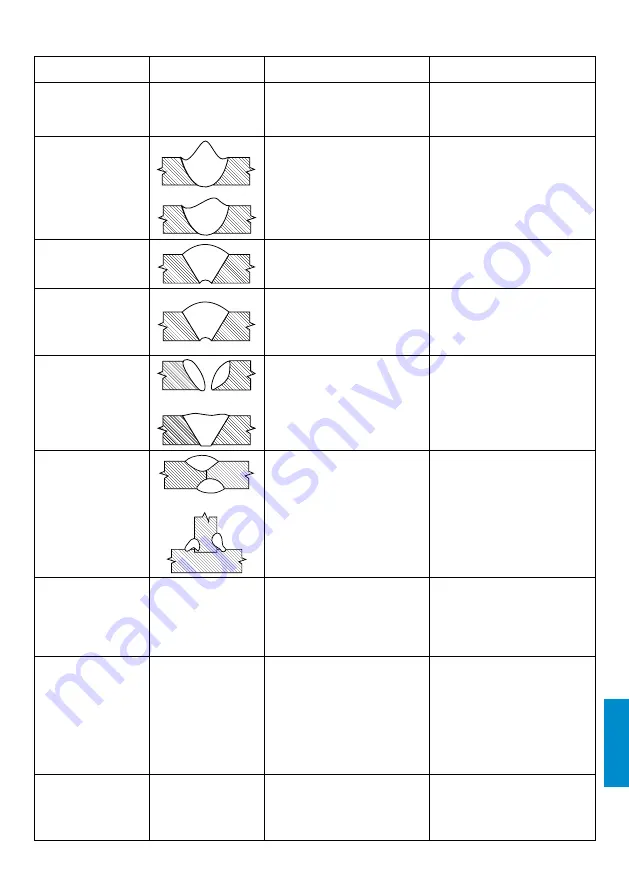
HU
EN
Table 9: Welding Line Faults, Causes and Preventive Measures of SAW Automatic Welding
Faulty category
Shape & feature
Cause
Preventive measures
Unequal welding line Inconsistent welding
line width
· Unstable welding speed;
· Unstable welding feeding;
· Unstable tip contact
· Remove circuit failures;
· Adjust the wire feeding
wheel;
· Replace the tip.
Undercut
· Too fast welding;
· Too high welding current;
· Too high arc voltage;
· Unaligned welding wire end.
· Slow down or adopt double-
arc or multiarc welding;
· Reduce welding current;
· Lower welding voltage;
· Calibrate welding wire posi-
tion.
Counter
concave
· Too high flux backing pres-
sure
· Improve the flux backing
Overflow
· Too long welding wire exten-
sion;
· Too small groove;
· Too low arc voltage;
· Unaligned welding wire end.
· Reduce extension length;
· Change groove size;
· Increase arc voltage;
· Calibrate welding wire posi-
tion.
Welding through
and back welding
line too high
· Too high welding current;
· Too slow welding;
· Too large groove clearance;
· Loose backing.
· Reduce welding current;
· Speed up welding;
· Improve assembly quality;
· Improve the compression
unit.
Lack of
penetration
· Too low welding current;
· Too high welding speed;
· Too high arc voltage;
· Unaligned welding wire end;
· Too large grid pressure fluc-
tuation.
· Properly increase current;
· Slow down welding;
· Lower arc voltage
· Straighten the welding wire
and adjust welding head
position;
· Avoid power use peak.
Air holes
· Column channel
· Single or group
along the center
of the welding line
· Dirty or non-cleaned base
metal;
· Incomplete welding wire rust
or oil removal; ·Wet flux;
· Bad flux ingredients or perfor-
mance
· Clear the base metal;
· Dry the flux;
· Replace it with proper one.
Heat cracks
· Horizontally or
vertically along the
welding line
· On both ends in
single-side welding
and both-side
formation.
· Over-segregation of low-
melting-point sulfide;
· No sufficient restraint force
in the crystallization of end
welding line.
· Choose the welding wire
containing low carbon or
sulfur but high manganese
or the flux of low silicon and
high manganese;
· Properly add run-on tabs,
keep proper weight and
welding tightness and
adopts grooved run-on tabs.
Interlaid dregs
· In case of multi-layer welding,
dregs not cleaned com
-
pletely between layers;
· Unaligned welding wire end
in final welding
· Completely clean the dregs
between layers;
· Adjust welding head position.
29
Содержание SW-1250
Страница 16: ......
Страница 19: ...HU EN INDEX INTRODUCTION 32 MAIN PARAMETERS 33 INSTALLATION 34 OPERATION 35 CAUTIONS 36 19...
Страница 35: ......
Страница 36: ...www iweld hu...