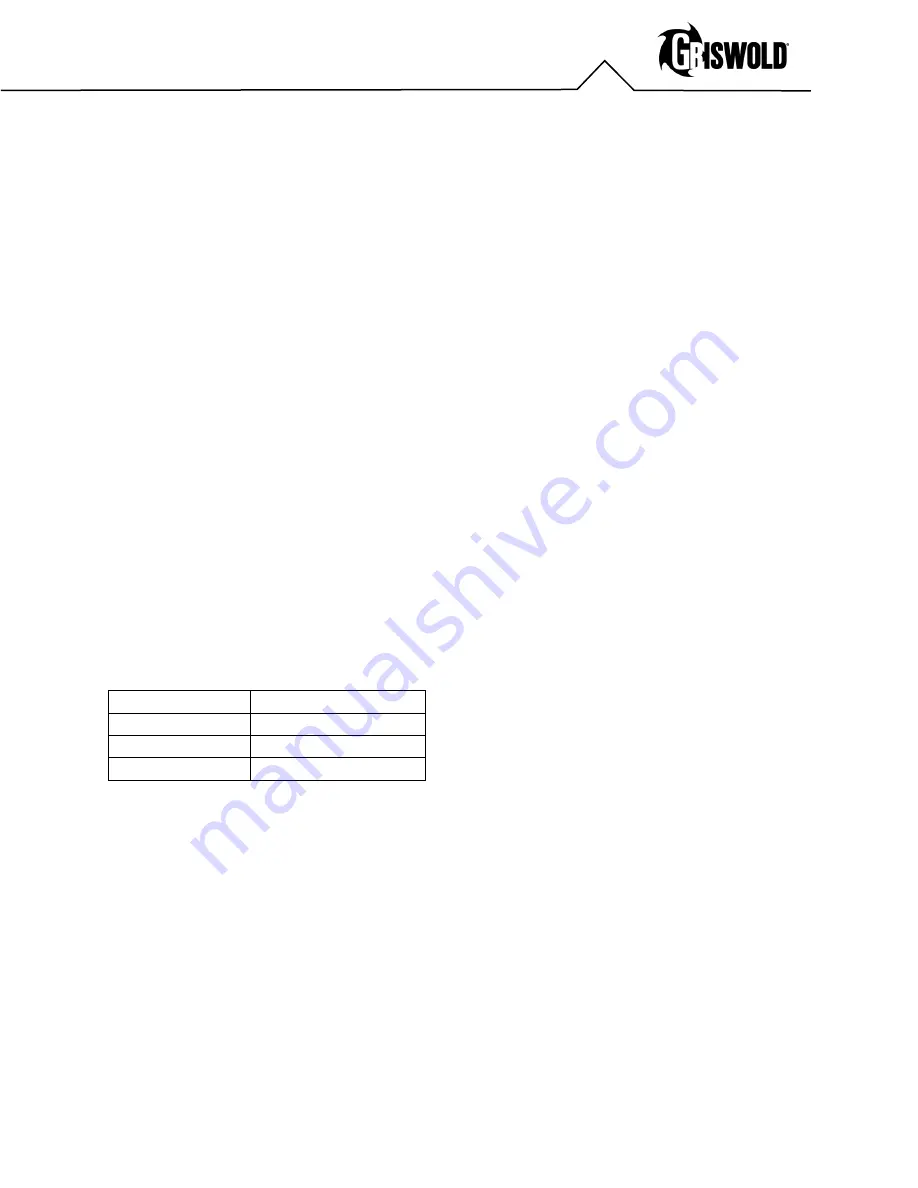
GRS-17000-E-01
850 SERIES
maximum allowable working pressure
(MAWP)
•
Do not allow the pump the be subjected to
temperatures greater than the maximum
allowable working temperature (MAWT)
•
If altering the pump flowrate by increasing
system resistance (e.g. by adjusting a
valve), always throttle the flow on the
discharge side of the pump. Throttling on the
suction side of the pump will decrease the
NPSHa for the pump and can cause pump
damage.
•
Do not overload the driver, which can
damage the driver and create unexpected
heat generation. A common scenario is
excessive power draw due to a change in
the system which allows the pump flowrate
to exceed the rated conditions
•
Do not operate the pump with a flowrate less
than the indicated minimum flowrate
•
Do not subject the pump to freezing
conditions. Freezing may damage the
components, leading to possible injury or
flooding.
MAINTENANCE
Bolt Torques
Recommended bolt torques for both hex head
and socket head cap screws
Screw Size
Recommended Torque
3/8 - 16 UNC
35 ft-lbs
1/2 - 13 UNC
85 ft-lbs
5/8
–
11 UNC
165 ft-lbs
Disassembly to Replace Mechanical Seal
•
Disconnect and lock out power to the driver
•
Close necessary valves and drain the pump
•
Flush the pump if necessary
•
Remove the case bolts and separate the
case and bracket. Since the pump is of a
back pull-out design, the pump back-end
(with the bracket) can be pulled from the
case while leaving the case bolted to the
piping. Alternatively, case can simply be
removed from the bracket and set aside
(e.g. if the pump is being disassembled on a
work bench).
•
Remove old O-ring and discard
•
Holding the impeller stationary, remove the
impeller screw and impeller washer
•
Remove the impeller
•
If present, remove the impeller spacer
•
Remove the mechanical seal spring
•
Remove the bracket. The rotating seal will
slide off during this process.
•
Push stationary seal assembly out of
bracket
Installing Mechanical Seal
•
Inspect shaft sleeve. If the outer surface is
damage, it may create a leak path under the
new rotating seal. Replace if necessary
•
If replacing sleeve, discard existing sleeve
O-ring(s). Clean shaft and apply a thin film
of assembly oil / grease. Install new sleeve
with new O-ring(s). If the sleeve has a
rectangular notch, align the notch with the
shaft keyway
•
Clean the seal bore of the bracket
•
Carefully press the new stationary seal
assembly into the bracket bore. Be careful
not to chip or damage the brittle seal face. It
is recommended to cover the seal face with
a softer material (e.g. cardboard, plastic)
during this process
•
Reinstall the bracket to the motor, taking
great care not to damage the stationary
mechanical seal face by letting it come into
contact with the motor shaft
•
Apply a thin film of assembly oil / grease to
the inner diameter of the rotating seal and
the outer diameter of the shaft sleeve and
install the rotating seal assembly onto the
sleeve, polished face first. Be sure that
enough oil / grease is present to allow the
seal to slide. Place the spring onto the back
of the rotating seal assembly and apply
pressure until the rotating mechanical seal
assembly slides to make contact with the
stationary seal face.
•
If applicable, install impeller spacer
•
Place impeller key into the shaft keyway and
slide it back
•
Apply a thin layer of assembly grease / oil to
the shaft and install impeller, pushing it back
(which will compress the mechanical seal
spring)