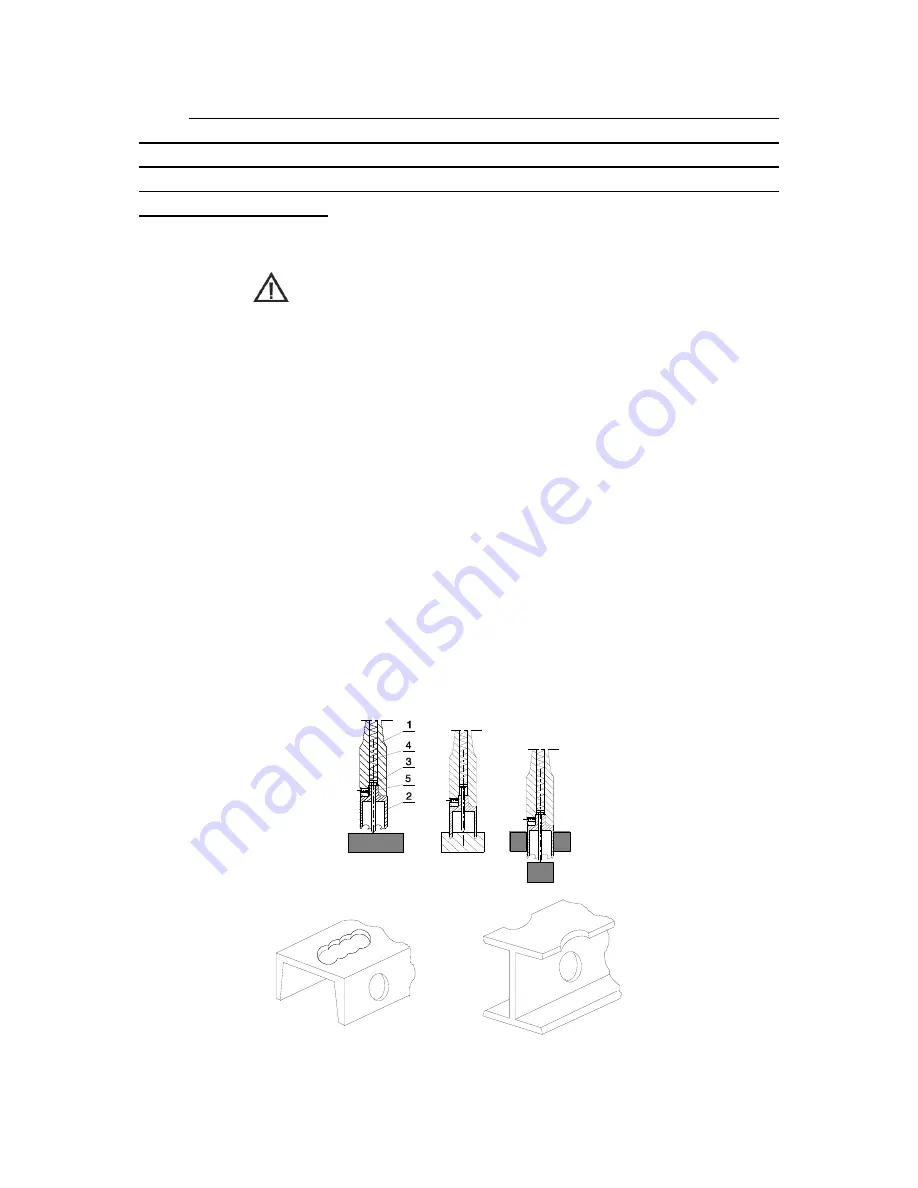
JEI SOLUTIONS LTD
MAGBEAST 2
Operator’s manual for Drilling Machine
MAGBEAST 2
- 5 -
DO NOT use drill
on steel thinner than (less than 3/8” (10 mm)). On thin
steel (less than 3/8” (10 mm)) magnet’s adhesive power would be significantly
reduced what can cause machines failure or individuals injury. The machine
should be located on the work piece with the entire surface of the
electromagnetic base! It is recommended that each time, before positioning
the machine surface under the electromagnetic base should be sanded down
with abrasive paper!
Please keep all recommendations.
II. START UP AND OPERATION
1. Cutters and optional equipment features
This dril
ling machine’s spindle has a socket with Morse taper 2 which make possible
to use twists drill (if it necessary with using drill sleeves) or milling cutters by using AMT
Arbor for fixing them in socket spindle taper [Drawing 2].
Milling cutter (2) is located inside arbor body (1) and is fastened with screws (3).
While fastening the cutter in the socket, be aware that screws should be screwed tight so
that they could not come unscrewed. It is important to position the cutter in relation to the
socket in such a way that fixing flats on the cutter shank are positioned opposite to the fixing
screws (3). Both fastening screws(3) should be used to fasten the cutter. Pilot (5) is located
inside the cutter. It makes it easier to position milling cutter over centre of a planned hole.
During drilling as the cutter goes deep into steel, the pilot moves back into the arbor body
and tightens discharge spring (4). That spring ejects slug which is a by-product of milling a
hole with a centre free cutter.
Basically milling cutters are designed to make through holes. On occasions when
there is a need for an overlapping hole pilot should not be used. [Drawing 3]
Drawing 3. A few types of holes that can be done with a milling cutter.
Drawing 2. Principle of milling cutter’s work