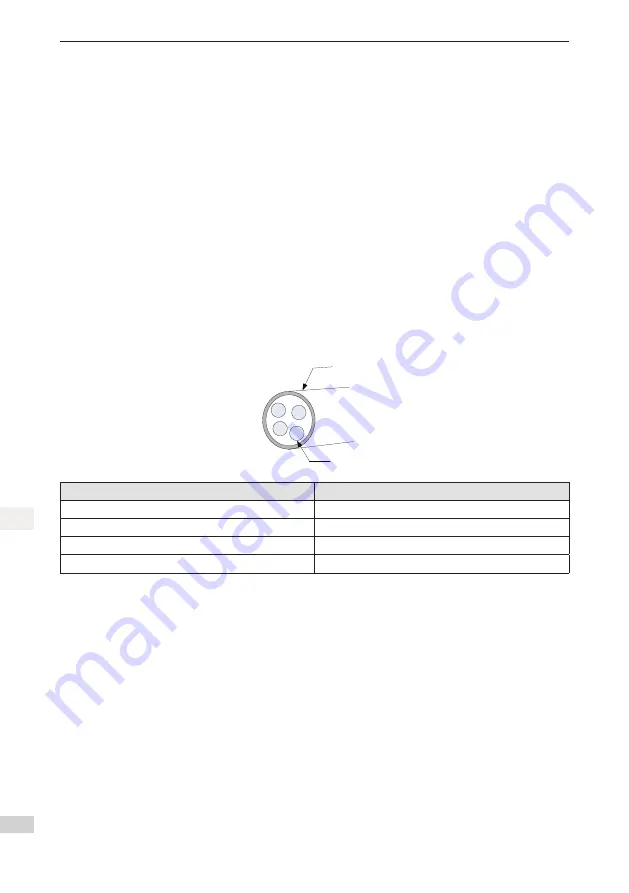
- 40 -
3 Wiring
3
3.1.5 Precautions for Main Circuit Wiring
1. Do not connect the input power cables to the output terminals U, V and W. Failure to comply will cause
damage to the servo drive.
2.
When cables are bundled in a duct, take current reduction into consideration since the heat dissipation
condition deteriorates.
3. When temperature inside the cabinet is higher than the temperature limit of the cables, select those
cables with a higher temperature limit. Teflon cables are recommended. As the surface of general ca
-
bles is easy to harden and break, take thermal insulation measures for cables laid in a low temperature
environment.
4. The bending radius of a cable shall exceed 10 times that of its outer diameter to prevent the internal wire
core from breaking due to long time bending.
5. Select and use cables with rated voltage of 600 V AC (and above) and temperature of 75
℃
(and above).
Under the ambient temperature of 30
℃
and normal heat dissipation conditions, the allowable current
density of the cables shall not exceed 8 A/mm
2
when the total current is below 50 A, or 5 A/mm
2
when the
total current is above 50 A. This value can be adjusted when the ambient temperature is high or when the
cables are bundled. The allowable current density (A/mm
2
) is calculated as follow:
Allowable current density = 8 × reduction coefficient of current-carrying conductor density ×
current correction coefficient
Pipe
Cables
Number of Cables in the Same Duct
Current Reduction Coefficient
Less than 3 cores
0.7
4 cores
0.63
5–6 cores
0.56
7–15 cores
0.49
6. The bleeder resistor cannot be connected between DC bus terminals P and C. Failure to comply may
cause a fire.
7. Do not bundle power cables and signal cables together or run them through the same duct. Power and
signal cables shall be separated by at least 30 cm to prevent interference.
8. High voltage may still remain in the servo drive when the power supply is cut off. Do not touch the power
terminals within 5 minutes after powering off.
9. Do not frequently turn ON and OFF the power supply. If the power supply needs to be switched on or off
repeatedly, make sure that the time interval is at least one minute. As the servo drive contains a capac
-
itor in the power supply, a large charging current flows for 0.2 seconds when the power supply is turned
OFF. Frequently turning ON and OFF the power supply will deteriorate performance of the main circuit
components inside the servo drive.
10. Use a grounding cable with the same cross-sectional area as the main circuit cable. If the cross-sectional
area of the main circuit cable is less than 1.6 mm
2
, use a grounding cable with a cross-sectional area
of 2.0 mm
2
.
11. Ground the servo drive to the earth reliably.
12.
Do not power on the servo drive if any cables become loose. Otherwise, a fire may occur.
Содержание SV820N Series
Страница 127: ...126 6 Trial Running 6 6 5 6 PLC Program 1 Add an FB file that edits the function block in the application...
Страница 128: ...127 6 Trial Running 6 2 The definition part of FB 3 Five function blocks in FB...
Страница 141: ...140 6 Trial Running 6 In section0 call the function block then the axis can be moved by the bus...
Страница 143: ...142 6 Trial Running 6 3 Open Visual studio and create a New Twincat3 Project...
Страница 146: ...145 6 Trial Running 6 Click OK Click OK...
Страница 147: ...146 6 Trial Running 6 Click Yes Click OK...
Страница 149: ...148 6 Trial Running 6 C The default RPDO list is as follows...
Страница 150: ...149 6 Trial Running 6...
Страница 152: ...151 6 Trial Running 6 7 Activate the configuration and switch over to the running mode Click...
Страница 157: ...156 6 Trial Running 6 Add a motion control library making it easy to call the control function block...
Страница 158: ...157 6 Trial Running 6 Create a new POU...
Страница 159: ...158 6 Trial Running 6 Create a new FB add MC_power MC_jog MC_home MC_absolute MC_reset to FB...
Страница 160: ...159 6 Trial Running 6 Call axis_motion in main Call the program in PLCTASK...
Страница 161: ...160 6 Trial Running 6 Compile the program if there is no fault configuration can be activated and then log in to the PLC...
Страница 181: ...Revision History Date Revised Version Revised Details May 2017 A00 First release...