 Storage and Freeze Protection
You must winterize your Carpet Extractor to protect the pump system from freezing
and also damage being caused to fittings and valves. Damage due to freezing is not
covered under the Warranty. Store your extractor in temperatures over 40 degrees
Fahrenheit. If you plan on storing your extractor in freezing conditions or for a long
period of time, the following procedure should help prevent your Carpet Extractor
from freezing and prevent pump and seals from drying out.
Recommended Procedure for Storage
•
In a separate container, mix 1/2-gallon of water with 1/2-gallon of automotive
radiator antifreeze (ethylene glycol type). Mix well and pour into the solution
tank.
•
Connect the pressure hose to the female quick disconnect (QD) on the front of
the machine. Insert an open-ended male QD into the female QD on the end of the
pressure hose.
•
When primed, turn down the pressure to 100 PSI.
•
Disconnect the open-ended QD and connect the solution hose to the male QD at
the auto-fill/chemical feed connection. CAUTION: applying high pressure (over
100 PSI) to the chemical feed system will damage the mechanism.
•
With the chemical feed supply tube at the bottom of the solution tank, turn on
the pump and allow to circulate for 10 minutes. Check to make sure the chemical
supply tube is drawing the antifreeze solution. This will introduce antifreeze into
the chemical feed system.