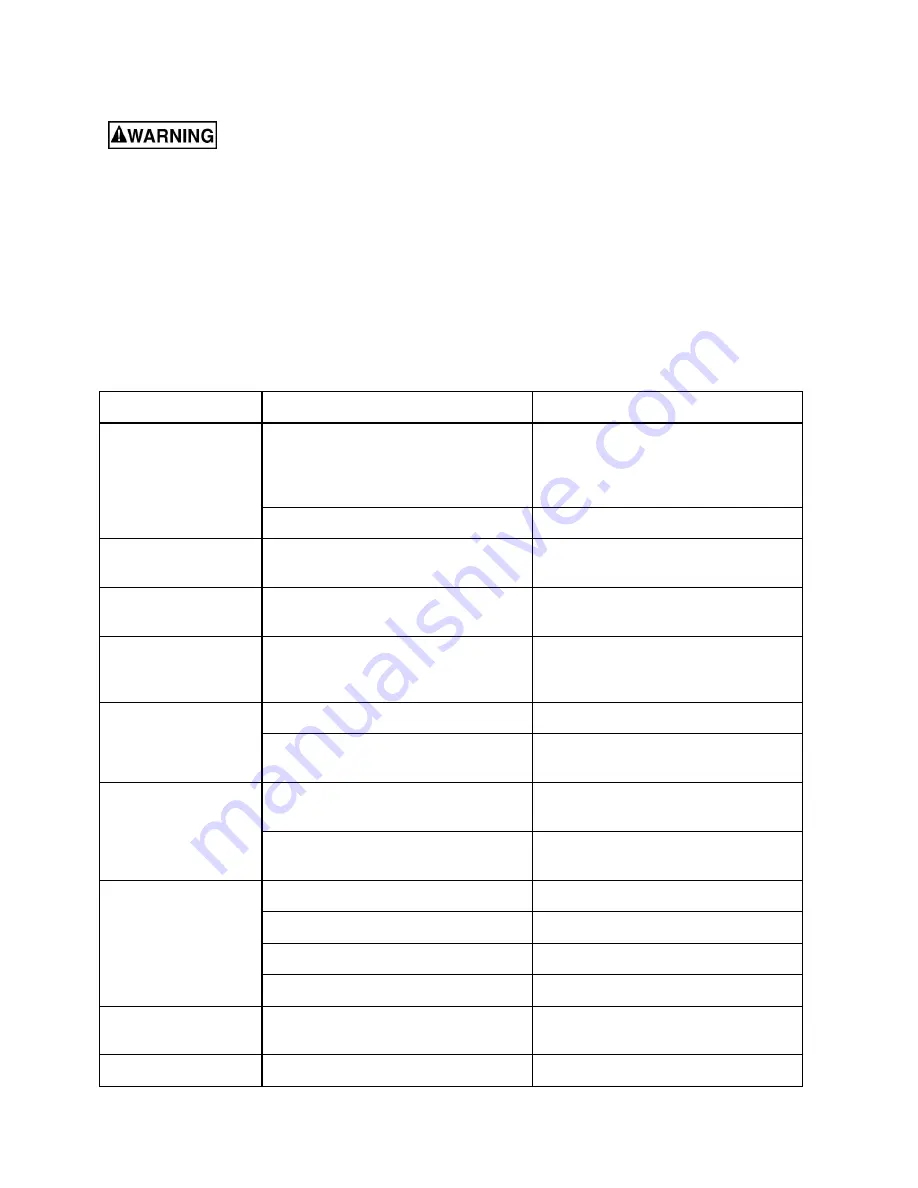
23
Maintenance
Before doing maintenance on
the machine, disconnect it from the electrical
supply by pulling out the plug or switching
off the main switch! Failure to comply may
cause serious injury.
For best results, perform the following
recommended procedures on a monthly basis:
•
Lubricate conveyor bushings and check for
wear.
•
Lubricate all moving parts, such as threaded
rods, washers, and bushings. (Bearings are
pre-sealed and require no lubrication.)
•
Clean sawdust from the abrasive strip and
the conveyor belt.
•
Blow dust from motors and switches. Blow
dust from inside of sanding drum.
•
Check all set screws for tightness on parts
such as bearings, conveyor and couplings.
Troubleshooting
Trouble Probable
Cause
Remedy
No incoming power.
Check plug connection. Make sure
fuse is not blown/circuit breaker is not
tripped. Push the circuit breaker
button on the sander motor to re-set.
Sander will not start.
Switch is malfunctioning.
Replace switch.
Conveyor motor
stalls.
Excessive depth of cut.
Reduce depth of cut; use coarser grit;
reduce feed rate.
Conveyor belt does
not move.
Shaft coupler is loose or unattached.
Adjust shaft coupler.
Conveyor rollers run
intermittently.
Shaft coupling is loose.
Align the shaft flats of the gear motor
and the drive roller and tighten the
shaft-coupling setscrews.
Slack in abrasive strip on drum.
Remove slack in strip.
Abrasive strip comes
off drum.
Abrasive improperly wrapped.
Read the section on wrapping
abrasive strips, pages 12-13.
Strip caught on inside edge of slot, or
on inboard side of drum.
Re-adjust the strip end in the slot
and/or trim the abrasive edge.
Abrasive strip is
loose.
Strip not cut properly.
Re-cut and re-install the abrasive
strip.
Excessive depth of cut.
Reduce depth of cut.
Excessive feed rate.
Reduce feed rate.
Inadequate dust collection.
Increase airflow at dust port.
Abrasive loads up
prematurely.
Inadequate abrasive.
Use an open-coat abrasive.
Line or groove in
stock.
Inconsistent feed rate.
Do not stop or change the feed rate
while feeding stock.
Snipe marks.
Improper tension on rollers.
Re-tension rollers (see page 19).
Содержание SandSmart 16-32 Plus
Страница 28: ...28 Conveyor and Motor Assembly ...
Страница 30: ...30 Drum Head Assembly ...
Страница 33: ...33 Electrical Connections ...
Страница 34: ...34 NOTES ...
Страница 35: ...35 ...
Страница 36: ...36 WMH Tool Group 2420 Vantage Drive Elgin Illinois 60123 Phone 800 274 6848 www wmhtoolgroup com ...