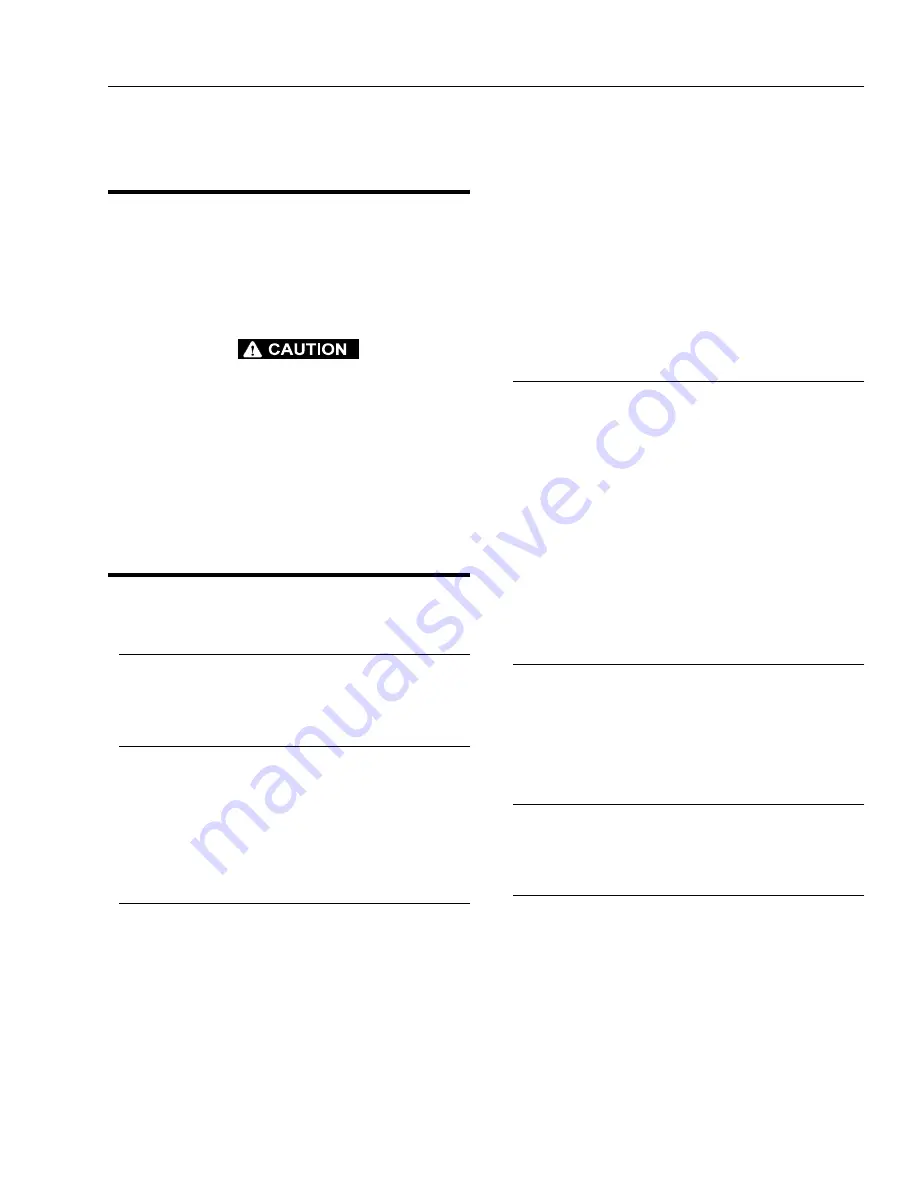
SECTION 2 - PROCEDURES
3120791
– JLG Sizzor –
2-1
SECTION 2. PROCEDURES
2.1
GENERAL
This section provides information necessary to perform
maintenance on the scissor lift. Descriptions, techniques
and specific procedures are designed to provide the saf-
est and most efficient maintenance for use by personnel
responsible for ensuring the correct installation and oper-
ation of machine components and systems.
WHEN AN ABNORMAL CONDITION IS NOTED AND PROCEDURES
CONTAINED HEREIN DO NOT SPECIFICALLY RELATE TO THE
NOTED IRREGULARITY, WORK SHOULD BE STOPPED AND
TECHNICALLY QUALIFIED GUIDANCE OBTAINED BEFORE WORK
IS RESUMED.
The maintenance procedures included consist of servic-
ing and component removal and installation, disassembly
and assembly, inspection, lubrication and cleaning. Infor-
mation on any special tools or test equipment is also pro-
vided where applicable.
2.2
SERVICING AND MAINTENANCE
GUIDELINES
General
The following information is provided to assist you in the
use and application of servicing and maintenance proce-
dures contained in this chapter.
Safety and Workmanship
Your safety, and that of others, is the first consideration
when engaging in the maintenance of equipment. Always
be conscious of weight. Never attempt to move heavy
parts without the aid of a mechanical device. Do not allow
heavy objects to rest in an unstable position. When raising
a portion of the equipment, ensure that adequate support
is provided.
Cleanliness
1.
The most important single item in preserving the
long service life of a machine is to keep dirt and for-
eign materials out of the vital components. Precau-
tions have been taken to safeguard against this.
Shields, covers, seals, and filters are provided to
keep air, fuel, and oil supplies clean; however, these
items must be maintained on a scheduled basis in
order to function properly.
2.
At any time when air, fuel, or oil lines are discon-
nected, clear adjacent areas as well as the openings
and fittings themselves. As soon as a line or compo-
nent is disconnected, cap or cover all openings to
prevent entry of foreign matter.
3.
Clean and inspect all parts during servicing or main-
tenance, and assure that all passages and openings
are unobstructed. Cover all parts to keep them
clean. Be sure all parts are clean before they are
installed. New parts should remain in their contain-
ers until they are ready to be used.
Components Removal and Installation
4.
Use adjustable lifting devices, whenever possible, if
mechanical assistance is required. All slings (chains,
cables, etc.) should be parallel to each other and as
near perpendicular as possible to top of part being
lifted.
5.
Should it be necessary to remove a component on
an angle, keep in mind that the capacity of an eye-
bolt or similar bracket lessens, as the angle between
the supporting structure and the component
becomes less than 90°.
6.
If a part resists removal, check to see whether all
nuts, bolts, cables, brackets, wiring, etc., have been
removed and that no adjacent parts are interfering.
Component Disassembly and Reassembly
When disassembling or reassembling a component, com-
plete the procedural steps in sequence. Do not partially
disassemble or assemble one part, then start on another.
Always recheck your work to assure that nothing has been
overlooked. Do not make any adjustments, other than
those recommended, without obtaining proper approval.
Pressure-Fit Parts
When assembling pressure-fit parts, use an “anti-seize” or
molybdenum disulfide base compound to lubricate the
mating surface.
Bearings
1.
When a bearing is removed, cover it to keep out dirt
and abrasives. Clean bearings in nonflammable
cleaning solvent and allow to drip dry. Compressed
air can be used but do not spin the bearing.
2.
Discard bearings if the races and balls (or rollers)
are pitted, scored, or burned.
3.
If a bearing is found to be serviceable, apply a light
coat of oil and wrap it in clean (waxed) paper. Do not
unwrap reusable or new bearings until they are
ready to install.
Содержание 26MRT
Страница 2: ......
Страница 11: ...SECTION 1 SPECIFICATIONS 3120791 JLG Sizzor 1 5 Figure 1 2 Serial Number Locations ...
Страница 12: ...SECTION 1 SPECIFICATIONS 1 6 JLG Sizzor 3120791 Figure 1 3 Torque Chart ...
Страница 28: ...SECTION 2 PROCEDURES 2 16 JLG Sizzor 3120791 Figure 2 16 Drive Axle Assembly ...
Страница 37: ...SECTION 2 PROCEDURES 3120791 JLG Sizzor 2 25 Figure 2 20 Brake Assembly ...
Страница 39: ...SECTION 2 PROCEDURES 3120791 JLG Sizzor 2 27 Figure 2 21 ADDCO Adjustments Gasoline Dual Fuel Engine ...
Страница 40: ...SECTION 2 PROCEDURES 2 28 JLG Sizzor 3120791 Figure 2 22 ADDCO Adjustments Diesel Engine ...
Страница 54: ...SECTION 3 TROUBLESHOOTING 3 10 JLG Sizzor 3120791 Figure 3 1 Electrical Schematic Yanmar Sheet of 1 of 2 ...
Страница 56: ...SECTION 3 TROUBLESHOOTING 3 12 JLG Sizzor 3120791 Figure 3 3 Electrical Schematic Daihatsu Sheet 1 of 2 ...
Страница 58: ...SECTION 3 TROUBLESHOOTING 3 14 JLG Sizzor 3120791 Figure 3 5 Hydraulic Schematic Sheet 1 of 2 ...
Страница 59: ...SECTION 3 TROUBLESHOOTING 3120791 JLG Sizzor 3 15 Figure 3 6 Hydraulic Schematic Sheet 2 of 2 1282590 L ...
Страница 60: ...SECTION 3 TROUBLESHOOTING 3 16 JLG Sizzor 3120791 This page intentionally left blank ...
Страница 61: ......