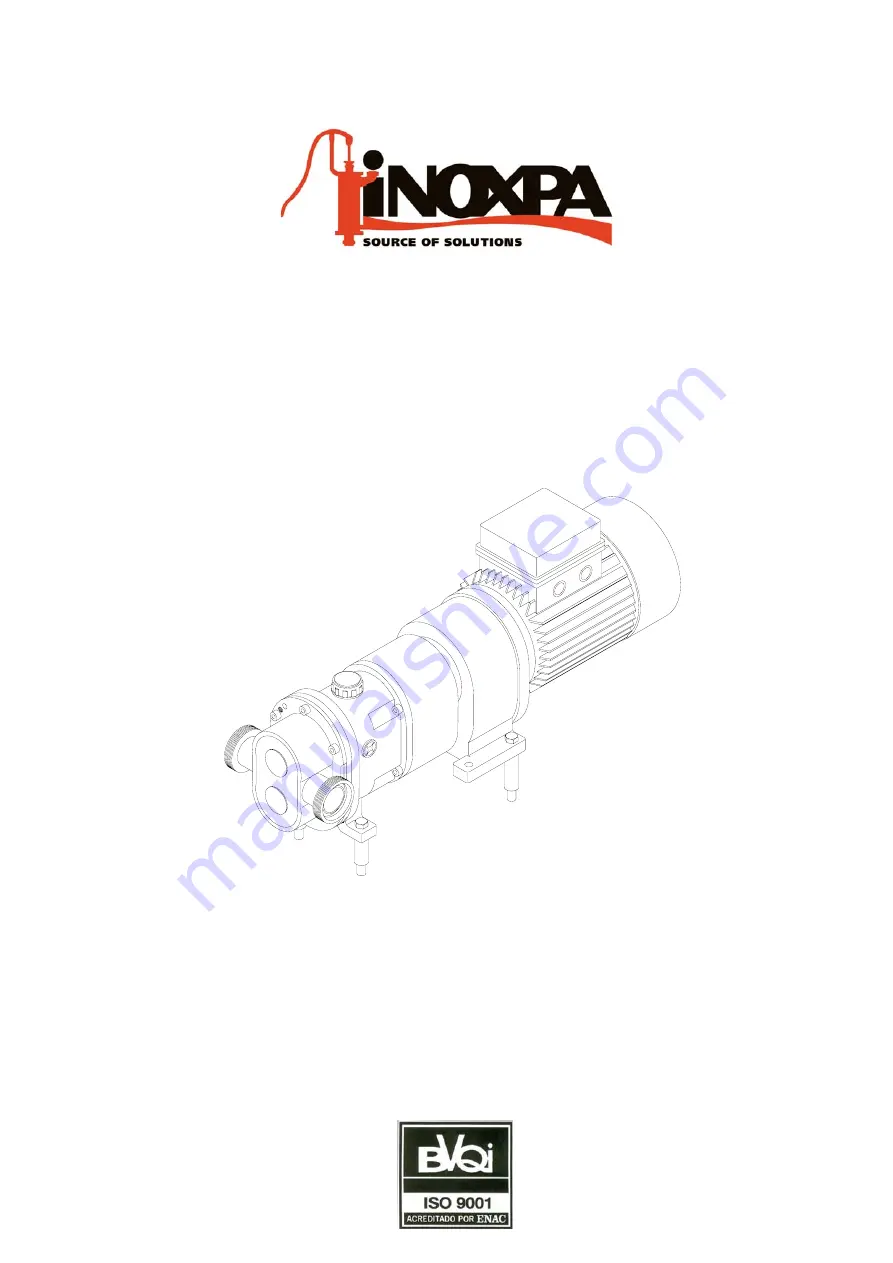
INSTALLATION, SERVICE AND
MAINTENANCE INSTRUCTIONS
TLS LOBE PUMP
INOXPA, S.A.
c/Telers, 54 Aptdo. 174
E-17820 Banyoles
Girona (Spain)
Tel. : (34) 972 - 57 52 00
Fax. : (34) 972 - 57 55 02
Email: [email protected]
www.inoxpa.com
Содержание TLS 1-25
Страница 33: ...9 TLS Technical Information 9 6 ED 17 10 00 TLS 1 25 1 40 Parts Diagram...
Страница 35: ...9 TLS Technical Information 9 8 ED 17 10 00 TLS 2 40 2 50 Parts Diagram...
Страница 37: ...9 TLS Technical Information 9 10 ED 17 10 00 TLS 3 50 3 80 Parts Diagram...
Страница 39: ...9 TLS Technical Information 9 12 ED 17 10 00 TLS 3 51 3 81 Parts Diagram...