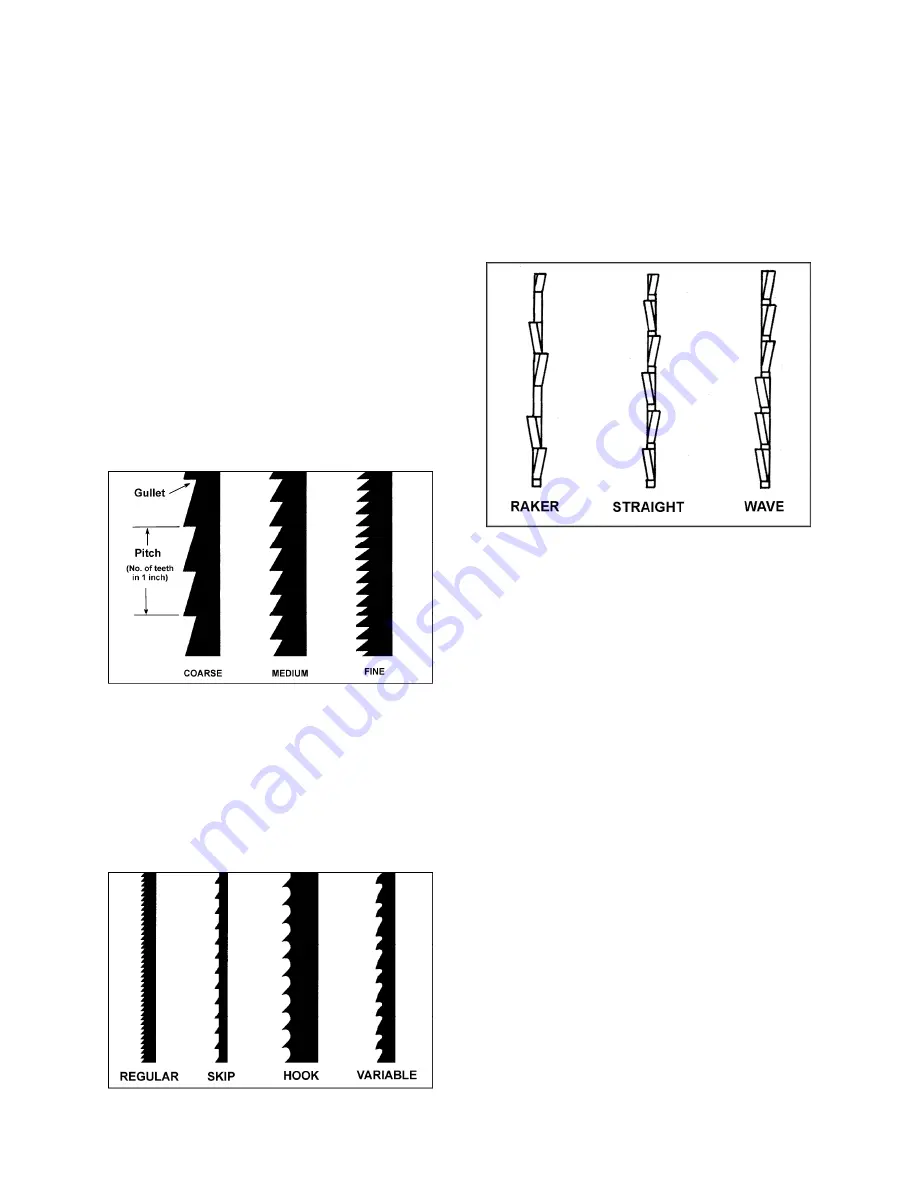
19
9.7
Width
Band saw blades come in different standard widths,
measured from the back of the blade to the tip of the
tooth. Generally, wider blades are used for ripping
or making straight cuts; narrower blades are often
used when the part being cut has curves with small
radii. When cutting straight lines with a narrow
blade, the blade may have a tendency to wander,
causing
blade lead
. (refer to
sect. 9.5).
9.8
Pitch
Pitch is measured in "teeth per inch" (TPI). Figure 9-
6 shows blades with different pitches. A fine pitch
(more teeth per inch) will cut more slowly but
smoother. A coarse pitch (fewer teeth per inch) will
cut rougher but faster. As a rule of thumb, the thicker
the workpiece, the coarser will be the blade pitch. If
you have to cut a hard or very brittle material, you
will probably want to use a blade with a finer pitch in
order to get clean cuts.
General rule:
Use a blade that will have no fewer
than 6 and no more than 12 teeth in the workpiece
at any given time.
Figure 9-6: blade pitch
9.9
Shape
Figure 9-7 shows common types of tooth shape.
Tooth shape has an effect on cutting rate, and with
few exceptions, the Skip and Hook types are used
to obtain higher feed rates when cutting thick
workpieces. Variable-tooth blades are also
available, which combine features of the other
styles.
Figure 9-7: blade shape
9.10
Set
The term "set" refers to the way in which the saw
teeth are bent or positioned. Set patterns are usually
selected depending on the type of material that
needs to be cut. Three common set patterns are
shown in Figure 9-8.
Generally, the
Raker
set is used for cutting metal
workpieces; the
Wave
set, when the thickness of the
workpiece changes, such as cutting hollow tubing or
structurals. The
Straight
set is most often preferred
when cutting wood or plastics.
Figure 9-8: blade set
9.11
Material
Band saw blades can be made from different types
of materials. Some of the most common include
spring steel, carbon steel, carbon steel equipped
with a high speed or welded edge (bi-metal), or
carbide tips. A special type of saw blade is made
from "high speed steel"; these should not be used
on band saws with low rates of speed.
Because of the importance of blade selection, it is
recommended that you use the
Blade Selection
Guide
in
sect. 11.0
.
9.12
Blade breakage
Band saw blades are subject to high stresses and
breakage may sometimes be unavoidable.
However, many factors can be controlled to help
prevent most blade breakage. Here are some
common causes for breakage:
1. Misalignment of blade guides
2. Feeding work too fast
3. Using a wide blade to cut a short radius curve
4. Excessive
tension
5. Teeth are dull or improperly set
6. Upper guides are set too high off workpiece
7. Faulty weld on blade
Содержание JWBS-14SFX
Страница 25: ...25 13 1 1 JWBS 14SFX 714401 Band Saw Assembly Exploded View ...
Страница 26: ...26 13 1 2 JWBS 14SFX 714401 Table and Miter Gauge Assembly Exploded View ...
Страница 35: ...35 ...
Страница 36: ...36 427 New Sanford Road LaVergne Tennessee 37086 Phone 800 274 6848 www jettools com ...