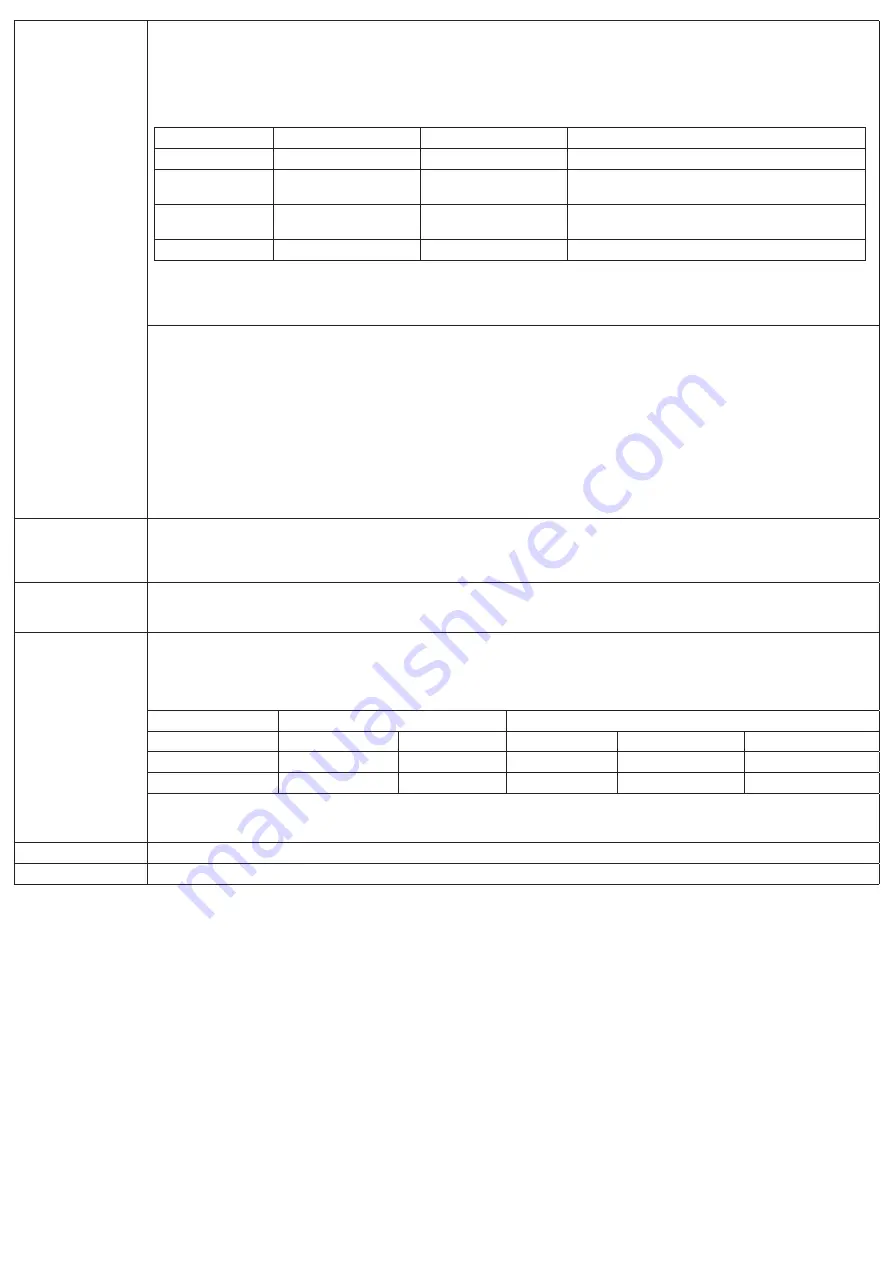
4 / 5
NT060US
Rev A - 2021-06 2027767-1
4) Cleaning,
disinfection and
drying
Cleaning: Automated:
Soak in lukewarm (less than 43°C), mild (pH 7.0 – 8.5), enzymatic detergent and deionized water for a
minimum of 5 minutes. For instruments with lumens and instruments equipped with cleaning ports, inject cleaning solution through the
instrument with an irrigation syringe and allow to soak for a minimum of 5 minutes. Use a soft instrument brush to scrub instruments
while submerged in cleaning solution to remove organic matter. Rinse with deionized water. Remove instruments and equipment
from any sterilization trays before placing into washer baskets. Orient devices following recommendations of washer/disinfector
manufacturers. Use alkaline or neutral pH detergent recommended by washer/disinfector or detergent manufacturers. These products
have been validated for effective cleaning using an automatic washer/disinfector cycle consisting of the following:
Phase
Recirculation Time
Water temperature
Detergent type
Pre-wash 1
5 minutes
20°C (68ºF)
N/A
Enzyme Wash
5 minutes
55°C (131ºF)
neutral pH enzymatic detergent
for example: Neodisher
®
MediClean forte
Wash 1
5 minutes
66°C (150.8ºF)
neutral pH enzymatic detergent
for example: Neodisher
®
MediClean forte
Rinse 1
5 minutes
70°C (158ºF)
N/A
Thoroughly examine instruments for any residual soil.
A rigid MIS (minimally invasive surgery) rack should be used to clean rigid MIS intruments and instruments with lumens to maximize
efficiency of cleaning. Suction ports and flush ports should be connected to the MIS Rack to allow a constant flow of solution inside
hard-to-reach areas of the instruments.
Cleaning: Manual:
Soak in lukewarm (less than 43 °C), mild (pH 7.0 – 8.5), enzymatic detergent and deionized water for a minimum
of 5 minutes. For instruments with lumens and instruments equipped with cleaning ports, inject cleaning solution through the instrument
with an irrigation syringe and allow to soak for a minimum of 5 minutes. Use a soft instrument brush to scrub instruments while
submerged in cleaning solution to remove organic matter. During brushing, actuate any moveable mechanisms such as hinged joints,
box locks, or spring-loaded features to allow access to hard to reach areas. If the components of the instrument can be retracted,
retract or open the part while cleaning the area. Rinse with deionized water, then clean ultrasonically in a lukewarm (less than 43
°C), mild (pH 7.0 – 8.5) detergent and deionized water for 15 minutes. Rinse thoroughly with deionized water, utilizing a syringe to
thoroughly rinse cleaning solution from lumens and cleaning ports. During final rinsing, rinsing solution to inject into cleaning ports
should be of 60mL minimum. Clean in this manner until no visible soil remains on the instrument. Dry with compressed air or wipe
dry with a lint-free cloth. Examine instruments for any staining or deterioration, remove from use as appropriate. Note: When using
an ultrasonic cleaner or a spray washing machine, follow the manufacturer’s recommendations, particularly with regard to articulated
instruments and positioning of instruments. Note: Additional cleaning methods may be warranted, including presoaking in 3% hydrogen
peroxide.
5) Maintenance,
inspection and
testing
Check the cleanliness and operation of the instrument. Clean again if debris is present and remove from use any damaged instrument.
Inspect components for any damage. If damage is observed, do not use the instrument until it is repaired. Following cleaning, lightly
lubricate instruments with movable parts. Use a lubricant intended for sterilizable instruments such as a water-soluble instrument milk.
Do not use silicone spray.
6) Packaging
A standard sterilization wrap may be used. In the US, an FDA cleared surgical wrap is required.
In sets: Instruments may be loaded into dedicated instrument trays or general purpose sterilization trays. Ensure that cutting edges are
protected. Wrap trays using appropriate method.
7) Sterilization
(Temperatures are
minimum required;
times are minimum
required)
The sterilization parameters given below should be used for devices that are fully disassembled when disassembly is possible. During
sterilization, do not mix instruments of different metals, to avoid electrolyte oxidation. Close instruments with catches and racks on
the first notch. Arrange the instruments in sterilization containers with perforations on the top and bottom and on supports such as
those used in microsurgery. Follow the appropriate cycle listed in the table below. All steam cycles have been validated in the wrapped
configuration and can be sterilized wrapped or unwrapped. These devices have only been validated for steam sterilization methods.
Instruments Only
Instruments Only or Instruments in Instrument Trays
Cycle
Gravity
Gravity
Pre-vac
Pre-vac (FR/WHO)
Pre-vac (U.K.)
Temperature
121 °C
132 °C
132 °C
134 °C
134 °C
Time
30 min
10 min
4 min
18 min
3 min
Drying:
Instruments Only and Aluminum/Stainless Steel Instrument Trays : 15 to 30 minutes and visual inspection for dryness.
Polymer-based (plastic) Instrument Trays: Minimum drying time 40 minutes and visual inspection for dryness
8) Storage
Store instruments in a clean, dry area.
9) Disposal
Instruments must be disposed of in accordance with applicable local regulations.
The instructions provided above have been validated by the manufacturer as being CAPABLE of preparing the product for re-use. They are not applicable to
single use devices or single use accessories, which must be destroyed after use in accordance with applicable local regulations. It remains the responsibility of
the processor to ensure that reprocessing is performed using validated equipment to achieve the desired result. This normally requires validation and routine
monitoring of the process. Some devices have specific assembly instructions. In this case, refer to the assembly insert provided with the device for additional
instructions. All validations performed per AAMI TIR12, (Designing, testing, and labeling reusable medical devices for reprocessing in health care facilities:
A guide for medical device manufacturers).
RETURNS
Contact Integra Customer Service to obtain a Return Goods Authorization number (RGA #) prior to shipping the product back to Integra. The RGA # should be
prominently displayed on the outside of the return packaging and included on all paperwork enclosed with the return. All product returned should be decontaminated
and cleaned, and all products should be safely packed in protective wrapping. Please have the original invoice number or purchase order number available to assist in
verifying warranty information.
LIMITED WARRANTY
A. This LIMITED WARRANTY provides assurance for the customer who purchases a Integra Product (hereinafter the “Product”) that should the Product fail to
function to Integra’s published specifications during the term of this LIMITED WARRANTY (one year from the date of shipment for new Product), Integra will
either replace, repair, or issue a credit (adjusted to reflect the age of the Product) for the Product or any portion thereof. This LIMITED WARRANTY is extended
only to the buyer purchasing the Product directly from Integra or from its affiliate or its authorized distributor or representative.
B. To qualify for this LIMITED WARRANTY, the following conditions must be met:
(1) The Product must be used on or before its “Use By” or “Use Before” date, if applicable.
(2) The Product must be used in accordance with its labeling and may not be altered or subjected to misuse, abuse, accident or improper handling.
(3) Integra must be notified in writing within thirty (30) days following discovery of a defect.
(4) The Product must be returned to Integra within thirty (30) days of Integra receiving notice as provided for in (3) above.