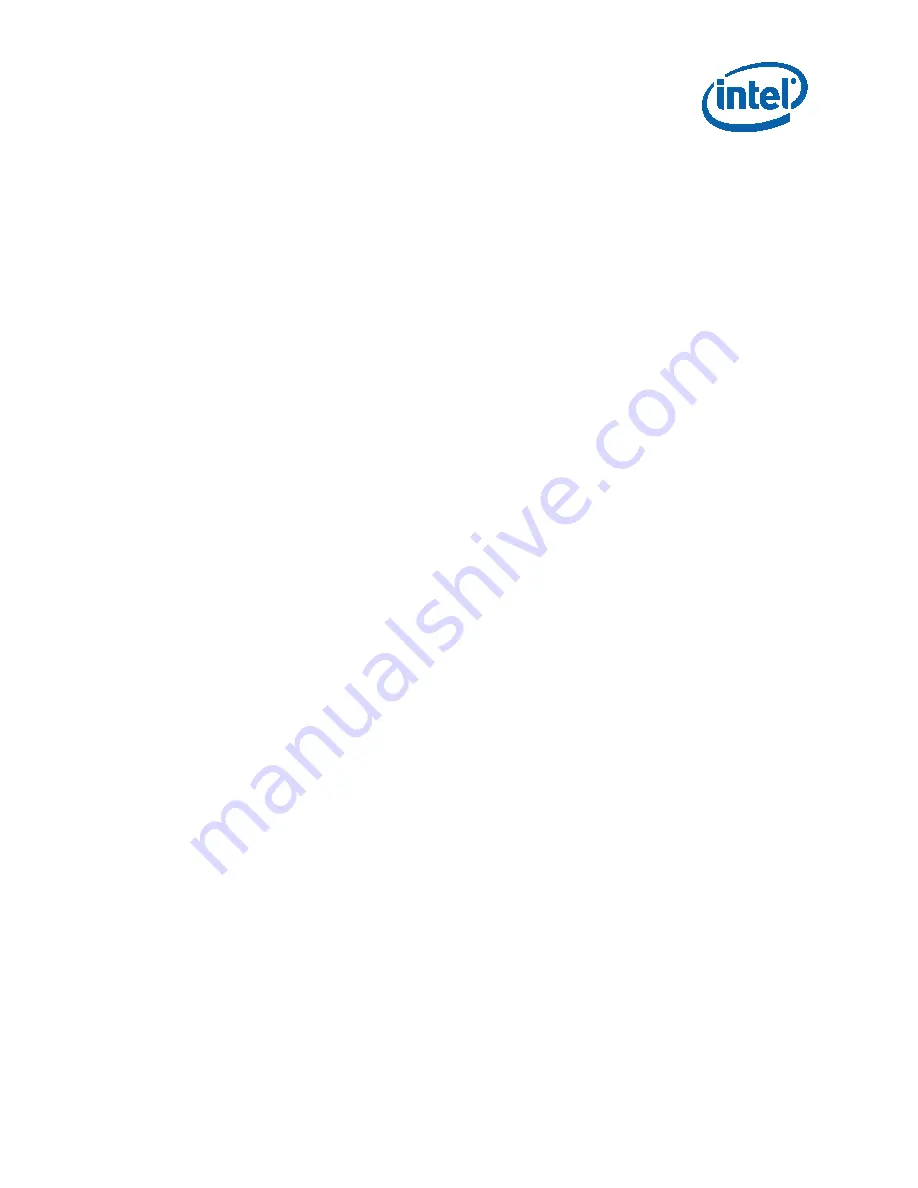
Processor Thermal/Mechanical Information
Thermal and Mechanical Design Guidelines
15
2.1.2
Heatsink Attach
2.1.2.1
General Guidelines
There are no features on the LGA775 socket to directly attach a heatsink: a
mechanism must be designed to attach the heatsink directly to the motherboard. In
addition to holding the heatsink in place on top of the IHS, this mechanism plays a
significant role in the robustness of the system in which it is implemented, in
particular:
•
Ensuring thermal performance of the thermal interface material (TIM) applied
between the IHS and the heatsink. TIMs based on phase change materials are
very sensitive to applied pressure: the higher the pressure, the better the initial
performance. TIMs such as thermal greases are not as sensitive to applied
pressure. Designs should consider a possible decrease in applied pressure over
time due to potential structural relaxation in retention components.
•
Ensuring system electrical, thermal, and structural integrity under shock and
vibration events. The mechanical requirements of the heatsink attach mechanism
depend on the mass of the heatsink and the level of shock and vibration that the
system must support. The overall structural design of the motherboard and the
system have to be considered when designing the heatsink attach mechanism.
Their design should provide a means for protecting LGA775 socket solder joints.
One of the strategies for mechanical protection of the socket is to use a preload
and high stiffness clip. This strategy is implemented by the reference design and
described in Section 6.7.
Note:
Package pull-out during mechanical shock and vibration is constrained by the LGA775
socket load plate (refer to the LGA775 Socket Mechanical Design Guide for further
information).
2.1.2.2
Heatsink Clip Load Requirement
The attach mechanism for the heatsink developed to support the processor should
create a static preload on the package between 18 lbf and 70 lbf throughout the life
of the product for designs compliant with the reference design assumptions:
•
72 mm x 72 mm mounting hole span for ATX (refer to Figure 7-40)
•
TMA preload versus stiffness for BTX within the limits shown on Figure 5-6
•
And no board stiffening device (backing plate, chassis attach, and so forth).
The minimum load is required to protect against fatigue failure of socket solder joint in
temperature cycling.
It is important to take into account potential load degradation from creep over time
when designing the clip and fastener to the required minimum load. This means that,
depending on clip stiffness, the initial preload at beginning of life of the product may
be significantly higher than the minimum preload that must be met throughout the life
of the product. For additional guidelines on mechanical design, in particular on designs
departing from the reference design assumptions refer to Appendix A.
For clip load metrology guidelines, refer to Appendix B.
Содержание AT80569PJ080N - Core 2 Quad 3 GHz Processor
Страница 24: ...Processor Thermal Mechanical Information 24 Thermal and Mechanical Design Guidelines...
Страница 80: ...Heatsink Clip Load Metrology 80 Thermal and Mechanical Design Guidelines...
Страница 82: ...Thermal Interface Management 82 Thermal and Mechanical Design Guidelines...
Страница 106: ...Balanced Technology Extended BTX System Thermal Considerations 106 Thermal and Mechanical Design Guidelines...
Страница 108: ...Fan Performance for Reference Design 108 Thermal and Mechanical Design Guidelines...
Страница 120: ...Mechanical Drawings 120 Thermal and Mechanical Design Guidelines Figure 7 50 Reference Fastener Sheet 1...
Страница 121: ...Mechanical Drawings Thermal and Mechanical Design Guidelines 121 Figure 7 51 Reference Fastener Sheet 2...
Страница 122: ...Mechanical Drawings 122 Thermal and Mechanical Design Guidelines Figure 7 52 Reference Fastener Sheet 3...
Страница 123: ...Mechanical Drawings Thermal and Mechanical Design Guidelines 123 Figure 7 53 Reference Fastener Sheet 4...