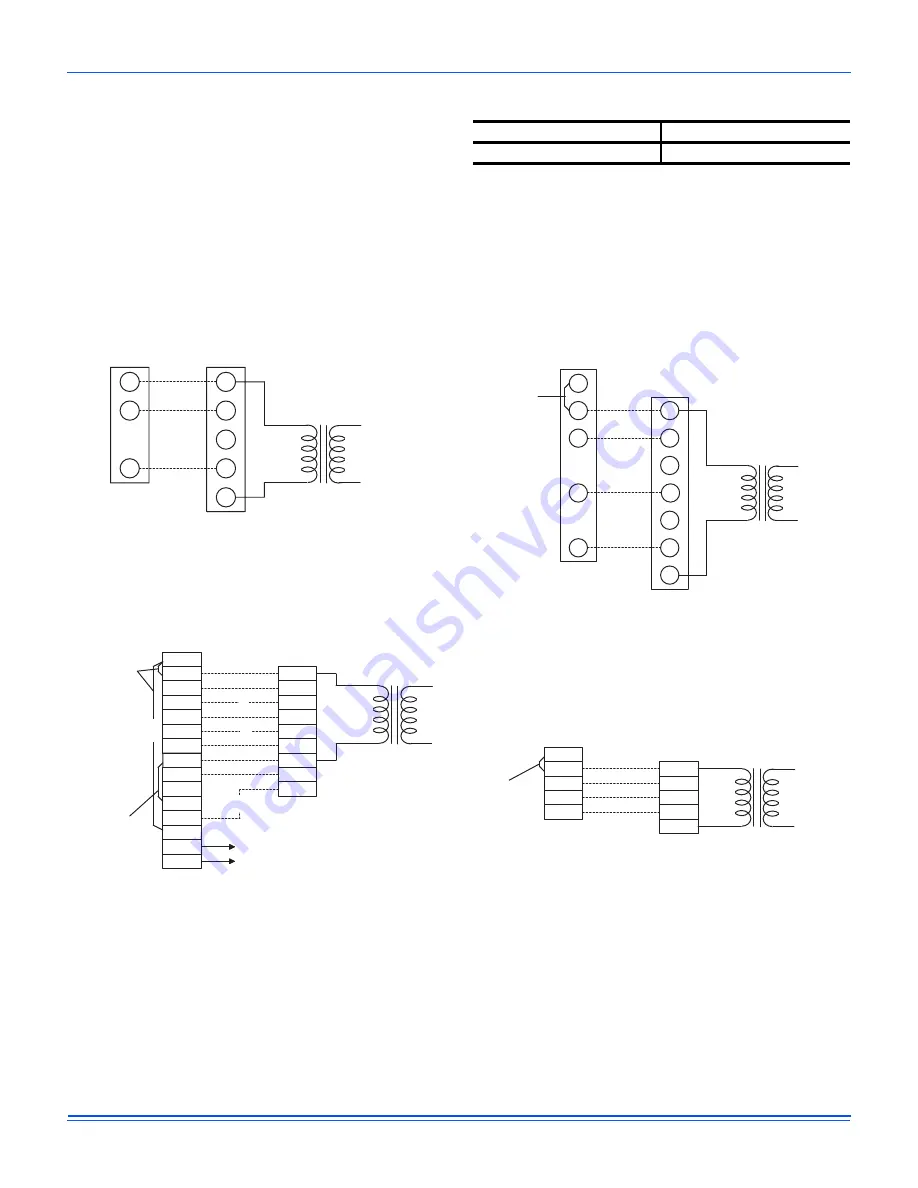
689670-BIM-A-0311
Johnson Controls Unitary Products
19
Thermostat Wiring
The thermostat should be located on an inside wall
approximately 56 inch above the floor where it will not be
subject to drafts, sun exposure or heat from electrical fixtures or
appliances. Follow the manufacturer's instructions enclosed
with thermostat for general installation procedure. Seven (7)
color-coded, insulated wires should be used to connect the
thermostat to the unit. Refer to Table 7 for control wire sizing
and maximum length.
Typical Control Wiring Detail
Figure 21: Typical Control Wiring
Table 7:
Control Wire Sizes
Wire Size
Maximum Length
1
18 AWG
150 Feet
1. From the unit to the thermostat and back to the unit.
RC
RH
Y1
Y2
W1
W2
G
LED 1
LED 2
COM
A1
A2
T
T
B
R
Y1
Y2
G
C
X
OCC
W2
W1
THERMOSTAT
1
TERMINALS
UNIT TERMINAL
STRIP TB1
24 VOLT
TRANSFORMER
TO REMOTE SENSOR
2TH040702224 IF USED
NOT
USED
ADD
JUMPER
ADD
JUMPER
4
4
3
2
1
ELECTRONIC PROGRAMMABLE THERMOSTAT 2ET04700224 (INCLUDES SUBBASE).
2
SECOND STAGE COOLING IS NOT REQUIRED ON UNITS LESS ECONOMIZER.
3
SECOND STAGE HEATING IS ONLY REQUIRED ON UNITS WITH A TWO STAGE
ELECTRIC HEATER OR 2 STAGE GAS HEAT.
4
REMOVE JUMPER J2 FROM TERMINALS 4 AND 9 ON JUMPER PLUG CONNECTOR
P6 ON UNITS WITH ECONOMIZER. TERMINALS A1 AND A2 PROVIDE A RELAY
OUT-PUT TO CLOSE THE OUTDOOR ECONOMIZER DAMPERS WHEN THE
THERMOSTAT SWITCHES TO THE SET-BACK POSITION.
COOLING / HEATING (ELECTRONIC THERMOSTAT)
MULTI STAGE
RH
RC
Y
W
G
R
Y1
W1
C
G
ADD
JUMPER
THERMOSTAT
1
TERMINALS
UNIT TERMINAL
STRIP TB1
24 VOLT
TRANSFORMER
1
ELECTRONIC PROGRAMMABLE THERMOSTAT 2ET07701024 (INCLUDES SUBBASE).
TO CONTROL THE ECONOMIZER ON SECOND STAGE COOLING, USE THERMOSTAT
2TH04700224.
COOLING / HEATING (ELECTRONIC THERMOSTAT)
SINGLE STAGE
RV
YC
GF
R
Y1
C
Y2
THERMOSTAT
1
TERMINALS
UNIT TERMINAL
STRIP TB1
24 VOLT
TRANSFORMER
1
24 VOLT THERMOSTAT 2TH07701024. TO CONTROL THE ECONOMIZER
ON SECOND STAGE COOLING, USE THE THERMOSTAT 2TH0401224.
G
COOLING ONLY (24 VOLT THERMOSTAT)
RC
Y
R
Y1
Y2
W1
W
W2
G
C
G
RH
THERMOSTAT
TERMINALS
UNIT TERMINAL
STRIP TB1
24 VOLT
TRANSFORMER
ADD
JUMPER
1
24 VOLT THERMOSTAT 2ET07701024. TO CONTROL THE ECONOMIZER ON THE SECOND
STAGE COOLING OR TO HAVE AN ELECTRIC HEAT ACCESSORY WITH TWO STAGES OF
HEAT, USE THERMOSTAT 2TH0471024.
1
COOLING / HEATING (24 VOLT THERMOSTAT)