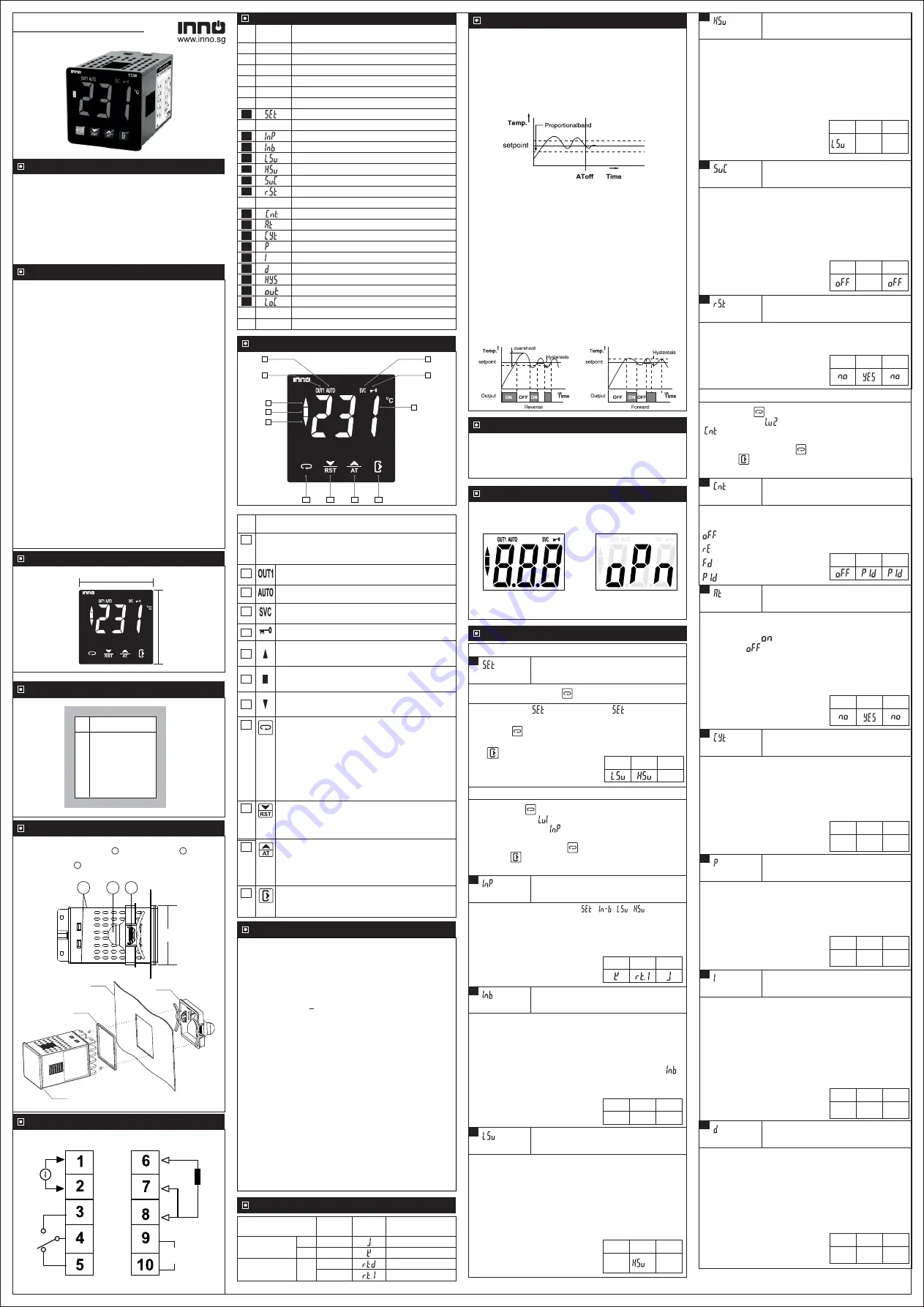
12
Up / AT Key :
Used in Program mode to increment parameter
value.
auto-tuning.
Touch & hold this key for 2 seconds to start or stop
11
Exit Key :
Press this key to save the setting value and to exit
the programing mode.
9
Press & hold this key atleast 8 seconds to enter
in Level2.
Press & hold this key atleast 1 seconds to enter
in set point mode.
Press & hold this key atleast 4 seconds to enter
in Level1.
Next key :
Used to enters parameters level, moves to next
parameters.
10
value.
Down / Reset Key :
Used in Program mode to decrement parameter
Used to Reset SVC time.
Sr.
No.
Description
Turns ON while control output is ON.
Turns ON when auto tunning is in progress.
4
5
Turns ON when keypad is locked.
3
6
Turns ON when service time elapsed.
O
Turns ON when the process value is > 5 C than set
point.
O
Turns ON when the process value is within the 5 C
range of the set point.
O
Turns ON when the process value is < 5 C than set
point.
8
7
2
RUN mode : Displays current measured value.
Process Value
SETTING mode : Displays parameter.
1
Input types & Input range
Input Type
Thermocouple
J
K
1
Decimal
Point
1
Display
O
Input Range ( C)
O
-50 to 750 C
O
-50 to 999 C
RTD
Pt
100
1
0.1
O
-99 to 400 C
O
-9.9 to 99.9 C
Operating Manual
Introduction
Caution for your safety
Notice:
The information in this document is
subject
to change in
order to improve reliability , design or function without prior notice
and does not represent
a commitment on the part of the company.
In no
event will the company be liable for direct, indirect, special,
incidental or consequential damage arising out of the use or
inability to use the product or documentation, even if advised of
the possibility of such damages. No part of this manual may be
reproduced or transmitted in any form or by any means without
the prior written permission of the company.
Probe :
To give a correct reading, the probe must be installed
in a place protected from thermal influences, which may
affect the temperature to be controlled.
WIRING:
The probe and its corresponding wires should
never be
installed in a conduit next to control or power
supply lines. The
electrical wiring should be done as shown in the diagram. The
power supply circuit should be connected to a protection switch.
The terminals admit wires of upto 2.5sq mm.
WARNING:
Improper wiring may cause irreparable damage and
personal injury. Kindly ensure that wiring is done by qualified
personnel only.
Controller:
Controller should be installed in a place
protected by vibration, water and corrosive gasses and
where ambient temperature does not exceed the values
specified in the technical data.
Maintenance:
Cleaning: Clean the surface of the controller with a
soft moist cloth. Do not use abrasive detergents, petrol, alcohol or
solvents.
Product Mounting
Installation :
Fixing and dimensions of panel models:
To fix the unit, slide the fastener 1 through the guides 2 as per the
position shown in the figure. Move the fastener in the direction of the
arrow, pressing tab 3 it permits to move the fastener in the opposite
direction of the arrow.
45.5mm
45.5mm
Panel Cutout
Dimensions
Connection Diagram
When power is supplied, whole display part will be flash for
6 sec and then enters in to RUN mode.
1. Whole display Part
2. Second Screen
Initial Display when Power is ON
Technical Specification
Display :
3 X 20mm 7 segment White display,
O
1 C for Thermocouple (J, K) input
85 to 265 VAC/DC on request.
Mounting
:
Flush panel mounting with fasteners
Protection
:
IP65 Front
<
2.5sq mm terminal only.
Data storage
:
Non-volatile flash memory
Storage temp :
-25°C to 60°C (non-condensing)
Power input
:
230 Vac ±15 % , 50-60Hz Standard.
Control output : Relay :
10A, 230V AC or
Connections
:
Terminal connectors.
SSR (field selectable) : 10V DC, 30mA
Thermocouple : J, K
Input Type
:
RTD : Pt100
O
O
Resolution
:
0.1 C / 1 C for RTD (Pt100) input
Dimensions
:
Frontal : 48 X 48mm, Depth : 78mm
O
Display Accuracy:
RTD : 0.1% of F.S +/- 1 C
Housing
:
Polycarbonate Plastic
Panel Cutout
:
45.5 X 45.5mm
7 Iconic LEDs for Indication
Operating temp. :
0°C to 60°C (non-condensing)
Operating humidity :
20% to 85% (non-condensing)
Thermocouple : 0.3% of F.S
Sampling Period :
1 second
(20 min of settling time for TC)
Parameter Setting Mode
Function: Sets the upper limit of PV input.
5
Parameter
Function: Sets the lower limit of PV input.
4
Parameter
For J type sensor
For J type sensor
Display will show . User can change value using UP/
DOWN keys. Holding the key, will change the value at a faster
rate. Press key to store the desired value & move on to
the next parameter. Set value also can be stored by pressing
Key
Function: To set control set point.
1
Parameter
Press & hold key for 1 seconds.
SP Setting
6
Parameter
Function : To set service time.
Example:
If user set Service time to 10 days, then after 10
days of continuous service of machine, the SVC icon on
controller will lit to indicate that service time has been elapsed
or its time to service the machine
Service Time notify the machine user to carry out the machine
maintenance setted at predefined time or to indicate that, the
machine has worked for certain days.
Min
Max
Fac.
999
Day
Function: Sets input correction.
3
Parameter
Min
Max
Fac.
In time it may be possible that the display may be offset by a
degree or so.
To compensate for this error, user may need to add or minus the
degrees required to achieve the correct temperature.
O
Example :
The temperature on the display is 28 C, whereas the
O
actual temperature is 30 C. User will have to set the " "
O
parameter to 2 C, which means that once out of the
O
programming mode, the temperature on display will be 30 C
O
O
(28 C+ 2 C).
O
-20 C
O
20 C
O
0 C
LEVEL1 Parameter
Function: Sets the type of input sensor .
2
Parameter
Min
Max
Fac.
For J type sensor
For type of input sensor & range please refer
"Input types &
Input range"
table.
8
9
10
11
12
Sets cycle time for PID action.
Sets proportional band.
Sets integration time.
Sets differential time.
Sets the
hysterisis.
Runs auto tuning.
Set control action for relay / SSR.
Index
Sr.
No.
Para.
Description
1
3
4
5
6
7
Control set point.
Sets the type of input sensor .
Sets input correction.
Sets the lower limit of PV input.
Sets the upper limit of PV input.
13
14
15
16
Factory reset parameter.
Level1 Parameter
Sets Control output.
Lock keypad.
2
LED Indications
User Interface
Technical Specification
Initial display when Power is ON
Parameter setting mode
Working
Level2 Parameter
Error Messages
Input types & Input range
Set service time.
Min
Max
Fac.
O
0 C
7
Parameter
Function : To restore default settings of
the controller.
When Set to Yes all parameter are programmed to factory
values.
Useful to debug setting related problems.
Min
Max
Fac.
Min
Max
Fac.
O
-50 C
Once set at a particular value, this will not allow the set point
to go above this value.
When changing the setting value and SV > HSV, SV is reset
as HSV.
Sets the maximum limit for set point adjustment. It can be
set from LSV+1 value to maximum specified range of
selected sensor.
While changing the sensor type , , ,
parameters of level1 will reset accordingly.
Once set at a particular value, this will not allow the set point
to go below this value.
When changing the setting value and SV < LSV, SV is reset
as LSV.
Sets the minimum limit for set point adjustment. It can be set
from minimum specified range of selected sensor to HSV-1
value.
Function: Sets cycle time for PID action.
10
Parameter
LEVEL2 Parameter
Function: Runs auto tunning.
9
Parameter
This parameter will be prompted only if selected control
action is PID in control parameters.
This parameter used to set YES/NO to start and stop Auto-
tuning.
When Setting as , the unit starts auto-tuning. After
Completing is automatically Set.
During auto-tuning, the AUTO indicator continuously ON.
Function: Sets control action for
relay/SSR.
8
Parameter
This parameter used to set required control action for
relay/SSR.
Min
Max
Fac.
= PID
= No action
= Reverse
= Forward
Min
Max
Fac.
Cycle time also known as duty cycle, the total length of time for
the controller to complete one ON/OFF cycle.
Example :
With a 20 second cycle time, an on time of 10
seconds and an OFF time of 10 seconds represents a 50
percent power output. The controller will cycle ON and OFF
while within the proportional band.
Min
Max
Fac.
1 sec 60 sec 3 sec
Function: Sets differential time.
13
Parameter
Sets the differential time of PID parameter.
Min
Max
Fac.
0
sec
999
sec
30
sec
Setting "0" will turn OFF differential.
Term D is a best estimate of the future trend of the SV-PV error,
based on its current rate of change. It is sometimes called
"anticipatory control", as it is effectively seeking to reduce the
effect of the SV-PV error by exerting a control influence
generated by the rate of error change. The more rapid the
change, the greater the controlling or dampening effect.
Function: Sets proportional band.
11
Parameter
Sets the proportional band of PID parameter.
Min
Max
Fac.
O
0.1 C
O
99.9 C
O
10.0 C
Function: Sets integration time.
12
Parameter
Sets the integration time of PID parameter.
Min
Max
Fac.
0
sec
999
sec
120
sec
Example :
If the (SV-PV) error is large and positive, the
control output will be proportionately large and positive and
vice versa if error is negative.
Term P is proportional to the current value of the SV-PV
error .
Term I accounts for past values of the SV-PV error and
integrates them over time to produce the I term.
Example :
If there is a residual SV-PV error after the
application of proportional control, the integral term seeks to
eliminate the residual error by adding a control effect due to the
historic cumulative value of the error.
Setting "0" will turn OFF integration.
A proportional–integral–derivative controller (PID controller or three
term controller) is a control loop feedback mechanism widely used in
industrial control systems and a variety of other applications requiring
continuously modulated control. A PID controller continuously
calculates an error value as the difference between a desired
setpoint (SV) and a measured process variable (PV) and applies a
correction based on proportional, integral, and derivative terms
(denoted P, I, and D respectively) which give the controller its name.
-1
O
-50 C
Min
Max
Fac.
O
750 C
O
750 C
+1
User can Upload parameters settings from one controller
and download them to multiple controllers.
This will make on site parameter setting easy.
Pro-key (On Request)
The Auto-tuning function automatically computes and sets the
proportional band (P), Integral time (I), Derivative time (D) as
per process characteristics.
After Auto-tuning is complete the
"AUTO"
led will turn OFF.
While Auto-tune is in progress
"AUTO"
led will turn ON.
Carry out the auto-tuning again, if there is a change in setpoint
or process parameters.
If auto -tuning is not complete after 3-4 cycles, it is suspected to
fail. In this case, check the wiring & parameters such as the
control action, input type etc.
PID-time proportional
with auto reset & rate
Working
2. ON/OFF control action (For reverse mode)
The relay is ‘ON’ up to the set temperature and cuts”OFF”
above the set temperature . As the temperature of the system
drops ,the relay is switched ‘ON’ at a temperature slightly
lower than the set point .
The difference between the temperature at which relay
switches ‘OFF’ is the hysteresis or dead band.
HYSTERESIS:
1. Auto tuning
Note : In Auto Tunning running time, user can not change
the parameter value.
48mm
1
2
3
CONTROLLER
GASKET
PANEL
Side Lock
Press & hold key for 4 seconds to enter into Level1
parameter setting( will flash).
Press the key to save the set value and to come out of
parameter setting after changing the set value.
When release the key, will flash.
Press
UP/DOWN
keys to modify the set value and to go to the
next parameter by pressing key.
Press
UP/DOWN
keys to modify the set value and to go to the
next parameter by pressing key.
will flash.
Press & hold key for 8 seconds to enter into Level2
parameter setting( will flash). When release the key,
Press the key to save the set value and to come out of
parameter setting after changing the set value.
TCW-S1-UR2-230AC
TM
48mm
48mm
TCW
User Interface
TCW
2
1
3
5
4
6
7
8
11
9
10
12
L
N
RTD
TC
+
-
NO
C
NC
SSR
+
-
Содержание TCW-S1-UR2-230AC
Страница 2: ......