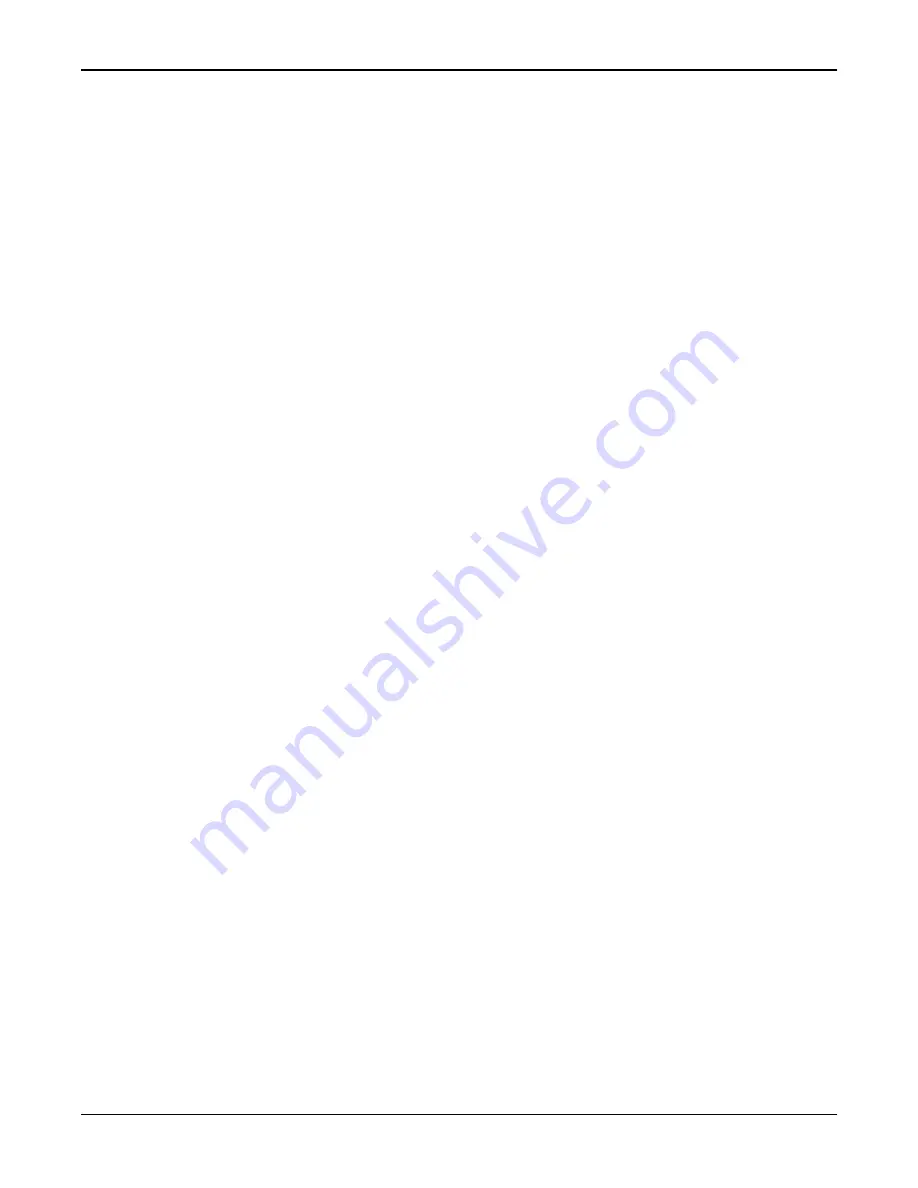
IRIS MODEL P522 APPLICATION MANUAL
Page 29
function is to use an auxiliary timer, so that a time
out of both the PLC and the auxiliary timer is re-
quired before light off (AND relationship).
The wiring diagram in Figure 10 shows a basic ig-
niter/burner circuit that can be used with a PLC to
accomplish the safe operation of a burner or burners in
a multiburner installation. Note that the burner shut-
down (BURNER STOP SW) is included; this circuit
is equally as critical as flame monitor protection.
BASIC BURNER START CIRCUIT
The sequence of operations for the basic burner start
circuit is as follows (refer to Figure 12):
1. Pressing the start button (START P.B.)
will start the ignition sequence, provid-
ing there is no MFT present, purge is
complete and all the limits for firing are
satisfactory, and no flame is being de-
tected. This latter function is the “safe-
start-check” jargon common in the flame
safeguard industry. Note that the PLC is
started at the same time as time delay 1
(TD1) is pulsed ON. (The push-button
switch must be actuated for at least 50
milliseconds to ensure the Delay After
De-Energized (DADE) timer is started.)
2. The master relay (RM) Contact pulls in,
sealing the loop around the flame relay
(RF) contact, normally closed. The RM
contact provides the current path to the
ignition transformer and igniter valve.
Note that the igniter valve contact from
the PLC must be commanded closed at
this time. A master relay is used so that
there is adequate current-carrying capac-
ity, which may not be the case for using
the flame relay contacts by themselves.
(The P522 flame relay contacts are rated
to 2 Amps at 220 VAC.) Alternatively,
additional, normally-open RM contacts
can be used, either in series or parallel,
to accommodate the load requirement
(sometimes, two contacts in series are
used to minimize contact wear caused by
inductive arcing when contacts are open).
3. The DADE timer will time-out, opening
the contact around the RF contact. If
there is no flame detected, the RM will
drop out, shutting down the sequence.
4. Once flame is detected, the PLC logic se-
quence can continue by opening the
burner valve, and then after a time delay,
closing the igniter valve (this is called
“interrupted igniter operation). The only
necessary requirement is that the burner
valve(s) be powered by RM contact(s),
as shown. A subsequent flame failure
will cause the RM to drop out, de-ener-
gizing the main fuel valve(s), regardless
of the state of the PLC.
This wiring diagram is not intended to illustrate all
the logic that would normally be used in a
multiburner system, but to show only the bare es-
sentials required to make the PLC safe. Such func-
tions as low-fire permissive on first burner started,
flameout alarm and reset, main burner time trial for
ignition, and igniter shutdown, would be part of the
PLC logic.
Occasionally, it is necessary to use two viewing
heads –one for the igniter and one for the burner–
with one signal processor. In this case, you can
switch between them (using one head at a time): the
igniter viewing head when proving igniter flame, and
the burner viewing head for proving main flame (re-
fer to section MULTIPLE VIEWING HEADS).
A safe-start-check would have to be made on both
viewing heads; you do not want to start up a burner
if it is already reading other flames. You can do this
by looking at both flame monitors in parallel (switch
both inputs together by connecting together the SIG
terminals of each viewing head, and the SIG GND
terminals of each viewing head) before starting the
ignition sequence. This will result in the normally-
closed RF contact on the P522 having to be closed
in order to start the burner. This parallel viewing
head operation should only be used for the start-up
sequence, because adding the flame signals together
increases the unwanted background that results in
poor discrimination.