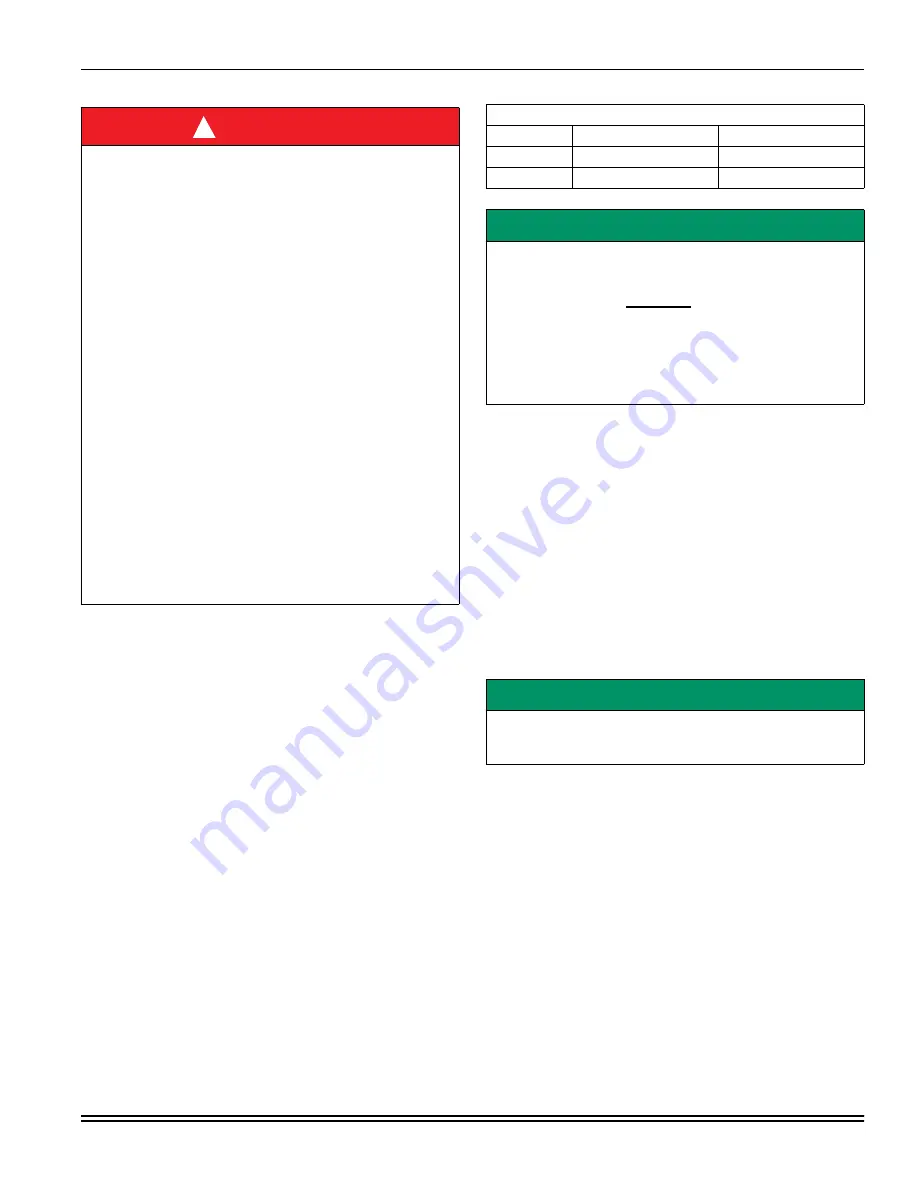
035-24121-001-C-1015
Johnson Controls Unitary Products
3
TESTS AND ADJUSTMENTS
Inlet and manifold gas pressure may be measured by connect-
ing the “U” tube manometer to the gas valve with a piece of tub-
ing. Follow the appropriate section in the instructions below.
Refer to Figure 2 for the locations of the pressure ports on the
gas valve.
Turn gas off at the ball valve or gas cock on gas supply line
before the gas valve. Find the pressure ports on the gas
valve marked Out P and In P.
1.
The manifold pressure must be taken at the port marked
OUT P.
2.
The gas inlet line pressure must be taken at the port
marked IN P.
3.
Using a 3/32” (2.4 mm) hexagonal wrench, loosen the set
screw by turning it 1 turn counter clockwise. DO NOT
REMOVE THE SET SCREW FROM THE PRESSURE
PORT.
Read the inlet gas pressure
Connect the positive side of the manometer to the IN P Tap on
the gas valve. Do not connect any tubing to the negative side of
the manometer, as it will reference atmospheric pressure. Refer
to Figure 2 for inlet pressure port location.
1.
Turn gas and electrical supplies on and follow the operating
instructions to place the unit back in operation.
2.
Once the correct gas inlet pressure has been established,
refer to Table 1, turn the gas supply to OFF, and turn the
electrical supply switch to OFF; then remove the flexible
tubing from the gas valve pressure tap, and tighten the set
screw using the 3/32” (2.4 mm) hexagonal wrench.
3.
Turn the electrical and gas supplies back on, and with the
burners in operation, check for gas leakage around the gas
valve pressure port for leakage using an approved non-cor-
rosive gas leak detection fluid, or other non-flammable leak
detection methods.
Read the manifold gas pressure
Connect the positive side of the manometer to the OUT P Tap
on the gas valve. Do not connect any tubing to the negative
side of the manometer as this is the port where it references
atmospheric pressure. Refer to Figure 3 for connection details.
1.
Refer to Figure 2 for location of pressure regulator adjust-
ment cap, and adjustment screw on main gas valve.
2.
Turn gas and electrical supplies on, and follow the operat-
ing instructions to place the unit back in operation.
3.
Adjust manifold pressure by adjusting gas valve regulator
screw for the appropriate gas per the following:
SINGLE STAGE GAS VALVE MODELS
1.
Refer to Figure 2 for location of pressure regulator adjust-
ment cap, and adjustment screw on main gas valve.
2.
Turn gas and electrical supplies on, and follow the operat-
ing instructions to place the unit back in operation.
3.
Adjust manifold pressure by adjusting gas valve regulator
screw for the appropriate gas per the following table.
DANGER
PROPANE AND HIGH ALTITUDE CONVERSION KITS
Make sure that the correct kit and/or gas orifices for the alti-
tude and the type of gas is used for the furnace installation.
Only use natural gas in furnaces designed for natural gas.
Only use propane (LP) gas for furnaces that have been prop-
erly converted to use propane (LP) gas. Do not use this fur-
nace with butane gas.
Incorrect gas orifices or a furnace that has been improperly
converted will create an extremely dangerous condition
resulting in premature heat exchanger failure, excessive
sooting, high levels of carbon monoxide, personal injury,
property damage, a fire hazard and/or death.
High altitude and propane (LP) conversions are required in
order for the appliance to satisfactorily meet the application.
An authorized distributor or dealer must make all gas conver-
sions.
In Canada, a certified conversion station or other qualified
agency, using factory specified and/or approved parts, must
perform the conversion.
The installer must take every precaution to insure that the fur-
nace has been converted to the proper gas orifice size when
the furnace is installed. Do not attempt to drill out any orifices
to obtain the proper orifice size. Drilling out a gas orifice will
cause misalignment of the burner flames, causing premature
heat exchanger burnout, high levels of carbon monoxide,
excessive sooting, a fire hazard, personal injury, property
damage and/or death.
!
TABLE 1:
Inlet Gas Pressure Range
INLET GAS PRESSURE RANGE
Natural Gas
Propane (LP)
Minimum
4.5” W.C. (1.12 kPa)
8.0” W.C. (1.99 kPa)
Maximum
10.5” W.C. (2.61 kPa)
13.0” (3.24 kPa) W.C.
IMPORTANT
The inlet gas pressure operating range table specifies what
the minimum and maximum gas line pressures must be for
the furnace to operate safely.
The gas line pressure MUST BE a minimum of
• 7” W.C. (1.74 kPA) for Natural Gas
• 11” W.C. (2.74 kPA) for Propane (LP) Gas
in order to obtain the BTU input specified on the rating plate
and/or the nominal manifold pressure specified in these
instructions and on the rating plate.
IMPORTANT
The cover screw for the pressure regulator must be removed
entirely to gain access to the adjustment screw. Loosening or
tightening the cover screw does not adjust the flow of gas.