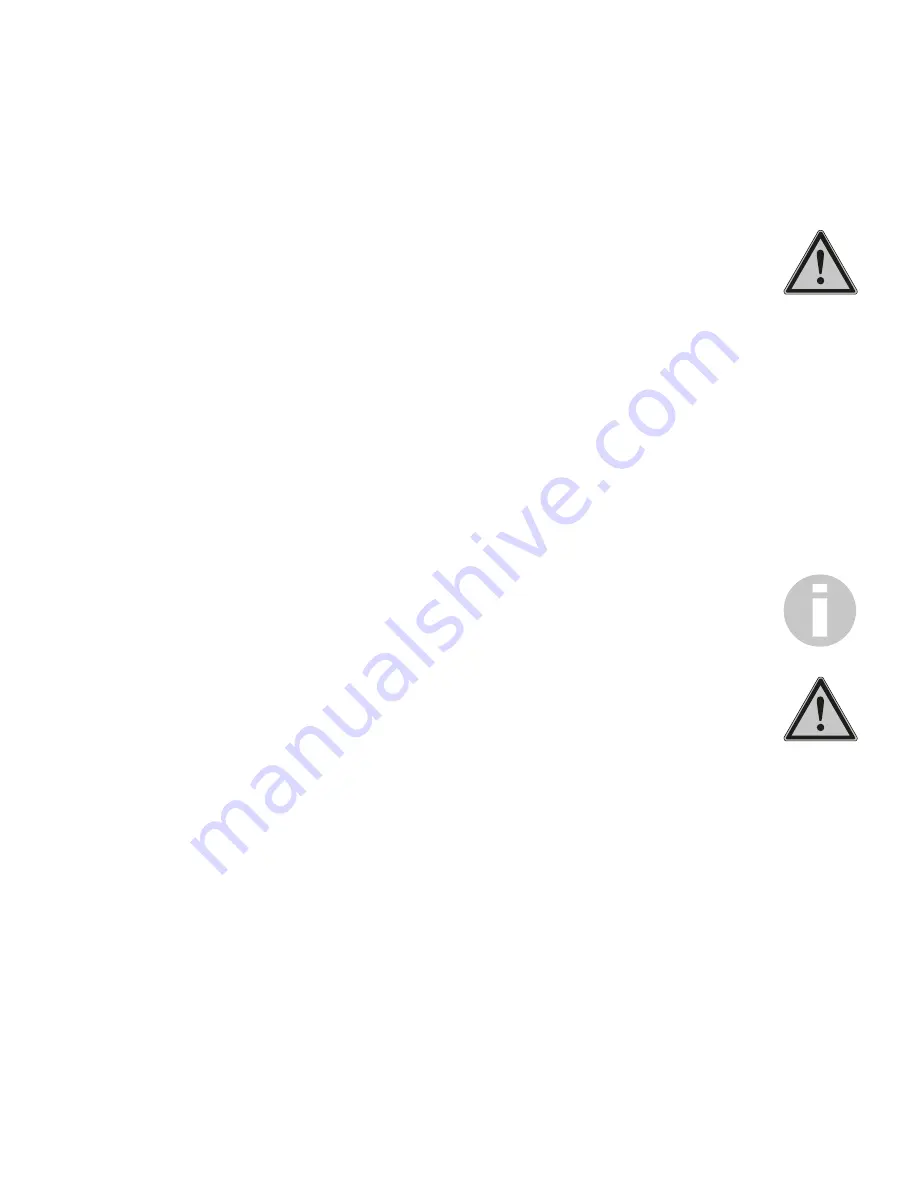
7. Installation
7.1 General information
Local rules and regulations must be taken into account when selecting a dosing pump for designing a
system, and for installation and operation. This applies to the selection of the appropriate materials for the
dosing pump, the handling of chemicals, and electrical installation. The technical data of the dosing pump
(Section 5) must also be taken into consideration. The system must be designed accordingly (e.g. pressure
loss in lines depending on nominal diameter and length).
NOTE!
The size of the lines used in connection with MAGDOS DE/DX 12 must be at least DN 6. DN 4 should only
be used for short lines (up to 1 m) and low-viscosity media (<20 mPa s) .
The designer and operating company are responsible for ensuring that the entire system, including the
dosing pump, is designed in such a way that neither system equipment nor buildings are damaged in the
case of chemical leakage due to the failure of wearing parts (e.g. diaphragm rupture) or burst hoses. If the
chemical system represents a potential source of danger, the installation must be designed in such a way
that no unreasonable consequential damage occurs, even if the dosing pump fails. We therefore recom-
mend installing leakage monitors and collecting pans.
The drain socket of the dosing head must be visible so that a diaphragm rupture can be detected. Drainage
should be able to flow freely downward through the drain pipe.
To increase the dosing accuracy and to ensure the functional reliability, we recommend the use of additional
accessories. These include pressure control valves, pressure relief valves, leakage monitors and low level
indicators, as shown in the installation examples.
Always use appropriate tools for the installation of plastic connection parts. To avoid damage, never apply
excessive force.
IMPORTANT!
Plastic parts (especially PVC parts) can be tightened and loosened more easily by applying lubricant (e.g.
silicone grease) to the thread beforehand.
To prevent seizing, threaded stainless steel parts (e.g. dosing head and valves) must be lubricated before
being assembled (e.g. with PTFE spray).
ATTENTION!
Compatibility of the lubricant with the metered chemicals must be checked.
7.2 Installation location
The installation location of the dosing pump must be easily accessible by operating and service personnel.
It is possible that the running noise of the dosing pump is transmitted through the piping, thus resulting in a
disturbing noise level. Installation of the dosing pump on a wall bracket should be preferred in such cases.
For the same reason, it is recommended to mount the pump on an outside wall and not on inside walls with
adjacent rooms used for residential purposes. When installing the dosing pump below the liquid level, care
must be taken to ensure that chemical leakages due to a broken diaphragm cannot cause any damage
(collecting pan, leakage sensor).
It is also possible to mount the pump directly on the chemical tank.
Pay attention to the maximum permissible ambient temperature of the dosing pump (refer to Technical
Data). Radiant heat from apparatus and heat exchangers must be shielded so that heat from the dosing
pump can be dissipated sufficiently. Avoid exposure to direct sunlight. If the dosing pump is installed
outside, provide a roof to protect it from the effects of weather.
Installation | Operation & Maintenance Instructions |
11