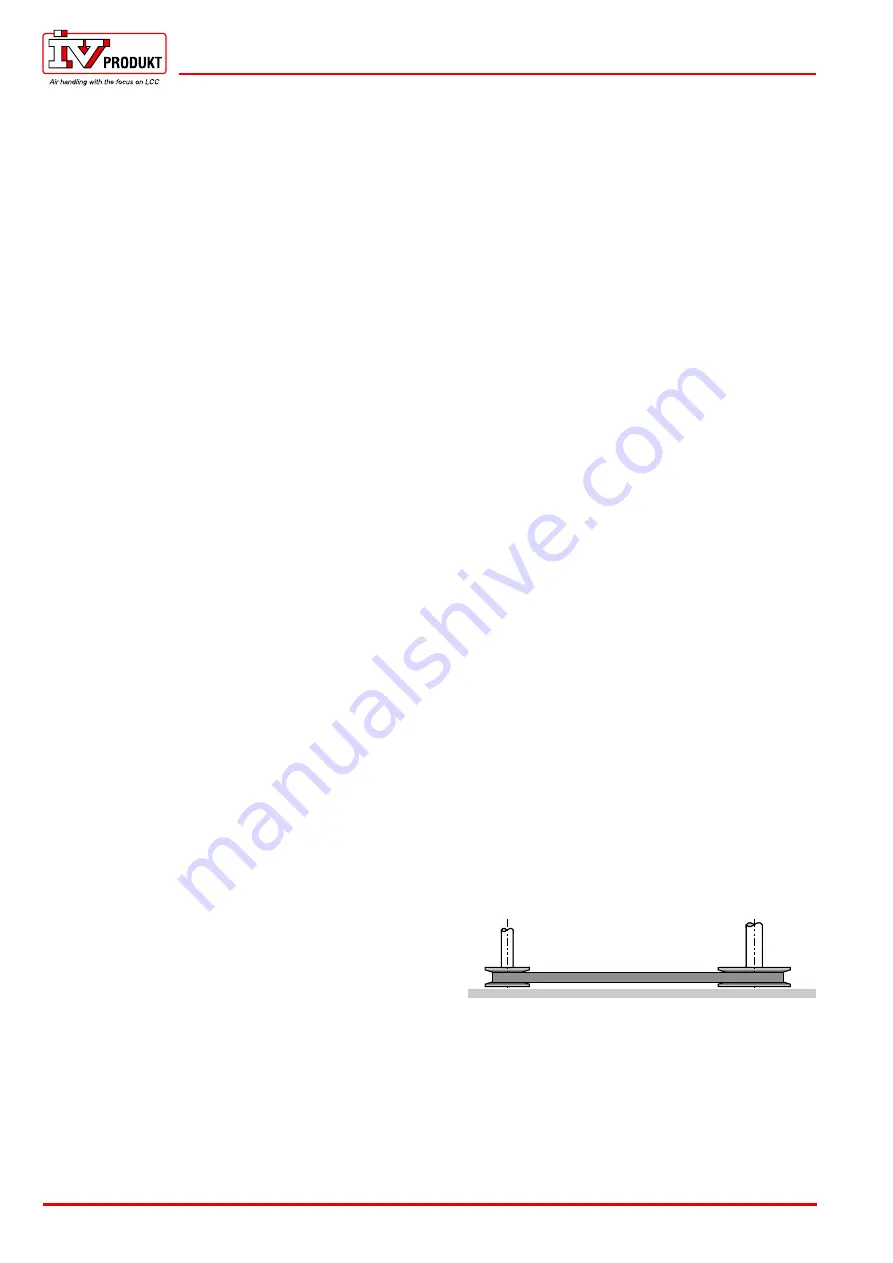
Continuous product development at IV Produkt may give rise to specification changes without notice.
Flexomix 060-950
DU11.F.081008.01GB
Operation and Maintenance
Instructions
Fan
General
The function of the fan is to transport air through the system,
i.e. the fan must overcome the air stream resistance present
in air diffusers and grilles, the ducting and the air handling
unit.
The fan speed is adjusted to provide the correct airflow. If
the fan generates a lower airflow, this may disturb ventilation
system performance.
If the supply airflow is too low, there will be imbalance in
the system and this may cause draught problems. If the
ventilation capacity is too low, this may contribute to poor
room climate. If the extract airflow is too low, poor ventila-
tion capacity will result. Imbalance can also lead to damp air
being pressed out into the building structure. An excessively
low extract airflow causes increased power consumption if
a means of heat recovery is installed.
The reason why the fan impels too little air may be that the
v-belts are slipping. This may also be due to the effect of
dust deposits on the impeller blades.
If a centrifugal fan rotates in the wrong direction, the air will
flow in the correct direction but with reduced capacity. The
direction of fan rotation may have been changed as a result
of electrical installations. The direction of rotation should
therefore be checked.
Measures
N.B.! Before beginning work, switch off the air handling
unit from its switch and then turn the safety isolating
switch to the 0 position.
If the unit has double motors, there may be two switches.
1. Fan
What to check
Check that the fan impeller rotates easily, is in balance and
does not vibrate, and that the impellers are securely seated
on their shafts and that they have not shifted sideways toward
the inlet cones. Imbalance may be due to dust deposits on
or damage to the impeller blades.
Check by listening to hear whether any damage has arisen
in the bearings. Place a screwdriver, or the like, against the
bearing housing and listen with your ear against the screw-
driver handle. Normally you should hear only a humming
sound. If you hear a squeaking sound, the bearings need to
be lubricated. A scraping sound indicates that foreign par-
ticles have penetrated the bearing. A regular metallic noise
indicates that the bearing is damaged. In both these cases
the bearings should be replaced by new ones.
The fan impeller, bearing housing and motors are mounted on
a vibration-isolated base plate with anti-vibration mountings.
Check that the mountings are firmly secured and are intact.
Inspect the safety guards, flexible connection, mounting
bolts and suspension devices, anti-vibration mountings and
base frame/stand.
Check that the impellers are clean, free of dust deposits.
Check tht the belt pulley mounting bolts are tight.
Cleaning
Wipe the fan impeller blades clean to remove possible dust
deposits. For this, you can use a mixture of Toluene and
denatured alcohol (2:1) or white spirit if required. Do not use
kerosene since it can cause rust to form on surfaces.
Then vacuum clean the air handling unit to prevent dust from being
discharged out into the duct system.
Clean the fan casing in the same way as the impellers.
Check that the enclosures and inlet cones are correctly secured.
Lubrication
If the fan bearing blocks are fitted with lubricators, lubricate
if required with SKF ALFA LUBE LG MT2 grease. In other
cases, the bearings are permanently lubricated and normally
do not require additional lubrication.
2. Belt Drive
Inspection
Check that the drive belts are not worn, broken, dried out
or damaged in any way. If the belts are damaged, they must
be replaced. If more than one belt must be replaced, you
must replace all the belts. Check that the belts are correctly
tensioned. Excessive tensioning can cause the bearings to
overheat and can overload the motor. Too loose tension will
cause the belts to slip and become quickly worn.
To replace or tension the belts
Tension the belts by moving the motor by means of the ten-
sioning bolts of the motor base plate. Do not force the belts
over the pulley, first release the tensioning bolts.
When changing belts, check that the pulley grooves are not
worn.
Use a ruler to check that the belt pulleys are parallel and that
their grooves are in alignment, see Fig 2.
Note that new belts should be re-tensioned after about
14 days.
Fig. 2