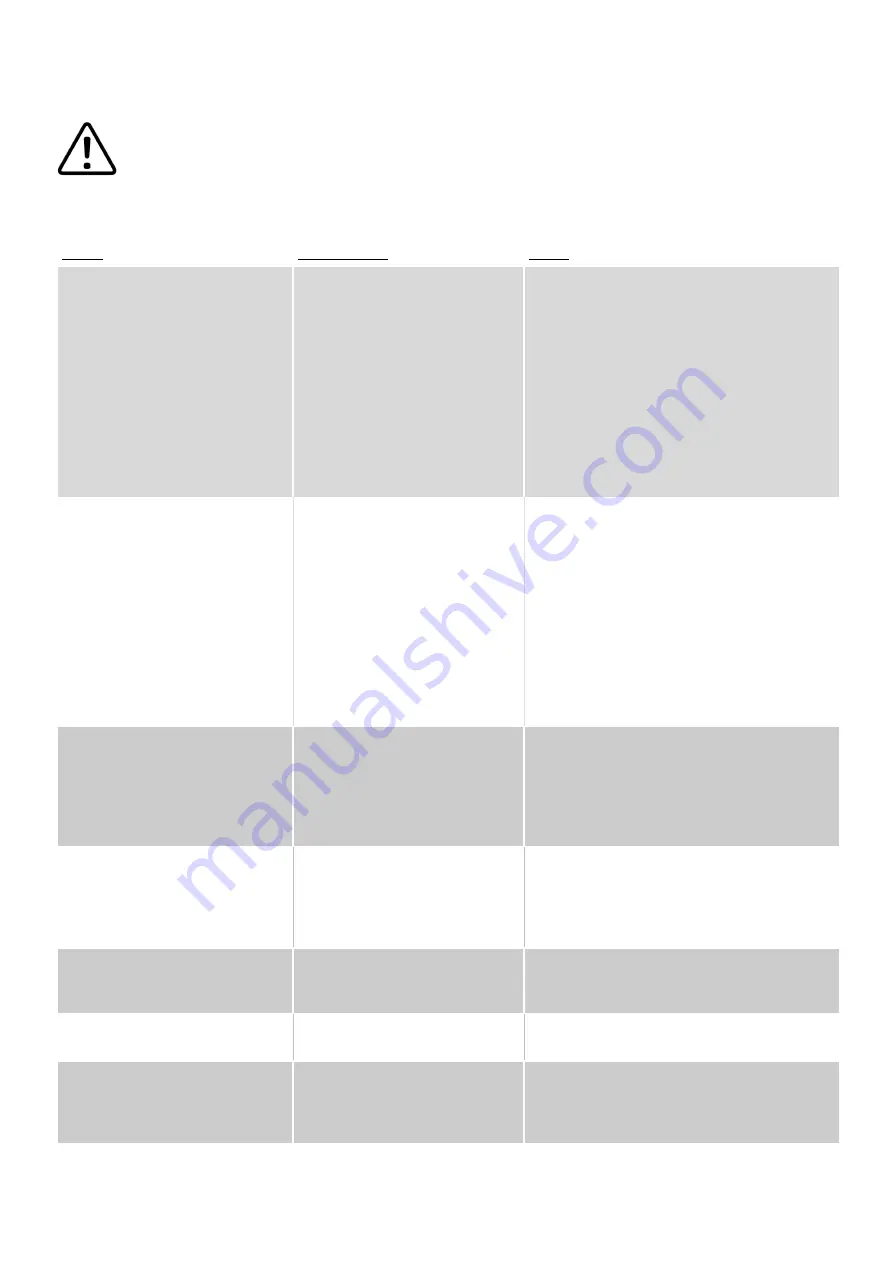
27
MIG WELDING PROBLEMS
Before starting any welding activity ensure that you have suitable eye protection and
protective clothing. Also take the necessary steps to protect any persons within the welding
area.
MIG welding defects and prevention methods
Defect
Possible cause
Action
Porosity (within or outside the bead)
Poor material
Insufficient shield gas flow
Gas flow too low/high
Leaking hoses
Faulty gas valve
Working in open area with drafts
Check the material is clean
Check hoses and MIG torch for blockages
Check the regulator setting or that it is not frozen
due to a high flow
Check all hoses for leaks
Call a service engineer
Put screens up around the weld area
Poor or inconsistent wire feed
Incorrect pressure on wire drive
causing burn back to contact tip or
bird nesting at the feed roll
Damage to torch liner
Welding wire contaminated or rusty
Worn welding tip
Readjust the upper feed pressure
Increase the pressure to eliminate burn back to
tip
Decrease pressure to eliminate bird nesting
Replace torch liner
Replace wire
Check and replace welding tip
No operation when the torch switch
is operated
Torch switch faulty
Fuse blown
Faulty PCB inside the equipment
Check the torch switch continuity and replace if
faulty
Check fuses and replace if necessary
Call a service engineer
Low output current
Loose or defective work clamp
Loose cable plug
Power source faulty
Tighten/replace clamp
Re-fix plug
Call a service engineer
No operation
No operation and mains lamp not lit
Faulty power source
Check mains fuse and replace if required
Call a service engineer
Excessive spatter
Wire feed speed too high or
welding voltage too low
Reset the parameters according to the weld
to be made
Excessive penetration, the weld
metal is below the surface level of
the material and hangs below
Heat input too high
Poor weld technique
Reduce the amperage or use a smaller electrode
and lower amperage
Use correct welding travel speed