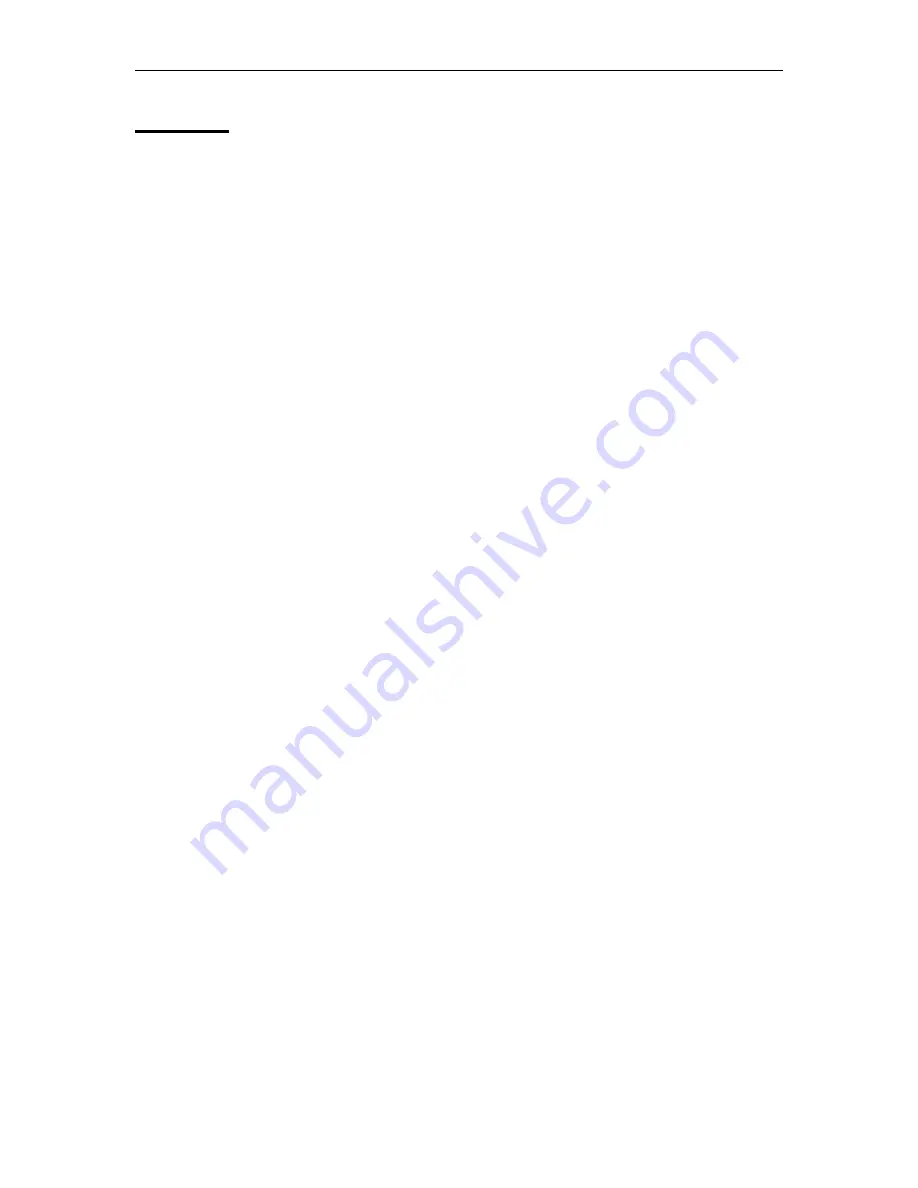
Jet Stream 500
7
Overview
The Jet Stream 500 is a complete wind tunnel package, engineered to study basic aerodynamic
principles of model aircraft wings, CO
2
cars along with other objects. The design is optimized to
instruct students in junior high, middle school, high school and university level classes with a focus
on ease of use. Since the wind tunnel is designed as a general instrument, the uses are limitless.
From airfoil to automobile or even rocket research, the learning value goes a long way.
Easy to Operate
The tunnel is controlled with an easy to use control panel. Starting the tunnel is as easy as entering
the desired air speed on the control panel. The LCD panel is continuously updated to accurately
reflect the system's wind velocity along with the forces generated on the test model. A one horse
power electric motor with a 10.5" propeller is powerful enough to produce winds of 80 miles per
hour in the test section. This is fast enough to test most any model. Instrumentation located in the
test area also monitors lift and drag forces exerted on the test model so forces can be displayed in
real time
on the display panel. Precision strain gages mounted under the test bed accurately
measure the forces on the model without having to attach them directly to the model. This allows
for easy mounting and unmounting of the test model. The lift over drag (L/D) ratio is also
computed and displayed on the display panel to demonstrate airfoil design efficiency.
Quality Design
The test area is free of turbulence due to following stringent wind tunnel design rules. By
extending the length of the tunnel and using a special flow straightener, the Jet Stream 500 has
virtually eliminated the test area turbulence, common in poorly designed tunnels. This allows the
instrumentation to
precisely
measure the forces within the tunnel to less than 0.5%. Wind velocity
is constantly monitored hundreds of times a second to maintain a steady flow over the test model.
Using a pitot static tube connected to a differential pressure transducer, the wind velocity is
electronically monitored and controlled. This provides a
constant
wind speed independent of the
size or angle of the test model. The actual wind velocity is displayed on the control panel which
allows studies to be conducted over a wide range of conditions.