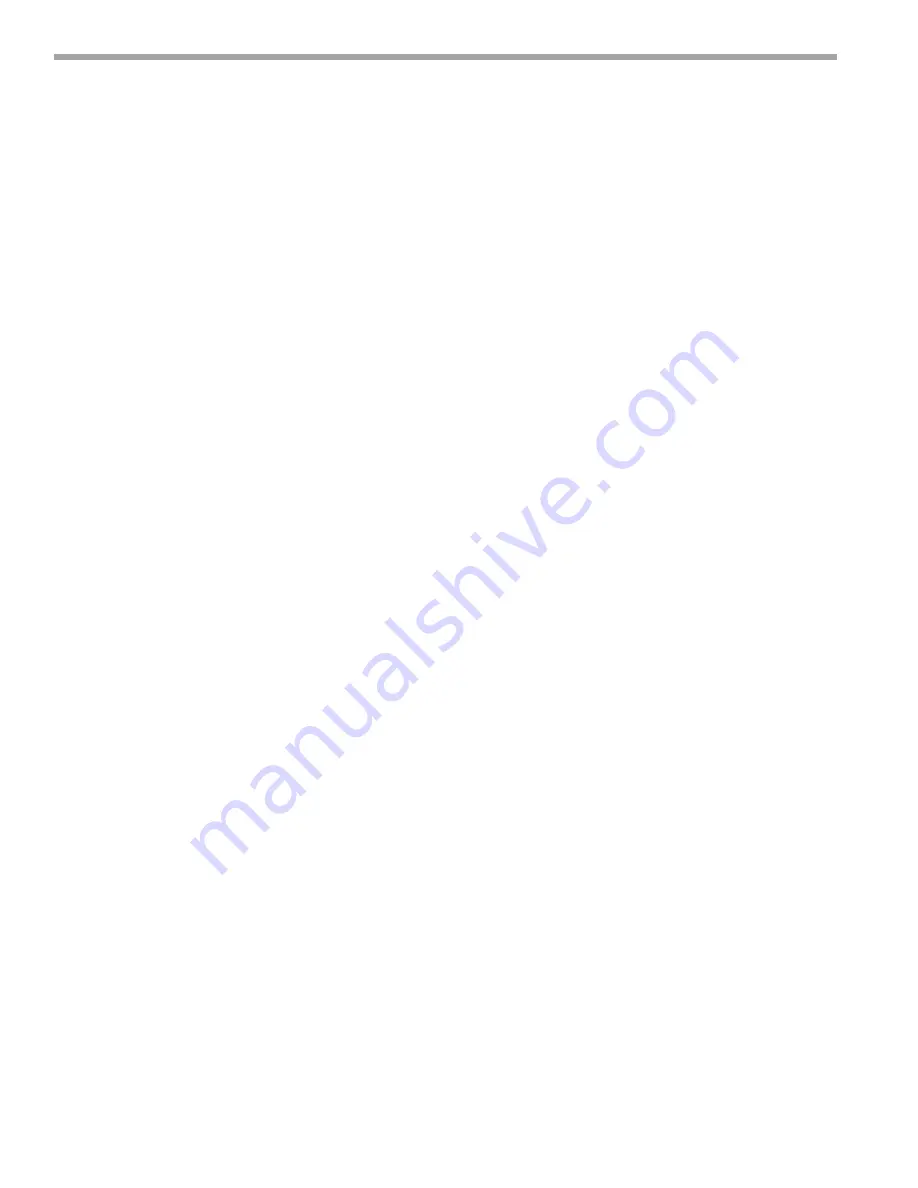
I n s t a l l a t i o n , O p e r a t i o n , M a i n t e n a n c e
56
W A T E R - S O U R C E H E A T P U M P S
JE-Series
I s s u e D a t e :
M a y 1 0 , 2 0 2 1
Troubleshooting, Cont’d.
Advanced Diagnostics
If a communicating service tool is connected to the DXM2,
additional diagnostic information and troubleshooting
capabilities are available. The current status of all DXM2
inputs can be verified, including the current temperature
readings of all temperature inputs. With a communicating
service tool the current status of the inputs can be
accessed from the Service Information menu. In the
manual operating mode, most DXM2 outputs can be
directly controlled for system troubleshooting. With a
communicating service tool the manual operating mode
can be accessed from the Installer menu. For more
detailed information on the advanced diagnostics of
the DXM2, see the DXM2 Installation, Operation and
Maintenance (IOM) manual (part #97B0003N15).
DXM2 Troubleshooting Process Flowchart/Functional
Troubleshooting Chart
The “DXM2 Functional Troubleshooting Process
Flowchart” is a quick overview of how to start diagnosing
a suspected problem, using the fault recognition features
of the DXM2 board. The “Functional Troubleshooting
Chart” on the following page is a more comprehensive
method for identifying a number of malfunctions that may
occur, and is not limited to just the DXM2 controls. Within
the chart are five columns:
• The “Fault” column describes the symptoms.
• Columns 2 and 3 identify in which mode the fault is
likely to occur, heating or cooling.
• The “Possible Cause column” identifies the most likely
sources of the problem.
• The “Solution” column describes what should be done
to correct the problem.