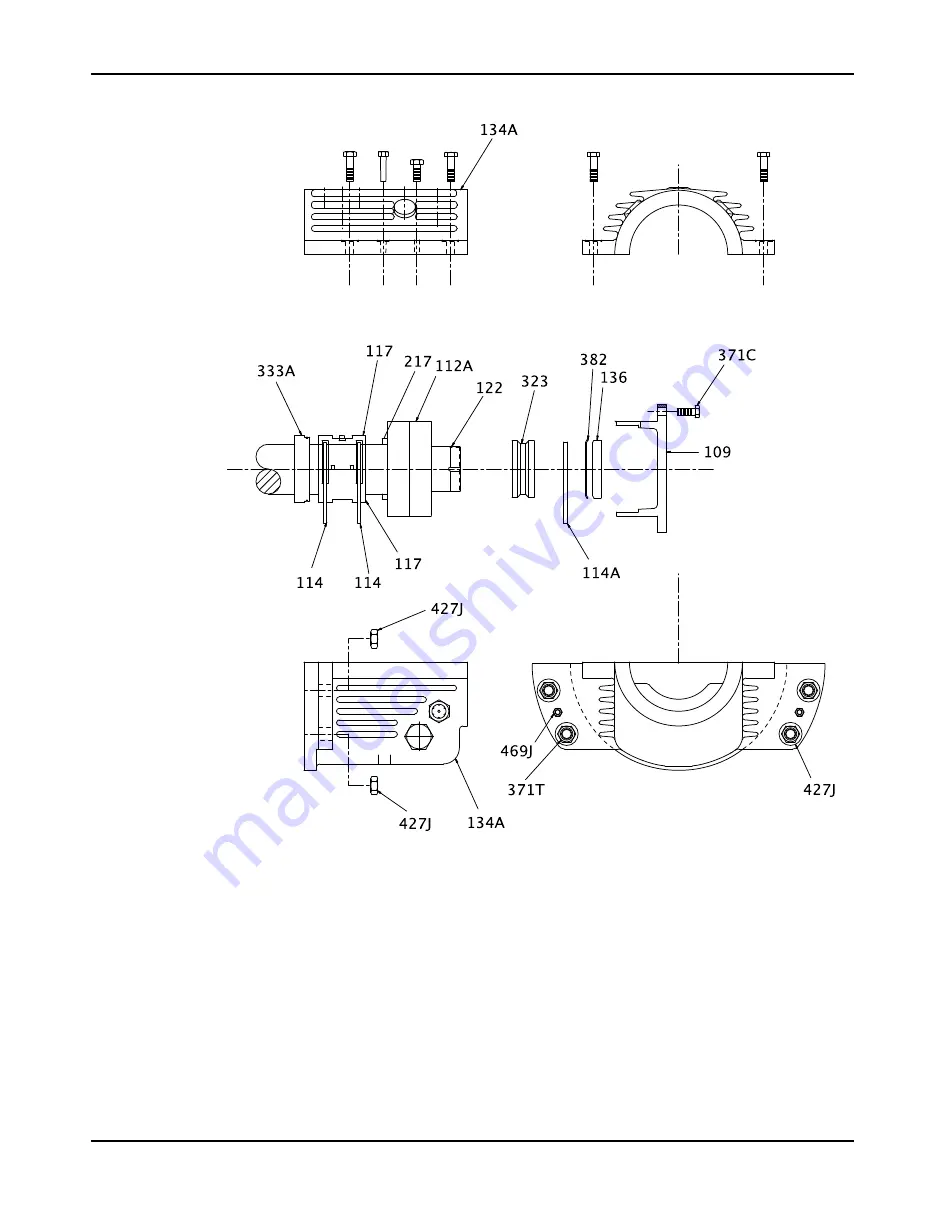
Maintenance
Disassemble the thrust end (sleeve/ball bearing pumps)
1. Remove the outboard end cover (109) by removing the end cover bolts (371C).
2. Remove the upper half of the bearing housing (134A) from the lower half:
a) Remove the dowel pins between the upper and lower halves of the bearing housing
(134A).
b) Remove the hex head screws that connect the upper and lower halves of the bearing
housing (134A).
c) Tighten the jackscrews in order to separate the housing halves.
68
Model 3610, API Type BB1 API 610 11th Edition Installation, Operation, and Maintenance Manual