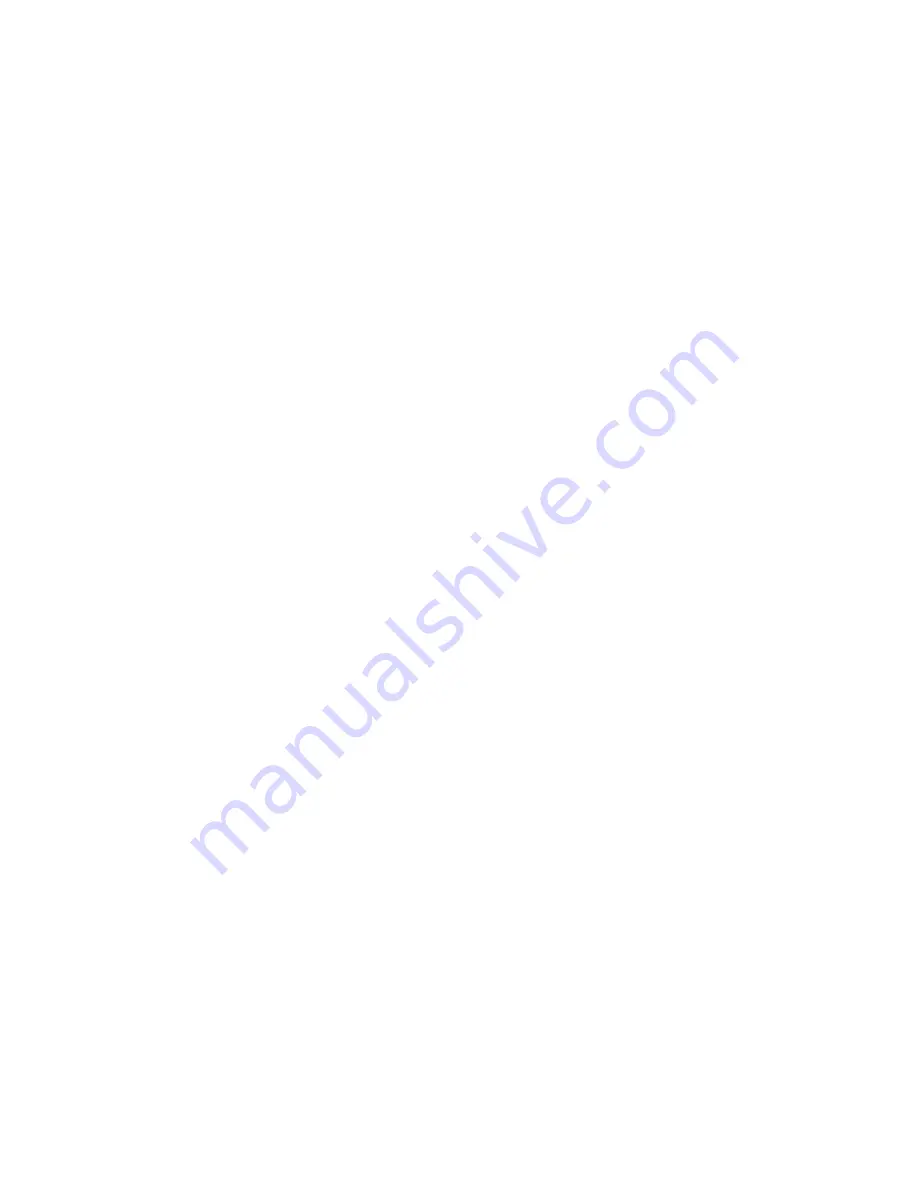
Foundations
The machine should be sited on a firm level floor capable of withstanding its
loaded weight.
Electrical supply
Single phase - Each dryer must be provided with a separate isolation point,
usually a fused switched spur outlet. Electrical connections are made inside the
rear service box located at the upper left of the machine. Notice must be taken
of the connection diagram. Ensure that the machine is also earthed correctly
using the copper lug provided. Three phase - A separate circuit serving each
dryer must be provided. On electric heat models the connection is made on the
oven contactor at the rear. The isolator must be in an accessible position for
emergency shut off. A competent installer must carry out all work. All work and
materials must comply with local and national codes of practice.The machine
must be installed using correctly sized cable (not provided) and an appropriate
protection device, i.e. fuse or circuit breaker. A permanent 24hr power supply
is essential.
Gas supply
Ensure that the correct pressure is supplied to the unit depending upon the
type of gas used, if the inline pressure exceeds the max permissible pressure a
regulator must be fitted. The machine is designed to burn at a certain rate,
known as the Btu or kw rating of the appliance. To ensure that this rate is
maintained the gas supply should remain constant. therefore the supply line
must be correctly sized. Distance from the meter and other appliances on the
same supply will have an effect on the pressure. Each unit should have a gas
isolation tap, test nipple point and restraining wire/chain. The machine should
be connected to a supply using a flexible armoured hose with union connector,
(bayonet fittings must not be used) as vibrations could cause a solid connection
to fracture. All gas work must be carried out by a registered CORGI gas installer
and must comply with all relevant local and national codes of practice.
Exhaust
All exhaust ductwork must be designed by a competent operative to ensure
that the installation does not have any detrimental effect on the performance of
the dryer. The duct should follow the shortest possible route to atmosphere
using the least number of bends possible and should be constructed of a
smooth wall, rigid stainless steel or galvanized tubing. The diameter of the
ducting should never be reduced in size and where possible 45º bends should
be used in place of 90º bends. Rigid ducting should be used right upto the
machine spigot wherever possible. If this is not possible flexible ducting can be
used as a final connection only and should be limited to a maximum 0.5 metres
in length and must not change direction. Plastic or foil flexible ducting must not
be used, only use metal flexible such as rega-duct, steelflex or glassflex duct. If
a common duct is to be used to vent multiple dryer installations the diameter
must be increased to accommodate the cumulative effect of all the dryers.
Exhaust terminations for horizontal duct terminations should be via a downturn
90º elbow, vertical ducts to be terminated via inverted china hats or a 135º
return. Conventional china hats (hoods) must not be used as this as a massive
effect on back pressure. Suitable louvres or grills may be used to prevent entry
by foreign objects but consideration must be given to potential restrictions to
air flow and must also allow easy cleaning of the grill or louvre.
Duct termination must be 2 metres away from any opening or fresh air inlet
into the building. Where this is not possible a minimum of 300mm will be
accepted, provided that the configuration of the exhaust termination in respect
of the make-up air inlet grille shall not allow re-circulation of the exhausted
damp, warm air back into the make-up air vent.
The exhaust should be properly sealed at all the joints by duct tape(not rivets or
screws). Larger diameter or rectangular ducting may require some additional
fixing by screws or rivets but these must be kept to a minimum in number and
length. In all cases adequate access must be made for cleaning purposes. Site
conditions may vary and these should be taken into account when planning the
exhaust system. It is recommended that the supplier is consulted for long,
multiple and difficult ducting runs.
NOTE! NEVER USE 90º ENTRY POINTS
ON MULTIPLE DUCTING. ONLY USE 45º ENTRY SPIGOTS (NOT BOOTS).
Ventilation
While in operation the dryer removes a large amount of air, from the room
via the exhaust. Therefore the air inside the room must be continually
replenished with fresh air from atmosphere. Ventilation must be fixed and
unrestricted and sized to provide the correct amount of fresh air in take.
Louvres and grills may be used but consideration should be given to any
restriction imposed by them. Ventilation must be a minimum of 300mm and
should ideally be 2 meters away from any exhaust duct termination. If more
than one dryer is installed the opening should be increased to match their
requirements; there is no need to make a separate opening. Where
ventilation from outside is provided through a cavity, the cavity must be lined
and sealed in a plenium box or suitable alternative. Site conditions may vary
and these should be taken into account when planning the ventilation
Steam
All steam pipework in the installation must be sized by a competent operative
taking into account the distance from the source and the amount of steam
that is required. The steam supplied must be dry. Final connection to the
steam coil shall be made with a flexible hose. Suitable isolation taps and a
strainer must be fitted to facilitate ease of service. A condensate return line
must be fitted incorporating a trap mounted 300mm below the steam coil
outlet, non return valve and isolation tap. All steam supply pipes should be
lagged and installed to local and national codes of practice as they form part
of a pressurised system.
NOTE! FOR STEAM DRYERS A CLEAN, DRY,
REGULATED COMPRESSED AIR SUPPLY AT 80PSI IS REQUIRED.
Water Supply
This machine is fitted with a S.A.F.E. system (Sensor Activated Fire
Extinguishing system), which is designed to prevent serious laundry fires
within the dryer. A permanent 24hr water supply is essential and should be
supplied via an isolation valve or tap terminating in a
3
/
4
” BSP male threaded
end. Final connection via
3
/
4
” flexible hose supplied with the dryer.
NOTES
1 WHERE THE WATER FOR THE SAFE SYSTEM IS TO BE BROUGHT
FROM A COLD WATER SERVICE, WHICH ALSO SUPPLIES THE
WASHER(S), IT IS RECOMMENDED THAT THE SAFE SUPPLY IS
TAKEN FROM UPSTREAM OR BEFORE THE WASHER(S) SUPPLY
TO ENSURE MAXIMUM AVAILABLE PRESSURE IS SUPPLIED TO
THE DRYER(S) .
2 WHERE EXISTING SERVICES ARE TO BE CONNECTED TO.
THE INSTALLER MUST ENSURE,THAT THESE ARE ADEQUATELY
SIZED AND THAT THEY ARE IN GOOD WORKING ORDER.
FOR EXAMPLE, IF A DRYER IS TO BE CONNECTED TO AN
EXISTING EXHAUST IT MUST BE CHECKED FOR ANY
BLOCKAGES DURING INSTALLATION AND BE
CLEAR OF ANY LINT.
3 FOR MULTIPLE MACHINE INSTALLATIONS SERVICES MUST BE
INCREASED IN SIZE ACCORDINGLY. I.E EXHAUST DUCTING,
GAS SUPPLY ETC.
All specifications subject to change with out notice