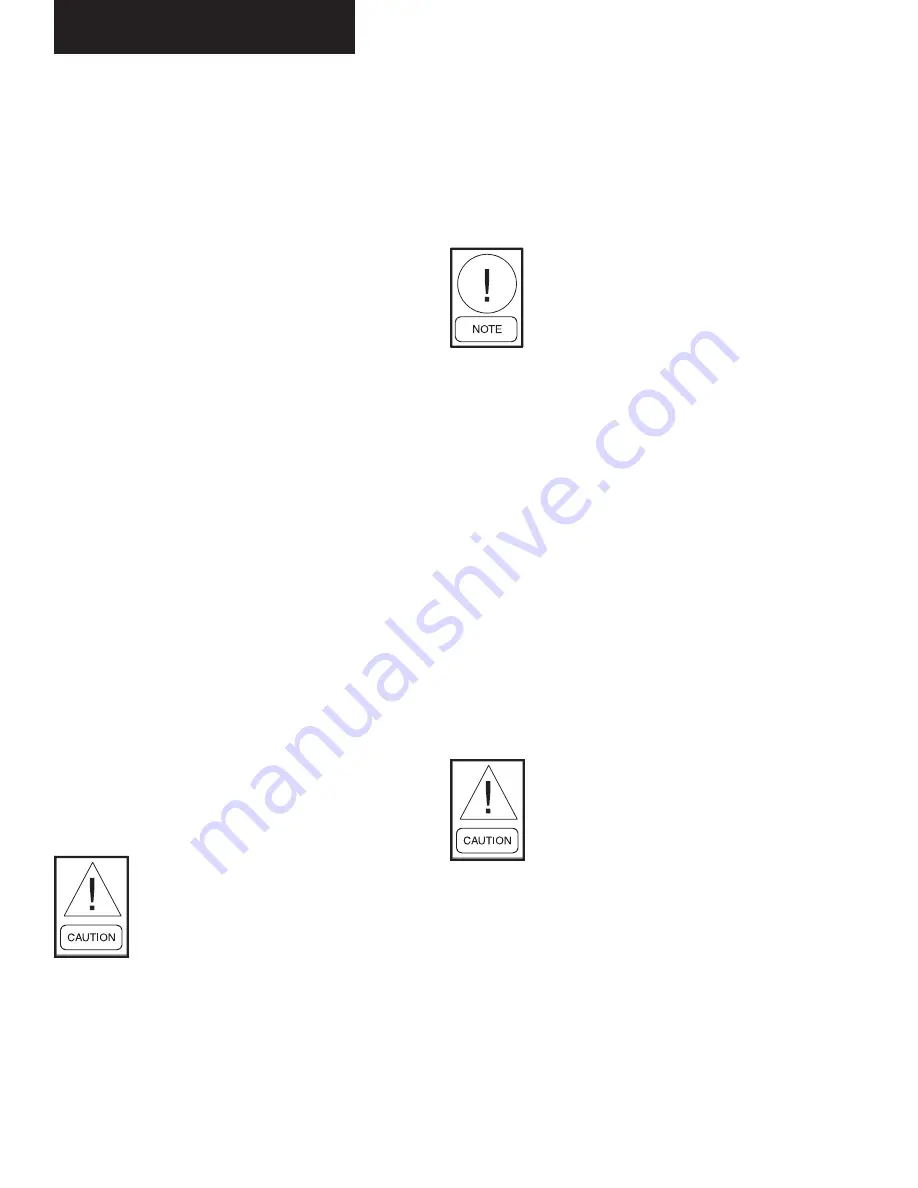
JOHNSON CONTROLS
128
FORM 150.62-NM6 (103)
MAINTENANCE
It is the responsibility of the equipment owner to provide
maintenance on the system.
IMPORTANT
If system failure occurs due to improper maintenance
during the warranty period, YORK will not be liable for
costs incurred to return the system to satisfactory op-
eration. The following is intended only as a guide and
covers only the chiller unit components. It does not cover
other related system components which may or may not
be furnished by YORK. System components should be
maintained according to the individual manufacture’s
recommendations as their operation will affect the op-
eration of the chiller.
COMPRESSORS
Oil Level check
The oil level can only be tested when the compressor
is running in stabilized conditions, to ensure that there
is no liquid refrigerant in the lower shell of the com-
pressor. When the compressor is running at stabilized
conditions, the oil level must be between 1/4 and 3/4 in
the oil sight glass. Note: at shutdown, the oil level can
fall to the bottom limit of the oil sight glass. Use YORK
“F” oil when adding oil.
Oil Analysis
The oil used in these compressors is pale yellow in color
(mineral oil). If the oil color darkens or exhibits a change
in color, this may be an indication of contaminants in the
refrigerant system. If this occurs, an oil sample should
be taken and analyzed. If contaminants are present,
the system must be cleaned to prevent compressor
failure.
Never use the scroll compressor to
pump the refrigerant system down into
a vacuum. Doing so will cause internal
arcing of the compressor motor which
will result in failure of compressor.
CONDENSER FAN MOTORS
Condenser fan motors are permanently lubricated and
require no maintenance.
CONDENSER COILS
Dirt should not be allowed to accumulate on the con-
denser coil surfaces. Cleaning should be as often as
necessary to keep coil clean.
Exercise care when cleaning the coil
so that the coil fins are not damaged.
OPERATING PARAMETERS
Regular checks of the system should be preformed to
ensure that operating temperatures and pressures are
within limitations, and that the operating controls are set
within proper limits. Refer to the Operation, Start-Up,
and Installation sections of this manual.
ON-bOARD bATTERY bACK-UP
U17 is the Real Time Clock chip that maintains the date/
time and stores customer programmed setpoints. Any-
time the chiller is to be off (no power to the microboard)
for an extended time (weeks/months), the clock should
be turned off to conserve power of the on-board battery.
To accomplish this, the J11 jumper on the microboard
must be moved to the “CLKOFF” position while power
is still supplied to the microboard.
The unit evaporator heater is 120VAC.
Disconnecting 120VAC power from
the unit, at or below freezing tem
peratures, can result in damage to
the evaporator and unit as a result of
the chilled liquid freezing.
OvERALL UNIT INSPECTION
In addition to the checks listed on this page, periodic
overall inspections of the unit should be accomplished
to ensure proper equipment operation. Items such as
loose hardware, component operation, refrigerant leaks,
unusual noises, etc. should be investigated and cor-
rected immediately.
Service and Troubleshooting
Содержание York YCAL0014E Series
Страница 111: ...JOHNSON CONTROLS 111 FORM 150 62 nm6 103 2 This page intentionally left blank...
Страница 133: ...JOHNSON CONTROLS 133 FORM 150 62 nm6 103 4 LD08851...
Страница 135: ...JOHNSON CONTROLS 135 FORM 150 62 nm6 103 4 This page intentionally left blank...
Страница 137: ...JOHNSON CONTROLS 137 FORM 150 62 nm6 103 LD08855 4...
Страница 139: ...JOHNSON CONTROLS 139 FORM 150 62 nm6 103 4 This page intentionally left blank...
Страница 141: ...JOHNSON CONTROLS 141 FORM 150 62 nm6 103 LD08858 4...
Страница 143: ...JOHNSON CONTROLS 143 FORM 150 62 nm6 103 4 This page intentionally left blank...
Страница 145: ...JOHNSON CONTROLS 145 FORM 150 62 nm6 103 LD08862 4...
Страница 147: ...JOHNSON CONTROLS 147 FORM 150 62 nm6 103 4 This page intentionally left blank...
Страница 149: ...JOHNSON CONTROLS 149 FORM 150 62 nm6 103 LD08865...
Страница 151: ...JOHNSON CONTROLS 151 FORM 150 62 nm6 103 LD08867...
Страница 153: ...JOHNSON CONTROLS 153 FORM 150 62 nm6 103 LD08869...
Страница 155: ...JOHNSON CONTROLS 155 FORM 150 62 nm6 103 4 This page intentionally left blank...
Страница 157: ...JOHNSON CONTROLS 157 FORM 150 62 nm6 103 LD08872...
Страница 159: ...JOHNSON CONTROLS 159 FORM 150 62 nm6 103 4 LD08877...
Страница 161: ...JOHNSON CONTROLS 161 FORM 150 62 nm6 103 LD08874...
Страница 163: ...JOHNSON CONTROLS 163 FORM 150 62 nm6 103 This page intentionally left blank...
Страница 165: ...JOHNSON CONTROLS 165 FORM 150 62 nm6 103 4 LD08830...
Страница 167: ...JOHNSON CONTROLS 167 FORM 150 62 nm6 103 4 LD08833...
Страница 169: ...JOHNSON CONTROLS 169 FORM 150 62 nm6 103 4 LD08835...
Страница 171: ...JOHNSON CONTROLS 171 FORM 150 62 nm6 103 4 This page intentionally left blank...
Страница 173: ...JOHNSON CONTROLS 173 FORM 150 62 nm6 103 4 LD08837...
Страница 175: ...JOHNSON CONTROLS 175 FORM 150 62 nm6 103 4 LD08840...
Страница 177: ...JOHNSON CONTROLS 177 FORM 150 62 nm6 103 4 LD08842...
Страница 179: ...JOHNSON CONTROLS 179 FORM 150 62 nm6 103 4 This page intentionally left blank...
Страница 181: ...JOHNSON CONTROLS 181 FORM 150 62 nm6 103 4 LD08844...
Страница 183: ...JOHNSON CONTROLS 183 FORM 150 62 nm6 103 4 LD08847...
Страница 185: ...JOHNSON CONTROLS 185 FORM 150 62 nm6 103 4 LD08849...
Страница 187: ...JOHNSON CONTROLS 187 FORM 150 62 nm6 103 4 This page intentionally left blank...