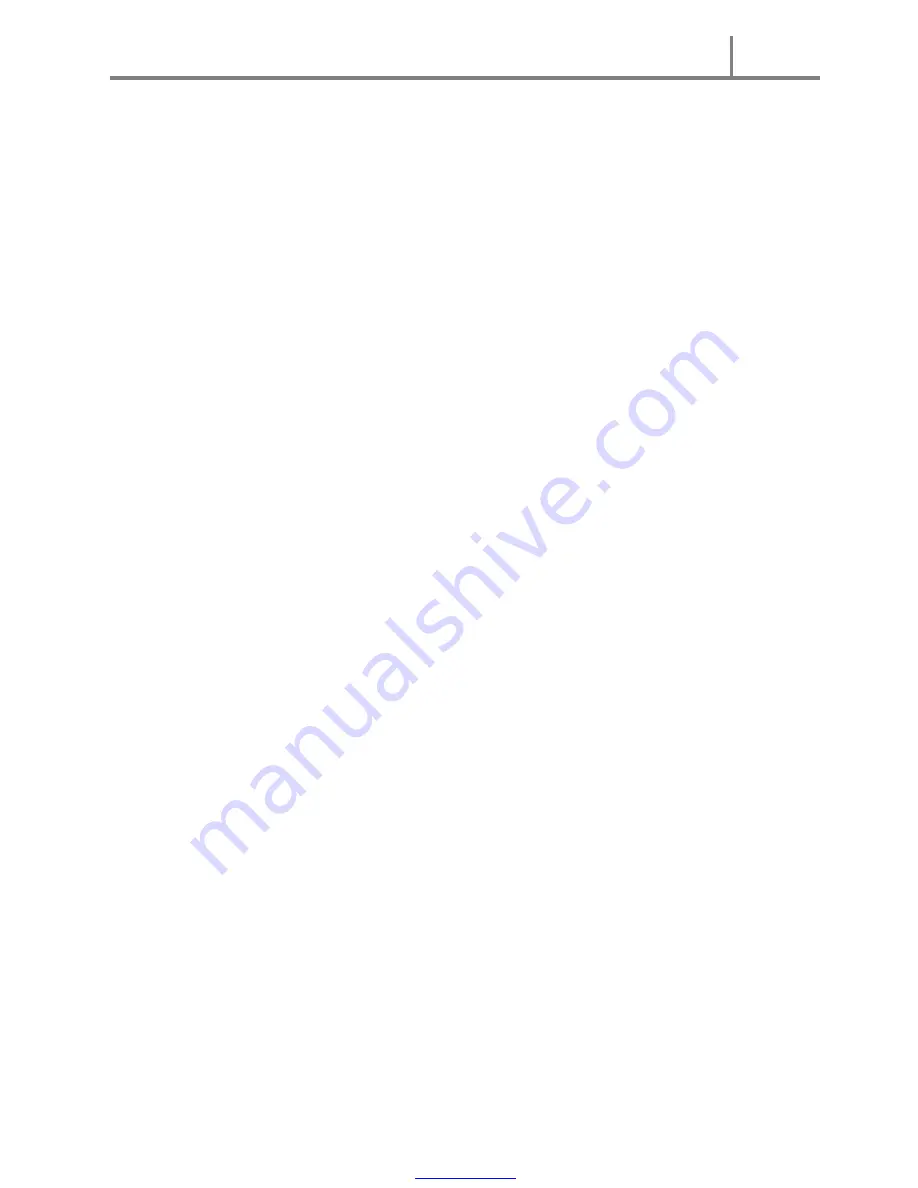
JAG
flocomponents FB2 IOM
2012
Page
3
of
8
www.JAGvalve.com
JAG.FB2.IOM.Rev.0
SECTION 1 - STORAGE
1.1
Pre Despatch
Non corrosion resistant valves shall be
primed and/or painted.
After testing and before shipment, valves
shall be drained of test fluid.
Parts and equipment shall have exposed
bare metallic surfaces protected with a rust
preventative which shall not become fluid
and run at temperatures less than 125°F.
Exposed sealing surfaces shall be protected
from mechanical damage for shipping.
Valves not destined for immediate use will
be adequately prepared and packed before
shipping in such a way as to avoid any
possible damage during transport and
during the subsequent storage period before
use.
Relevant valve certification is always
included in shipment.
1.2
Customer Storage Instruction
If possible it would be advisable to leave the
valves in their own packing cases and/or
pallets during the entire period of storage. In
either case, to prevent damage, the
protective covers on the flanges of every
valve must not be removed. The valves
must always remain in an OPEN position.
It is advisable that storage conditions be
closed and dry. The valves should be stored
in weatherproof conditions in a building with
an adequate roof.
Gearboxes and actuators are supplied and
shipped already assembled with their
relative Valves and fitted with additional
equipment (e.g. Limit Switches / Solenoids)
as required by the customer contract.
Caution must be taken to ensure that all
protective covers on this equipment are not
removed until installation.
2.1
Unpacking and Inspection
Care should be taken during unpacking of
valves.
It is advisable to check valve exterior for
shipping damage and any damage should
be reported to the Quality Assurance
Manager immediately.
All
JAG
flocomponents valves are supplied
with the ball in the open position and
protective covers on both ends.
Ensure end covers remain securely in place
until the valve is ready for installation.
This will prevent ingress of dirt and damage
to ball surface and end connection surface
finish.
Please also check that valve certification is
correct to the requirements.
SECTION 3 - PRE-INSTALLATION
3.1
Pre Installation
Before installation check to ensure size,
pressure rating, end connection and material
of construction are suitable for required
service conditions.
Remove dirt/debris that may have
accumulated in the valve during long term
storage and always maintain valve
cleanliness during installation procedure.
In particular weld spatter should be kept
clear of valve seats as this could result in
damage to the soft seats and valve
malfunction.
SECTION 4 - HANDLING
4.1
Handling
On valves with restricted space between the
flanges handling is achieved by slinging the
valve on the neck diameter behind each of
the pipe flanges.
NB. Webbed slings should be used at all
times.
SECTION 5 - INSTALLATION
5.1
Installation
JAG
flocomponents valves can be supplied
with various end connections.
Ensure that the pipe work, flanges, etc., are
square, true and that pipes are properly
supported to prevent line buckling, which
could result in excessive stress on the valve.
Dependent on the application, the joint/
gasket selection and bolting torques as
recommended by the joint/gasket
manufacturer[s] should be observed to
maintain sound, tight joints.
Butt Weld End Valves - during welding all
possible efforts should be taken to stop the
ingress of weld slag into the pipeline.