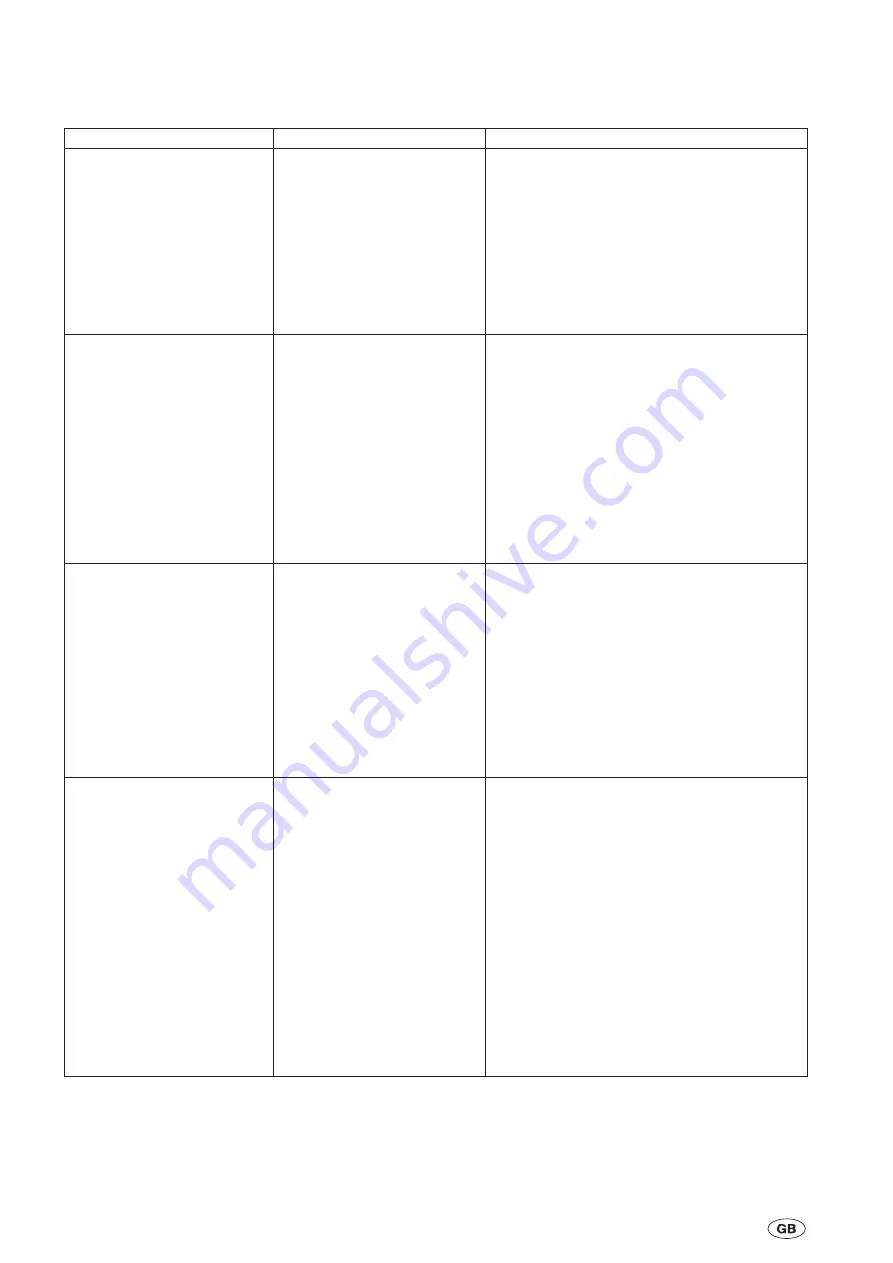
PROBLEM
POSSIBLE CAUSE
ACTION
High Discharge Pressure
Warm inlet water or insufficient
water flow through the condenser
Gas outlet valve on the condenser
not completely open
Overcharged refrigerant
Condenser plates coated with scale,
slime, corrosion
Suction pressure is higher than
standard
Open the valve
Check the valves, capillary tubes and strainer. Replace,
if necessary.
Purge the refrigerant.
Clean the condenser water plates with chemical cleaner
See "High Suction Pressure".
Low Discharge Pressure
Too much water flowing through the
condenser or water is too cold
Insufficient refrigerant charge
Leakage from the condenser gas
outlet valve
Liquid refrigerant flooding back from
the water cooler, causing oil to
foam.
Suction pressure is lower than
standard
Adjust the water cock or the regulating valve.
Check the operation of cooling tower.
Add refrigerant.
Check to determine how long it takes to balance high
and low.
Check the operation and adjustment of the expansion
valve. Check the feeler bulb is securely connected to the
suction pipe and that it is completely insulated.
Inlet water temperature is lower than the limited
temperature.
See "Low Suction Pressure"
High Suction Pressure
High discharge pressure
Refrigerant overcharged
Liquid refrigerant flooding back from
the water cooler
Leakage from the condenser gas
outlet valve
Insufficient insulation for the chilled
water piping
See "High Discharge Pressure"
Purge the refrigerant
Check the operation and adjustment of the expansion
valve. Check the feeler bulb is securely connected to the
suction pipe and completely insulated.
Inlet chilled water temperature to the unit is considerably
higher than the standard temperature.
Check the condenser gas outlet valve
Check the insulation of the piping
Low Suction Pressure
Condenser liquid outlet valve not
completely open
Expansion valve not properly
adjusted or faulty.
Inlet chilled water temperature is
considerably lower than standard
temperature.
Insufficient refrigerant charge
Excessive oil circulating in the
system
Insufficient chilled water flow
through the water cooler.
Low discharge pressure
Scales on water cooler plates
Open the valve.
Adjust for correct superheat. Check for loss of refrigerant
in the feeler bulb.
Check the insulation specifications
Add refrigerant
Check the oil charge
Check the chilled water piping lines for pressure loss.
Adjust the water shutoff valve
Clean the plates
8
-
2
035-21786-100 Rev. 1 (0909)
Содержание York YCRE 040
Страница 2: ......
Страница 49: ...9 3 035 21786 100 Rev 1 0909 Suction Pressure Evaporator Sub cooling Temperatures...
Страница 54: ...9 7 Clearances and Foundations 9 8 035 21786 100 Rev 1 0909...
Страница 55: ...9 8 Dimensions 9 9 035 21786 100 Rev 1 0909 Model YCSE 040...
Страница 56: ...9 10 035 21786 100 Rev 1 0909 Model YCSE 050...
Страница 57: ...9 11 035 21786 100 Rev 1 0909 Model YCSE 060...
Страница 58: ...9 12 035 21786 100 Rev 1 0909 Model YCSE 080...
Страница 59: ...9 13 035 21786 100 Rev 1 0909 Model YCSE 100...
Страница 60: ...9 14 035 21786 100 Rev 1 0909 Model YCRE 040...
Страница 61: ...9 15 035 21786 100 Rev 1 0909 Model YCRE 050...
Страница 62: ...9 16 035 21786 100 Rev 1 0909 Model YCRE 060...
Страница 63: ...9 17 035 21786 100 Rev 1 0909 Model YCRE 080...
Страница 64: ...9 18 035 21786 100 Rev 1 0909 Model YCRE 100...
Страница 66: ...This Page Intentionally Blank 10 2 035 21786 100 Rev 1 0909...
Страница 68: ...Subject to change without notice ALL RIGHTS RESERVED Form 035 21786 100 Rev 1 0909 www johnsoncontrols com...