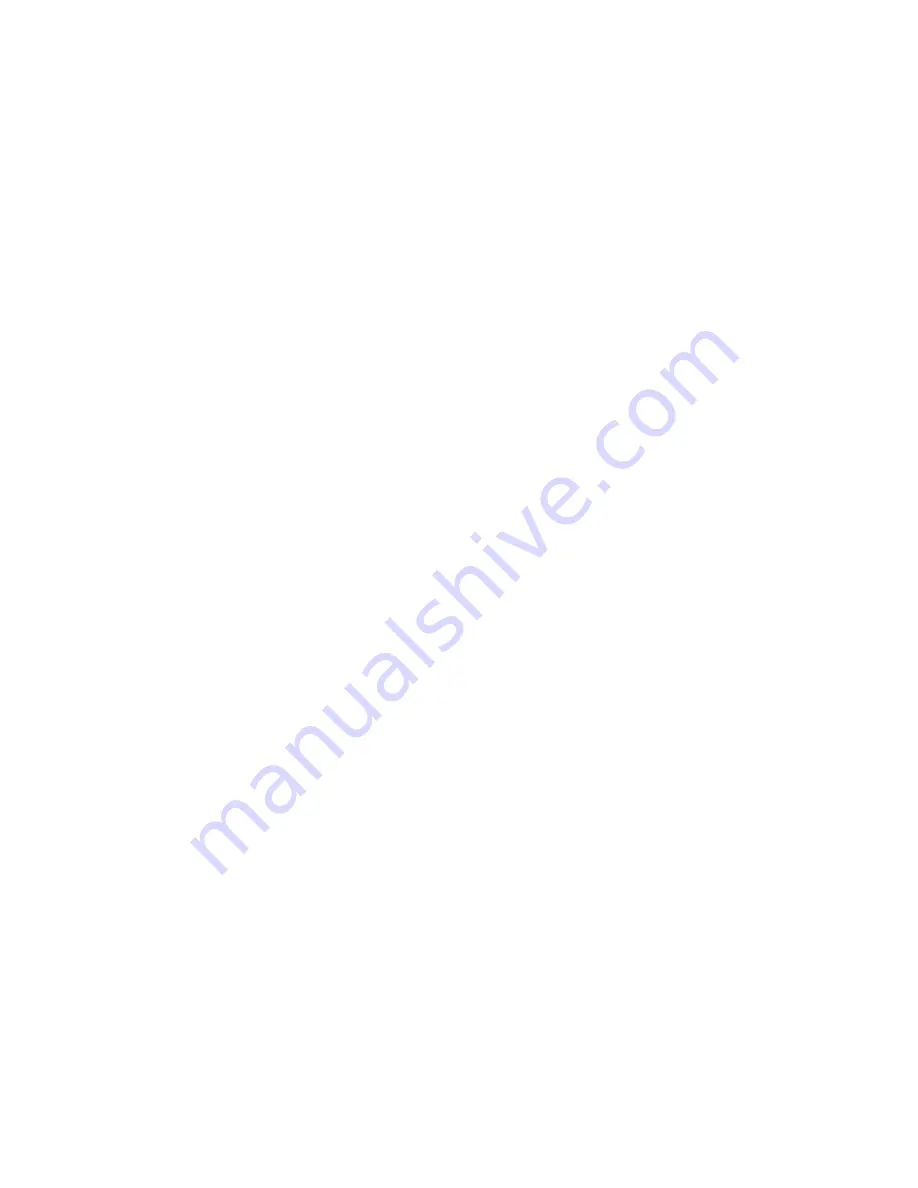
Tool operation (con't.)
· Always be aware that misuse and/or improper handling of this tool can cause injury to
yourself and other.
· Never clamp or tape the trigger or contact trip in an actuated position.
· Never leave a tool unattended with the air hose attached.
· Do not operate this tool if it does not contain a legible warning label.
· Do not continue to use a tool that leaks air or does not function properly. Take the
tool to a qualified service technician for proper servicing.
MAINTENANCE
Caution:
· Use caution when working with the spring assembly. The spring is wrapped around, but
not attached to, a roller. If the spring is extended beyond its length, the end will come
off of the roller and the spring will roll up with a snap, with a chance of pinching your hand.
Also, the edges of the spring are very thin and can cut. Care must also be taken to ensure
no permanent kinks are put in the spring, as this will reduce the spring's force.
· Do not use modified replacement parts or parts which will not give equivalent performance
to the original equipment.
Assembly procedure for seals
When repairing a tool, make sure the internal parts are clean and lubricated. Coat each
O-ring with O-ring lubricant before assembling. Use a small amount of oil on all moving
surfaces and pivots. After reassembly, add a few drops of air tool oil through the air line
fitting before testing.
Air supply pressure and volume
Air volume is as important as air pressure. The air volume supplied to the tool may be
inadequate because of undersized fittings and hoses, or from the effects of dirt and water
in the system. Restricted air flow will prevent the tool from receiving an adequate volume
of air, even though the pressure reading is high. The results will be slow operation,
misfeeds, or reduced driving power. Before evaluating tool problems for these symptoms,
trace the air supply from the tool to the supply source for restrictive connectors, swivel
fittings, low points containing water, and anything else that would prevent full volume
flow of air to the tool.
To replace piston
1) Insert the flats on the lower end of the driver piston stem carefully into the end of a
piston/plunger wrench.
2) Using another piston/plunger wrench, or another wrench of the proper size, unscrew
the plunger from the upper end of the stem. After this is done, it will be possible to lift
the poppet off the stem.
3) Place the piston/plunger wrench down over the piston stem onto the driver piston,
locking the piston ears in the slots in the wrench. Unscrew the piston from the stem.
To replace driver
1) It is not necessary to disassemble the piston-poppet-driver assembly to replace the
driver. Pull the poppet up on the driver piston stem as far as it will go.
2) Insert the piston/plunger wrench over the driver piston, locking the piston ears in the
slots in the wrench. Unscrew the piston from the threaded portion of the stem.
Page 5