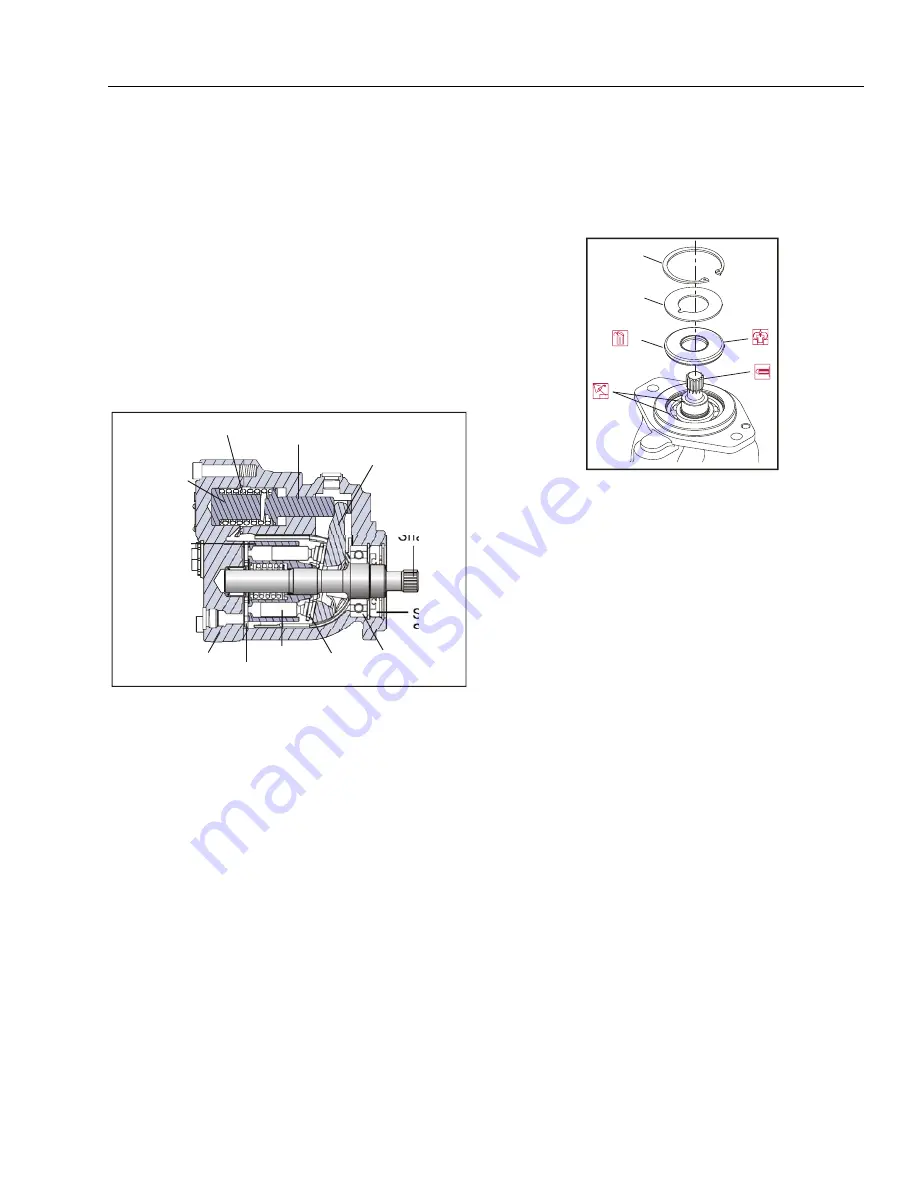
SECTION 3 - CHASSIS & TURNTABLE
3120746
– JLG Lift –
3-27
3.7 DRIVE MOTOR (S/N 85132 TO PRESENT)
Description
The drive motors are low to medium power, two-position
axial piston motors incorporating an integral servo piston.
They are designed for operation in both open and closed
circuit applications. The standard control is a direct acting
single line hydraulic control. The integral servo piston con-
trols motor displacement.
The motors are spring biased to maximum displacement
and hydraulically shifted to minimum displacement. Mini-
mum and maximum displacement can be set with fixed
internal stops. The large diameter servo piston allows
smooth acceleration and deceleration with relatively large
circuit orificing.
Shaft Seal Replacement
REMOVAL
1. Remove the snap ring (1) retaining the shaft seal
and support washer.
2. Remove the support washer (2).
3. Carefully pry out the shaft seal (3).
To avoid damaging the shaft during removal, install
a large sheet metal screw into the chuck of a slide
hammer. Drive the screw into the seal surface and
use the slide hammer to pull the seal.
4. Discard the seal.
INSPECT THE COMPONENTS
Inspect the new seal, the motor housing seal bore, and
the sealing area on the shaft for rust, wear, and contami-
nation. Polish the shaft and clean the housing if neces-
sary.
INSTALLATION
1. Cover the shaft splines with an installation sleeve to
protect the shaft seal during installation.
2. Install a new shaft seal with the cupped side facing
the motor. Press seal into housing until it bottoms
out. Press evenly to avoid binding and damaging
the seal.
3. Install seal support washer.
4. Install snap ring.
5. Remove the installation sleeve.
Bias spring
Servo piston
Swashplate
Output
Shaft
Piston
Slipper
Cylinder
Block
Endcap
Shaft
Seal
Bearing
Minimum
Angle
Stop
Valve plate
Figure 3-7. Drive Motor Cross Section
1
2
3
1. Snap Ring
2. Support Washer
3. Shaft Seal
Figure 3-8. Removing the Shaft Seal
Содержание 601S
Страница 1: ...Service and Maintenance Manual Model 601S P N 3120746 November 22 2016 ...
Страница 2: ......
Страница 4: ... JLG Lift THIS PAGE LEFT BLANK INTENTIONALLY ...
Страница 16: ...x JLG Lift 3120746 TABLE OF CONTENTS Continued This page left blank intentionally ...
Страница 26: ...SECTION 1 SPECIFICATIONS 1 10 JLG Lift 3120746 Figure 1 3 Torque Chart ...
Страница 36: ...SECTION 2 GENERAL 2 10 JLG Lift 3120746 Figure 2 7 Connector Installation ...
Страница 40: ...SECTION 2 GENERAL 2 14 JLG Lift 3120746 This page left blank intentionally ...
Страница 49: ...SECTION 3 CHASSIS TURNTABLE 3120746 JLG Lift 3 9 Figure 3 1 Torque Hub Drive Fairfield ...
Страница 51: ...SECTION 3 CHASSIS TURNTABLE 3120746 JLG Lift 3 11 Figure 3 2 Torque Hub Drive Auburn Gear ...
Страница 53: ...SECTION 3 CHASSIS TURNTABLE 3120746 JLG Lift 3 13 Figure 3 3 Drive Brake Assembly Ausco ...
Страница 88: ...SECTION 3 CHASSIS TURNTABLE 3 48 JLG Lift 3120746 Figure 3 38 Swing Bearing Tolerance Boom Placement ...
Страница 91: ...SECTION 3 CHASSIS TURNTABLE 3120746 JLG Lift 3 51 Figure 3 40 Swing Brake Assembly Ausco ...
Страница 99: ...SECTION 3 CHASSIS TURNTABLE 3120746 JLG Lift 3 59 ...
Страница 119: ...SECTION 3 CHASSIS TURNTABLE 3120746 JLG Lift 3 79 Figure 3 46 EFI Component Location ...
Страница 122: ...SECTION 3 CHASSIS TURNTABLE 3 82 JLG Lift 3120746 Figure 3 47 ECM EPM Identification ECM EPM ...
Страница 128: ...SECTION 3 CHASSIS TURNTABLE 3 88 JLG Lift 3120746 This page left blank intentionally ...
Страница 132: ...SECTION 4 BOOM PLATFORM 4 4 JLG Lift 3120746 Figure 4 5 Boom Assembly Cutaway Sheet 1 of 2 ...
Страница 133: ...SECTION 4 BOOM PLATFORM 3120746 JLG Lift 4 5 Figure 4 6 Boom Assembly Cutaway Sheet 2 of 2 ...
Страница 145: ...SECTION 4 BOOM PLATFORM 3120746 JLG Lift 4 17 Figure 4 22 Rotator Assembly Helac ...
Страница 148: ...SECTION 4 BOOM PLATFORM 4 20 JLG Lift 3120746 This page left blank intentionally ...
Страница 160: ...SECTION 5 HYDRAULICS 5 12 JLG Lift 3120746 Figure 5 16 Troubleshooting System Response is Sluggish ...
Страница 174: ...SECTION 5 HYDRAULICS 5 26 JLG Lift 3120746 This page left blank intentionally ...
Страница 176: ...SECTION 6 JLG CONTROL SYSTEM ADE 6 2 JLG Lift 3120746 Figure 6 1 EPBCS Block Diagram ...
Страница 180: ...SECTION 6 JLG CONTROL SYSTEM ADE 6 6 JLG Lift 3120746 Figure 6 3 Control Module and Fault Code Indicator Location ...
Страница 183: ...SECTION 6 JLG CONTROL SYSTEM ADE 3120746 JLG Lift 6 9 Figure 6 4 Analyzer Flow Chart Sheet 1 of 3 ...
Страница 184: ...SECTION 6 JLG CONTROL SYSTEM ADE 6 10 JLG Lift 3120746 Figure 6 5 Analyzer Flow Chart Sheet 2 of 3 ...
Страница 185: ...SECTION 6 JLG CONTROL SYSTEM ADE 3120746 JLG Lift 6 11 Figure 6 6 Analyzer Flow Chart Sheet 3 of 3 ...
Страница 224: ...SECTION 7 SCHEMATICS 7 2 JLG Lift 3120746 Figure 7 1 Electrical Components Installation Prior to S N 62137 Sheet 1 of 2 ...
Страница 225: ...SECTION 7 SCHEMATICS 3120746 JLG Lift 7 3 Figure 7 2 Electrical Components Installation Prior to S N 62137 Sheet 2 of 2 ...
Страница 228: ...SECTION 7 SCHEMATICS 7 6 JLG Lift 3120746 Figure 7 5 Electrical Schematic Deutz Engine Sheet 1 of 2 ...
Страница 229: ...SECTION 7 SCHEMATICS 3120746 JLG Lift 7 7 Figure 7 6 Electrical Schematic Deutz Engine Sheet 2 of 2 1870074 C ...
Страница 230: ...SECTION 7 SCHEMATICS 7 8 JLG Lift 3120746 Figure 7 7 Electrical Schematic Ford Dual Fuel Engine Sheet 1 of 2 ...
Страница 231: ...SECTION 7 SCHEMATICS 3120746 JLG Lift 7 9 Figure 7 8 Electrical Schematic Ford Dual Fuel Engine Sheet 2 of 2 1870077 A ...
Страница 232: ...SECTION 7 SCHEMATICS 7 10 JLG Lift 3120746 Figure 7 9 Electrical Schematic Ford EFI Engine Sheet 1 of 2 ...
Страница 233: ...SECTION 7 SCHEMATICS 3120746 JLG Lift 7 11 Figure 7 10 Electrical Schematic Ford EFI Engine Sheet 2 of 2 1870127 A ...
Страница 234: ...SECTION 7 SCHEMATICS 7 12 JLG Lift 3120746 Figure 7 11 Electrical Schematic ADE Machines Sheet 1 of 4 ...
Страница 235: ...SECTION 7 SCHEMATICS 3120746 JLG Lift 7 13 Figure 7 12 Electrical Schematic ADE Machines Sheet 2 of 4 1870132 G ...
Страница 236: ...SECTION 7 SCHEMATICS 7 14 JLG Lift 3120746 Figure 7 13 Electrical Schematic ADE Machines Sheet 3 of 4 ...
Страница 237: ...SECTION 7 SCHEMATICS 3120746 JLG Lift 7 15 Figure 7 14 Electrical Schematic ADE Machines Sheet 4 of 4 1870132 G ...
Страница 238: ...SECTION 7 SCHEMATICS 7 16 JLG Lift 3120746 Figure 7 15 Hydraulic Schematic Sheet 1 of 4 ...
Страница 239: ...SECTION 7 SCHEMATICS 3120746 JLG Lift 7 17 Figure 7 16 Hydraulic Schematic Sheet 2 of 4 2792338 A ...
Страница 240: ...SECTION 7 SCHEMATICS 7 18 JLG Lift 3120746 Figure 7 17 Hydraulic Schematic Sheet 3 of 4 ...
Страница 241: ...SECTION 7 SCHEMATICS 3120746 JLG Lift 7 19 Figure 7 18 Hydraulic Schematic Sheet 4 of 4 2792338 A ...
Страница 242: ...SECTION 7 SCHEMATICS 7 20 JLG Lift 3120746 This page left blank intentionally ...
Страница 243: ......