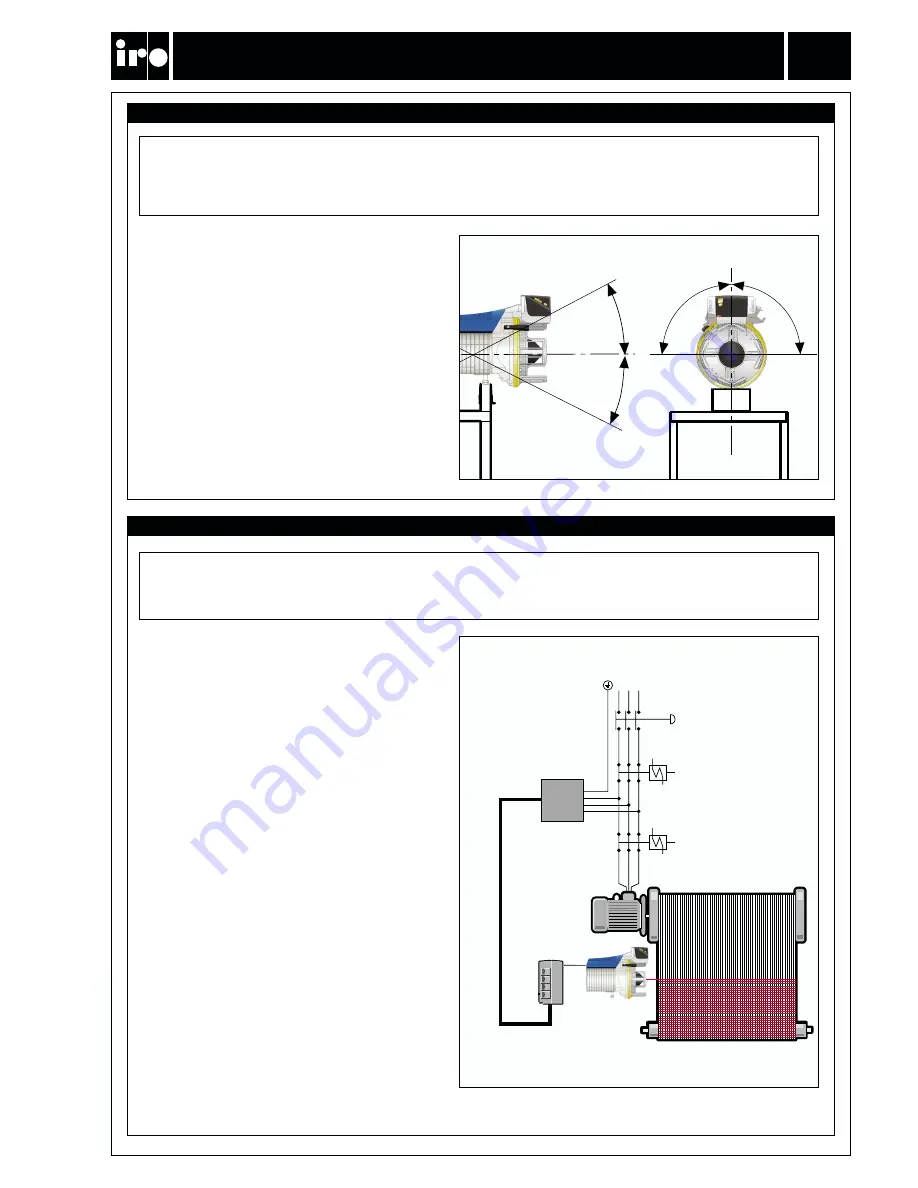
3
Ref. No. 31-8931-0201-06/0536
1131 CAN plus
Installation/ Mains Connection
L2
L1
L3
PE
Feeders must be mounted within 40° of the
horizontal plane.
40°
40°
90°
90°
IMPORTANT!
Turn off the main switch before any work is carried out on the electrical circuit.
Mains supply
Main switch
Emergency stop
Installation
Mains connection
The power supply to the feeder must not be
disrupted when the weaving machine stops.
NOTE
Condensation can form on the weft feeder when it is moved from the cold environment of the warehouse
to the warmer environment of the loom room. Make sure that the feeder is dry before switching it on.
Power supply