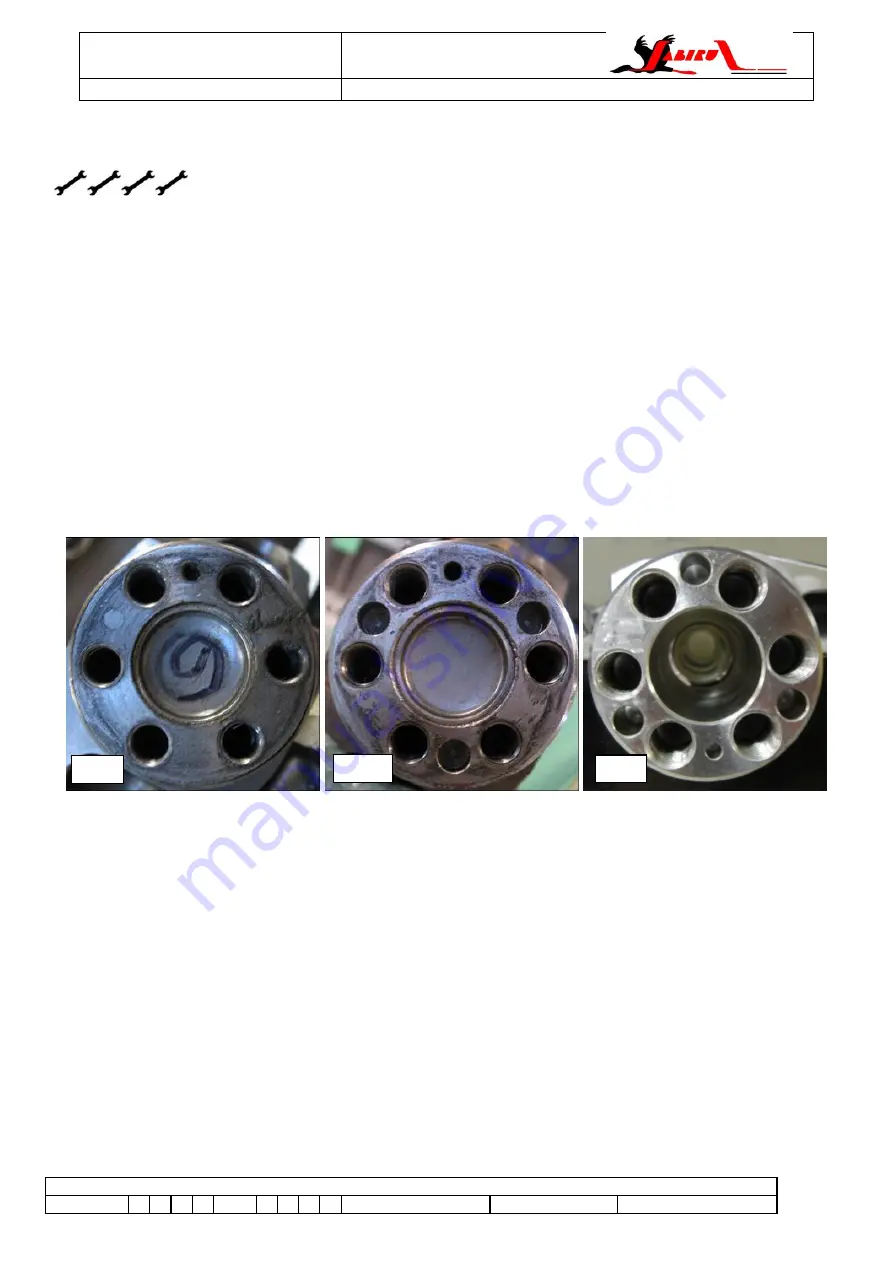
Engine Overhaul Manual
Jabiru Aircraft
Pty Ltd
Jabiru 2200 & 3300 Aircraft Engines
This document is controlled while it remains on the Jabiru server. Once this no longer applies the document becomes uncontrolled.
ISSUE
1
2
3
4
5
6 7
Dated : 28/10/2014
Issued By: AS
Page: 59 of 201
L:\files\Manuals_For_Products\Engine_Manuals\Overhaul_Manual\JEM0001-7_Overhaul_Manual_DRAFT_(29_10_14).docx
5.9 Subassembly A
– Crankshaft, propeller flange and connecting rods
5.9.1 Crankshaft and propeller flange
5.9.1.1
Mandatory updates
There are main 2 types of flywheels: alloy centred and the later model steel centred (commonly called
the ‘starfish’ centre).
If you have the alloy centred flywheel, check that the flywheel is dowelled to the crankshaft with 3 x
6mm dowels and retained with 6 x 5/16” x 1¼” UNF cap screws. Crankshafts using ¼” screws for
flywheel retention must be replaced.
Engi
nes with the “starfish” flywheel are retained with 6 x 5/16” x 1” or 6 x 3/8” x 1” UNF cap screws.
The flywheel end of the crankshaft should look like the “5/16”” or “3/8”” photos in Figure 63.
If this is not the case and the flywheel end of your crankshaft looks like the “Old” photo then the
crankshaft and flywheel must be modified before return to service and a new crankshaft timing gear
must be purchased. Details of the process are given in Section 12.4.2.
If the drilling and dowelling modification is required, complete the other cleaning and inspection steps
below to determine if the crankshaft is fit for return to service in all other respects before sending it
away for modification.
Several different length dowels have been used: older flywheels without the “starfish” use 24mm long
dowels.
Engines using the “starfish” initially used 20mm long dowels while later versions reverted to
24mm. Refer to Section 13 for serial number ranges. In all cases the dowels are 6mm in diameter.
Figure 63
– Crankshaft End Detail (Dowel Holes)
5.9.1.2
Mandatory Discard
Any crankshaft which has been subjected to a forced stoppage
– for example from a severe prop strike
or piston failure
– must be discarded. Section 3.4 refers.
5.9.1.3
Optional Updates: Crank / Propeller Flange
It is strongly recommended that during a full overhaul or bulk strip the engine configuration be updated
to include 8mm dowels between the crankshaft and the propeller flange for those engines not built with
this feature originally. This may require the replacement or modification of the propeller flange and
crankshaft. Refer to Table 40 for S/No. at which this was introduced to production engines.
Old
5/16”
3/8”