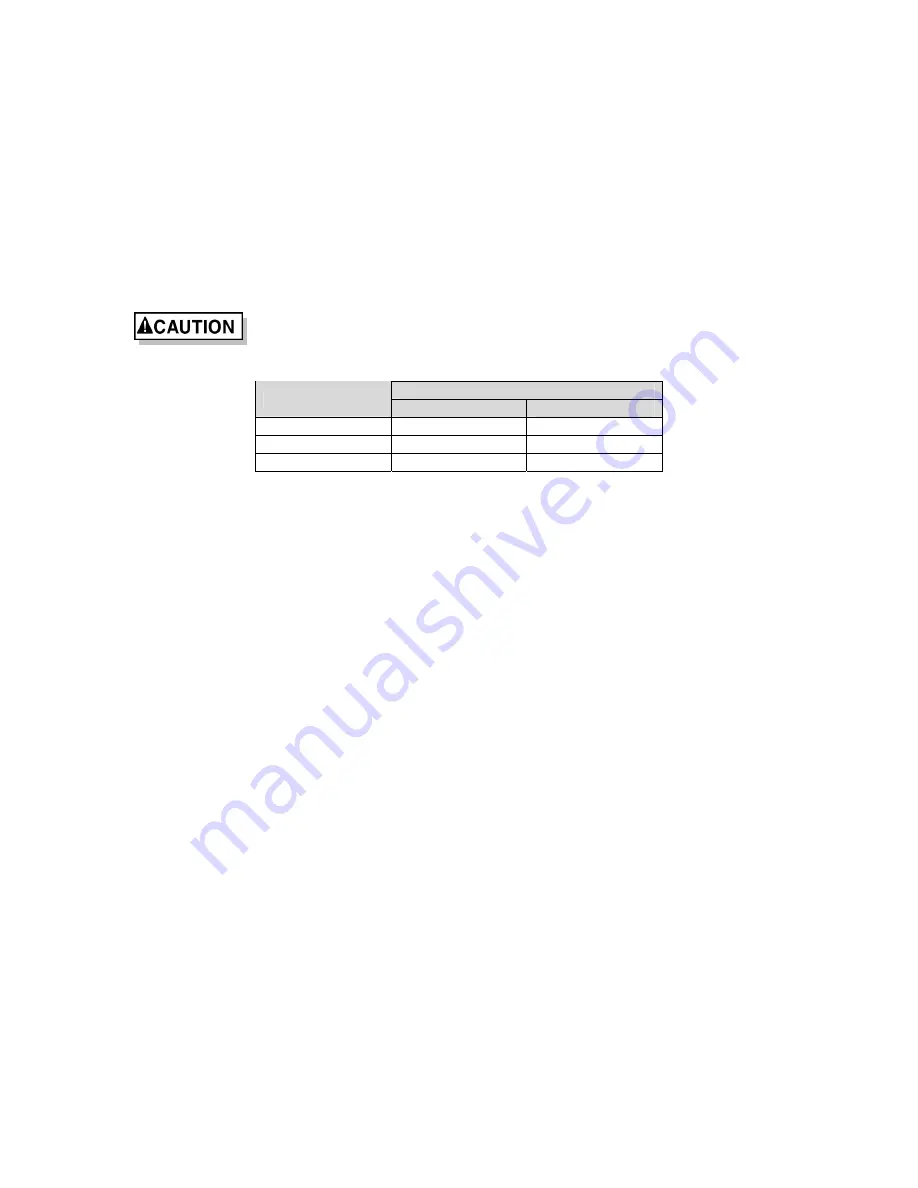
11
2. Place a warning placard or tag on the service panel to prevent accidental
electrical shock.
3. When installing the motor power cord into a receptacle, make sure the plug is
compatible with the receptacle.
4. When using hard-wired connections, connect the wires as shown in the wiring
diagram.
5. Install the fuses or reset the breakers.
6. Check the operation of the saw.
For circuits that are a long distance from the electrical service box, the wire size
must be increased in order to deliver ample voltage to the motor. To minimize
power losses and to prevent motor overheating and burnout, the use of wire
sizes for branch circuits or electrical extension cords according to the
following table is recommended.
AWG (American Wire Gauge) Number
Conductor Length
120 Volt Lines
240 Volt Lines
0 – 50 Feet
No. 14
No. 14
50 – 100 Feet
No. 12
No. 14
Over 100 Feet
No. 8
No. 12
Cleaning
•
All unpainted surfaces of the machine are treated with a rust preventative. Clean all
rust protected surfaces with a mild solvent. Do not use paint thinner, lacquer thinner,
gasoline or mineral spirits; these will damage painted surfaces.
Operation
General
•
Always wear approved safety glasses when using this machine. Before operating the
machine, remove tie, rings, watches and other jewelry, and roll sleeves up past the
elbows. Remove all loose clothing and confine long hair. Non-slip footwear is
recommended. Do
not
wear gloves when operating the saw.
•
Never use the machine if it is missing any guards or other safety devices.
•
Maintain a balanced stance at all times so that you do not fall or lean against the saw
blade or other moving parts.
•
Never leave the machine running. Always make sure it has come to a complete stop
before leaving the machine.
Controls
•
ON / OFF Switch
(Figure 3 Item 1.1). Located on the right side of the control panel.
Press this switch to start or stop the machine.
•
Feed Control Knob
(Figure 3 Item 1.3). Located on the left side of the control panel.
The knob is the hydraulic cylinder feed control valve. It is used to set the amount of
force that is applied to the saw blade. The feed rate is proportional to the opening of
the valve. Increasing the valve opening (counterclockwise) increases the feed rate;
decreasing the valve opening (clockwise) reduces the feed rate.
•
Blade Speeds
(Figure 5). The band saw has four blade speeds. The different speeds
are obtained by changing the position of the motor drive V-belt on step pulleys.
Change blade speeds as follows. Caution: Change speeds only when the machine is
not running.
Figure 4: Recommended Main Power Supply Wire Sizes