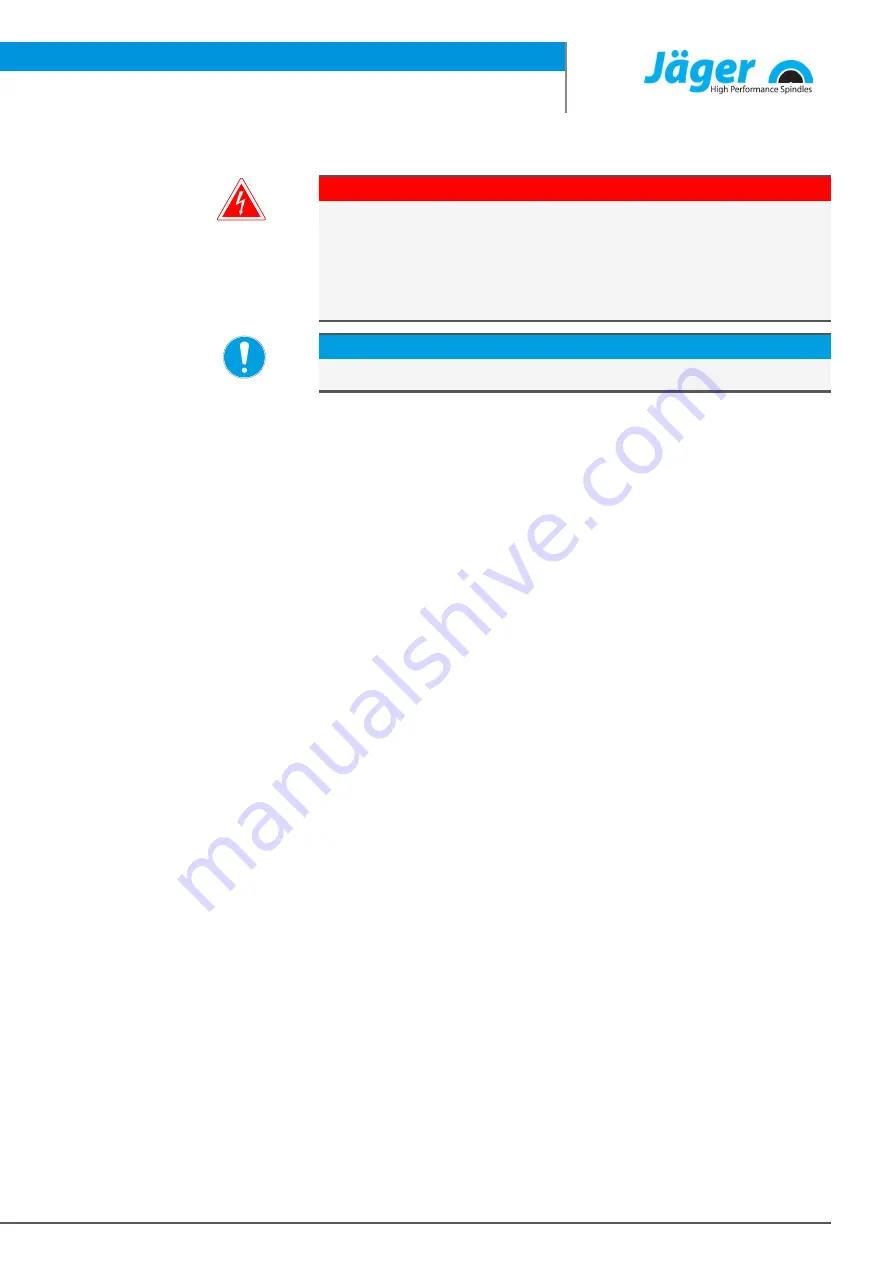
Service and repairs
Item no. 10405047-06, Revision 02
43 ( 48 )
14
Service and repairs
DANGER: Electric shock.
Electric shock can lead to severe burns and life-threatening injuries.
Take measures to prevent hazards caused by electrical energy (for details re-
fer e.g. to the regulations issued by the VDE and the local energy supply
companies).
u
Before commencing work, switch off the power supply of the HF spindle.
Note: Damage due to electrostatic discharge.
Do not touch the electrostatic-sensitive components of the HF spindle.
14.1
Service partners
Only certified service partners may open and repair the spindle. Failure to
comply with this voids any warranty claims and compensation claims for dam-
ages.
Ü
The list of partners can be found on the following website.
https://www.nakanishi-jaeger.com/en/contact/service-partners