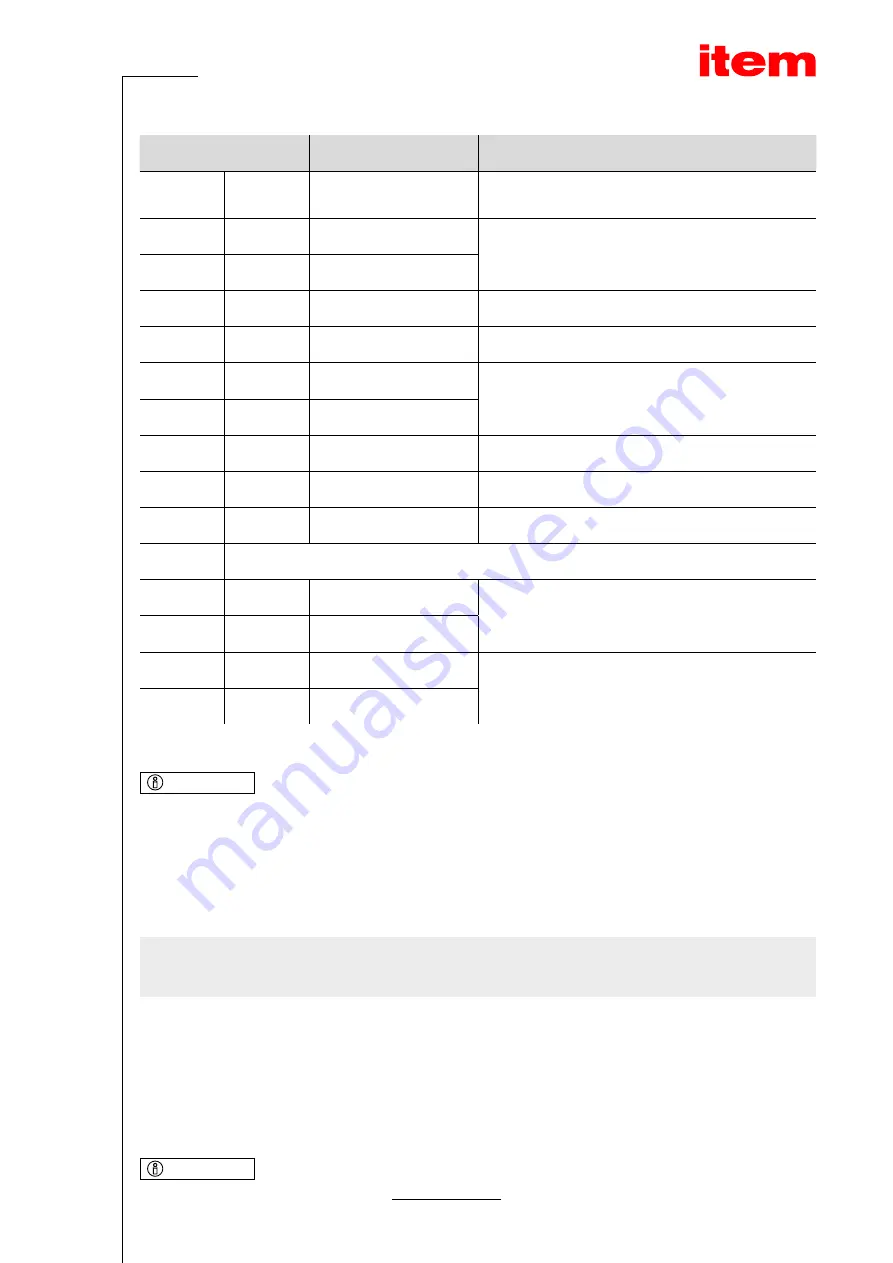
63
item Controller BL 1-04 /C
― Product manual
Pin
Name
Specification
1
MT+
Motor temperature sensor, normally closed contact, PTC,
NTC, KTY
9
Sensor cables for the encoder supply. In case of a long
cable, connect to US/GND at the motor end.
2
U_SENS-
10
US
Operating voltage for incremental encoders
3
GND
Associated reference potential
11
N / U
a0
Index pulse RS422 (differential) of the digital incremental
encoder
4
#N / Ū
a0
12
H_U
Phase U of the Hall sensor for commutation
5
H_V
Phase V of the Hall sensor for commutation
13
H_W
Phase W of the Hall sensor for commutation
6
14
A / Ū
a1
A track signal RS422 (differential) of the digital incremental
encoder
7
#A / U
a1
15
B / U
a2
B track signal RS422 (differential) of the digital incremental
encoder
8
#B / Ū
a2
INFO
Avoiding EMC interferences
The outer cable shield must be connected to the housing of the angle encoder connector with the greatest possible surface
area (with low impedance).
Cable type and configuration [X2B]
We recommend a minimum cross-section of 0.25 mm² for the angle encoder supply US and GND.
9.7 Connector: USB [X19]
The BL 1-04 /C servo drive has a Type B USB connector.
The correct operation requires a short USB cable (< 3 m) and the correct installation and earthing of the servo drive. If
excessive malfunctions/faults lead to communication problems (frozen communication), the USB connector can be briefly
disconnected to restart the communication.
In addition, we recommend using certified, double-shielded cables of the AB type (USB
2.0 connecting cable, type A connector to type B connector) AWG28-1P, AWG24-2C with shielded connectors.
INFO
Non-EMC-compliant wiring of the servo drive and motor