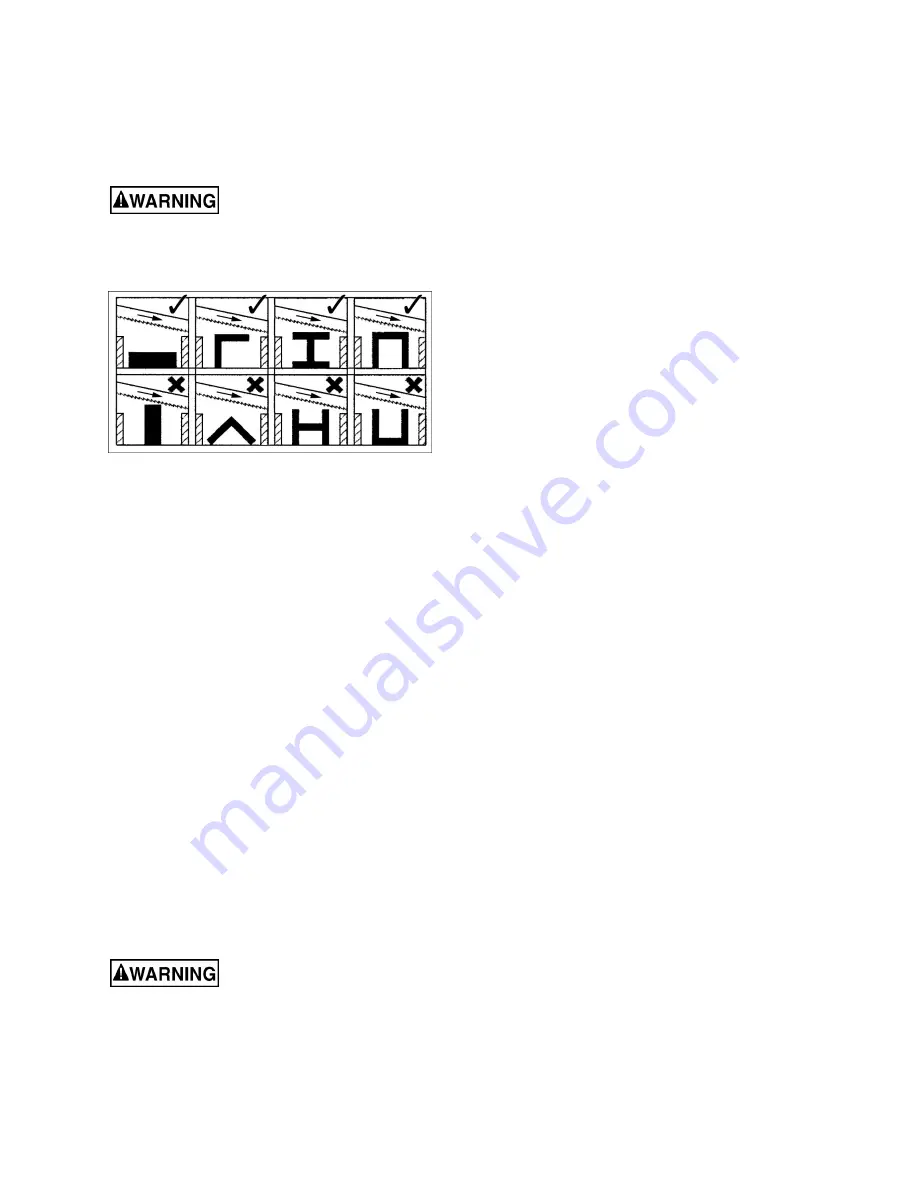
14
The top row shows acceptable clamping
positions, the bottom row shows
un
acceptable
positions.
If the thickness of profile section is very thin, a
piece which duplicates the profile should be
fitted inside the workpiece itself, to prevent
workpiece being crushed between the jaws.
Do not load/unload material
from vise while machine is running. Never hold
workpiece by hand when cutting; workpiece
must be firmly secured in vise. Do not reach into
cutting area during cutting operations.
Figure 23: clamping positions
3. Adjust blade guides to minimize exposed blade
area.
4. Release support and turn on saw. Lower bow
until blade contacts material. Release bow to
allow cutting to proceed. Weight of bow in
conjunction with spring tension will force blade
through material until cut is finished.
5. Switch trip tab must turn off saw at completion
of cut.
8.3
Evaluating cutting efficiency
Is the blade cutting efficiently? The best way to
determine this is to observe the chips formed by the
cutting.
If chip formation is powdery, then the feed rate is
much too light, or the blade is dull.
If chips are curled, but colored — that is, either blue
or straw-colored from heat generated during the cut
— then the feed rate is too high.
If chips are slightly curled and are not colored by
heat, the blade is sufficiently sharp and is cutting at
its most efficient rate.
9.0
User-maintenance
Always disconnect power to
the machine before performing maintenance.
Failure to do this may result in serious personal
injury.
Wipe down saw with a soft rag after each use, and
clear metal particles with a small paint brush or parts
cleaning brush. Do not use compressed air, as it
may force chips into the guide bearings and other
critical areas of saw.
Periodically apply a light coat of oil on exposed
metal surfaces to inhibit rust.
Make frequent inspections of motor fan, and blow
out (with low pressure air hose) or vacuum any
accumulation of foreign material to maintain normal
motor ventilation.
Keep blade guides clean and free of metal particles.
Check guide bearings frequently to make sure that
they are properly adjusted and turning freely.
Periodically inspect belt for wear or fraying. Replace
if needed.
Inspect power cord; if worn, cut or damaged in any
way, have it replaced immediately.
9.1
Lubrication
Ball bearings on blade guide assemblies and blade
wheels are permanently lubricated and sealed, and
should require no further lubrication.
Lubricate the vise lead screw as needed with #2
tube grease.
Drain and refill gear box oil after first 90 days of
operation. Thereafter, change every six months.
Use MOBIL SHC 634 or equivalent.
To change gear box oil:
1. Disconnect machine from power source.
2. Place bow in horizontal position. Loosen or
remove screw and nut on motor tension plate
(see A, Figure 12). Remove drive belt and allow
motor to drop away, for access to gearbox.
3. Remove four screws from gear box (Figure 24)
and remove cover plate and gasket.
4. Hold a container under lower right corner of
gear box with one hand while slowly raising bow
with the other. Drain completely.
5. Place arm in horizontal position. Wipe out
remaining oil with a rag.
6. Fill gear box with approximately 1/2 pint of
MOBIL SHC 634.
7. Replace gasket and cover. Fasten cover with
screws.
8. Reinstall and tension drive belt, and secure nut
on tension plate (A, Figure 12).
Содержание HVBS-56
Страница 17: ...17 11 1 1 HVBS 56 Bow Assembly Exploded View...
Страница 18: ...18 11 1 2 HVBS 56 Bed Assembly Exploded View...
Страница 23: ...23 12 0 Electrical Connections HVBS 56 Band Saw...