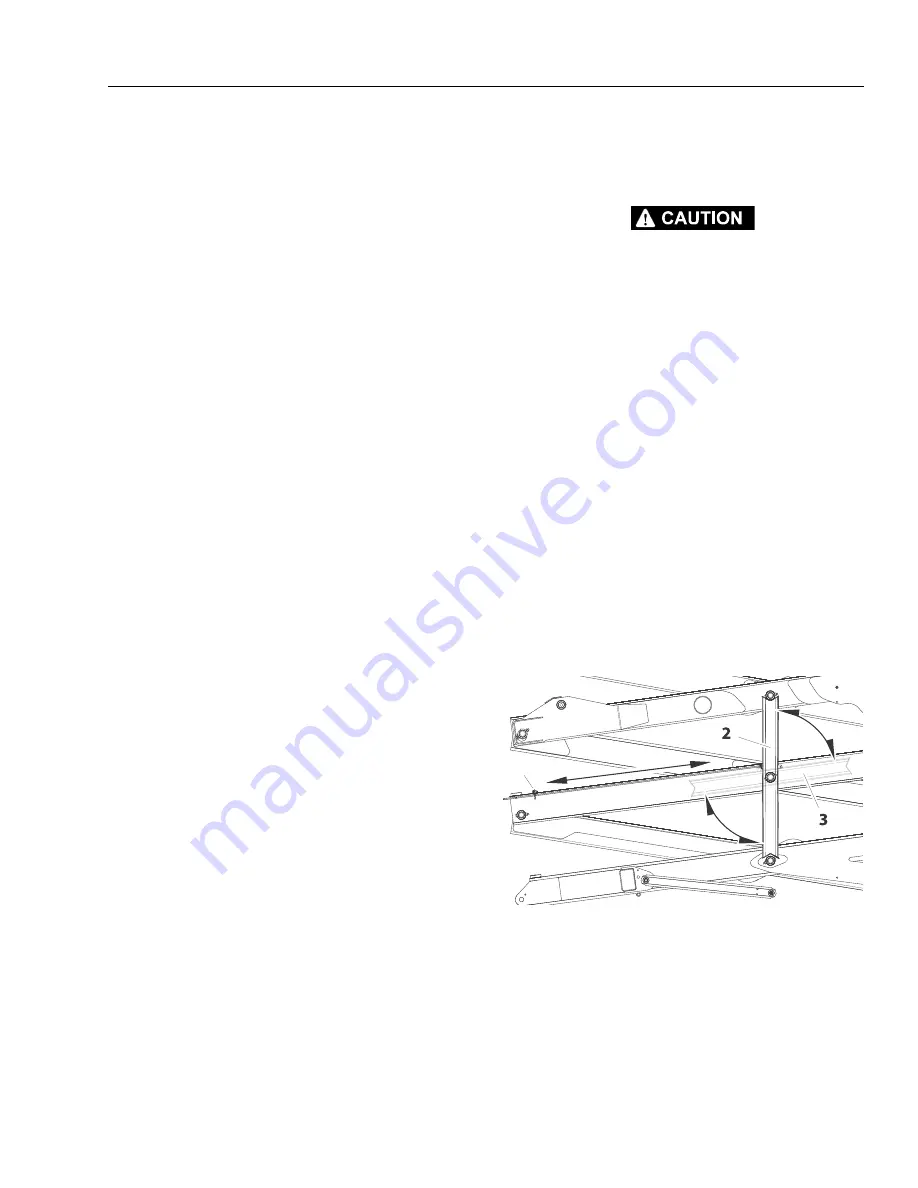
SECTION 2 - GENERAL
31215079
2-7
3. The only exception to the above is to drain and fill
the system with Premium Hydraulic Fluid oil or its
equivalent. This will allow start up at temperatures
down to -20°F (-29°C). However, use of this oil will
give poor performance at temperatures above 120°F
(49°C). Systems using Premium Hydraulic Fluid
should not be operated at temperatures above 200°F
(94°C) under any condition.
Changing Hydraulic Oil
1. Use of any of the recommended hydraulic oils elimi-
nates the need for changing the oil on a regular
basis. However, filter elements must be changed
after the first 50 hours of operation and every 300
hours thereafter. If it is necessary to change the oil,
use only those oils meeting or exceeding the specifi-
cations appearing in this manual. If unable to obtain
the same type of oil supplied with the machine, con-
sult local supplier for assistance in selecting the
proper equivalent. Avoid mixing petroleum and syn-
thetic base oils. JLG Industries recommends chang-
ing the hydraulic oil annually.
2. Use every precaution to keep the hydraulic oil clean.
If the oil must be poured from the original container
into another, be sure to clean all possible contami-
nants from the service container. Always clean the
mesh element of the filter and replace the cartridge
any time the system oil is changed.
3. While the unit is shut down, a good preventive main-
tenance measure is to make a thorough inspection of
all hydraulic components, lines, fittings, etc., as well
as a functional check of each system, before placing
the machine back in service.
Lubrication Specifications
Specified lubricants, as recommended by the compo-
nent manufacturers, are always the best choice, how-
ever, multi-purpose greases usually have the qualities
which meet a variety of single purpose grease require-
ments. Should any question arise, regarding the use of
greases in maintenance stock, consult your local sup-
plier for evaluation. Refer to Section 1 for an explanation
of the lubricant key designations appearing in the Lubri-
cation Chart.
2.5
SERVICE MAINTENANCE COMPONENTS
Setting Scissor Arm Safety Prop
THE SAFETY PROP MUST BE USED WHENEVER MAINTENANCE PER-
FORMED ON THE MACHINE REQUIRES THE SCISSOR ARMS TO BE
RAISED.
1 To engage the safety props, raise the unloaded plat-
form high enough to allow the safety props to rotate
vertically into position. (See Figure 2-1.)
2. Rotate the rod keeper plate and release the safety
prop actuator rod at the front of the machine.
(See Figure 2-2.)
3. Lift the actuator rod (flat) up out of the slot in the
keeper plate bracket and pull the actuator rod to
align the safety props vertically with the scissor arm
center pins above and below the safety prop mount-
ing pins.
4. Set the actuator rod (flat at the set position) into the
slot on the keeper plate bracket and rotate the
keeper plate to lock the actuator rod in this position.
5. Lower the platform arms until the safety prop rests
on the scissor arm center pin mounts above and
below the safety prop.
Maintenance can now begin.
To store the safety prop, raise the platform, release the
actuator rod from the keeper plate bracket, push the
safety prop rod so that the safety props are restored
back to its stowed position. Lock the actuator rod in
place with the keeper plate till next use.
1
Figure 2-1. Scissor Arm - Safety Prop Assembly
1.
Actuator Rod/Rod Keeper Plate.
2.
Safety Prop in set position.
3.
Safety Prop in stowed position.
Go
to
Discount-Equipment.com
to
order
your
parts