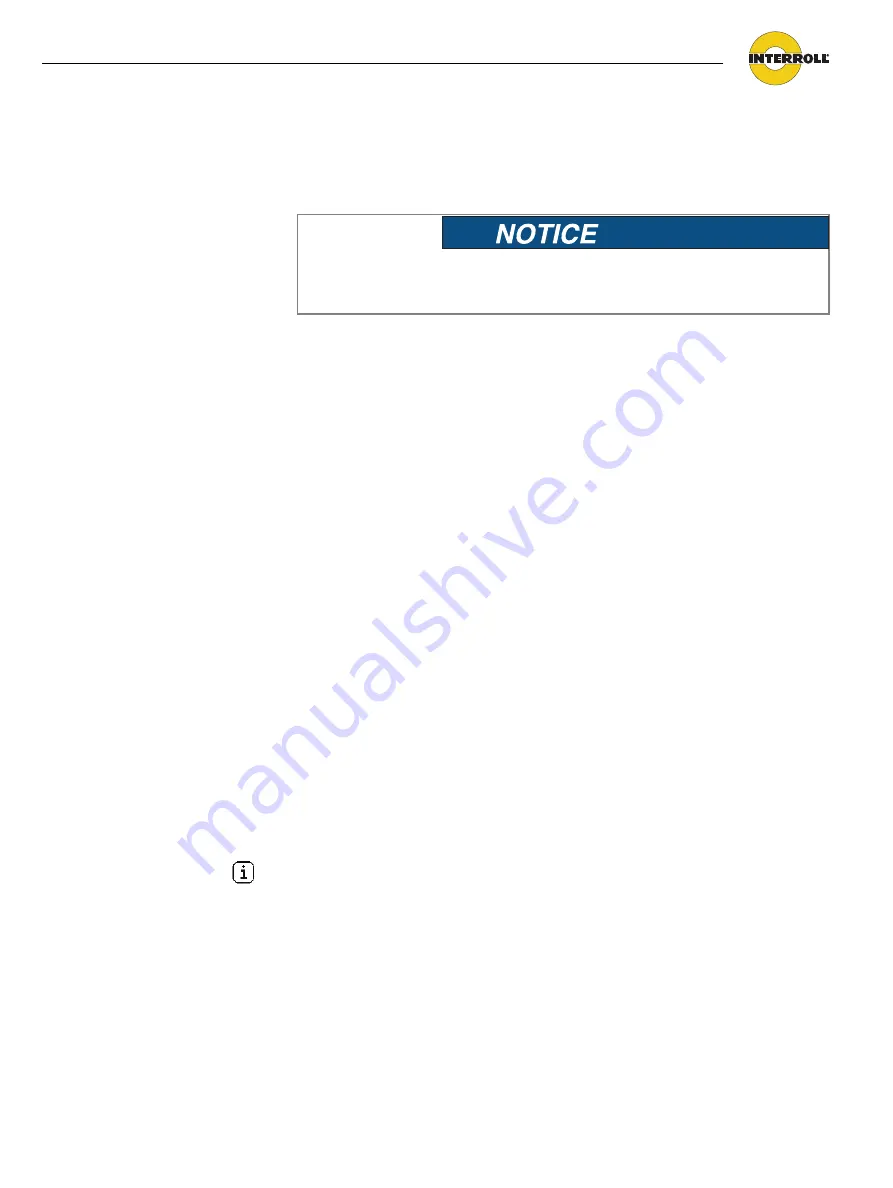
19
Version 1.0 (11/2007) en
Original language
RollerDrive EC200
Assembly
Warning notices concerning the electrical installation
¾
The electrical installation may only be executed by qualified and authorized
persons.
¾
Disconnect the power before installing, removing or rewiring the RollerDrive.
¾
Do not apply AC current to the RollerDrive or DriveControl device at any time
as this will cause irreparable damage.
¾
Do not apply too much stress to the connector pins. Bending the wires at the
connector and forcing the star washer over them can cause damage to the
insulation of the wires, which could result in failure of the RollerDrive.
¾
Ensure that the RollerDrive, the DriveControl and the 24 VDC power source
are properly earthed through the frame or supporting structure in which the
RollerDrive and the DriveControl are installed. Failure to do so could cause
the buildup of static electricity or ground loops and can cause the motor or
DriveControl to malfunction or fail prematurely.
¾
Do not bend the motor cable at the motor shaft. Leave a minimum of 12 mm
(0.5 in) of excess cable for stress relief. (Minimum motor cable bend radius 5x
cable diameter.)
¾
Do not spin the RollerDrive manually, as this generates an induction voltage
which could damage the DriveControl.
Setting up a roller conveyor
A roller conveyor usually consists of conveyor zones. Each zone is composed of
one RollerDrive and several idler rollers which are driven by the RollerDrive. The
idler rollers can be linked using either flat belts, timing belts, O-ring belts, multi-
rib belts or roller chains. The number of idler rollers in each zone depends on the
application.
¾
Before installing the RollerDrive, define the position of the conveyor zone
within the conveyor and the position of the RollerDrive within the conveyor
zone.
Risk of damage to the motor and/or the wires of the
RollerDrive
¾
Observe the following notices.
Hint
Locate the RollerDrive near the center of the zone or the center of gravity of the
object being conveyed to improve the transmission of the force between
RollerDrive and goods.
Содержание RollerDrive EC200
Страница 1: ...User Manual Interroll RollerDrive EC200...