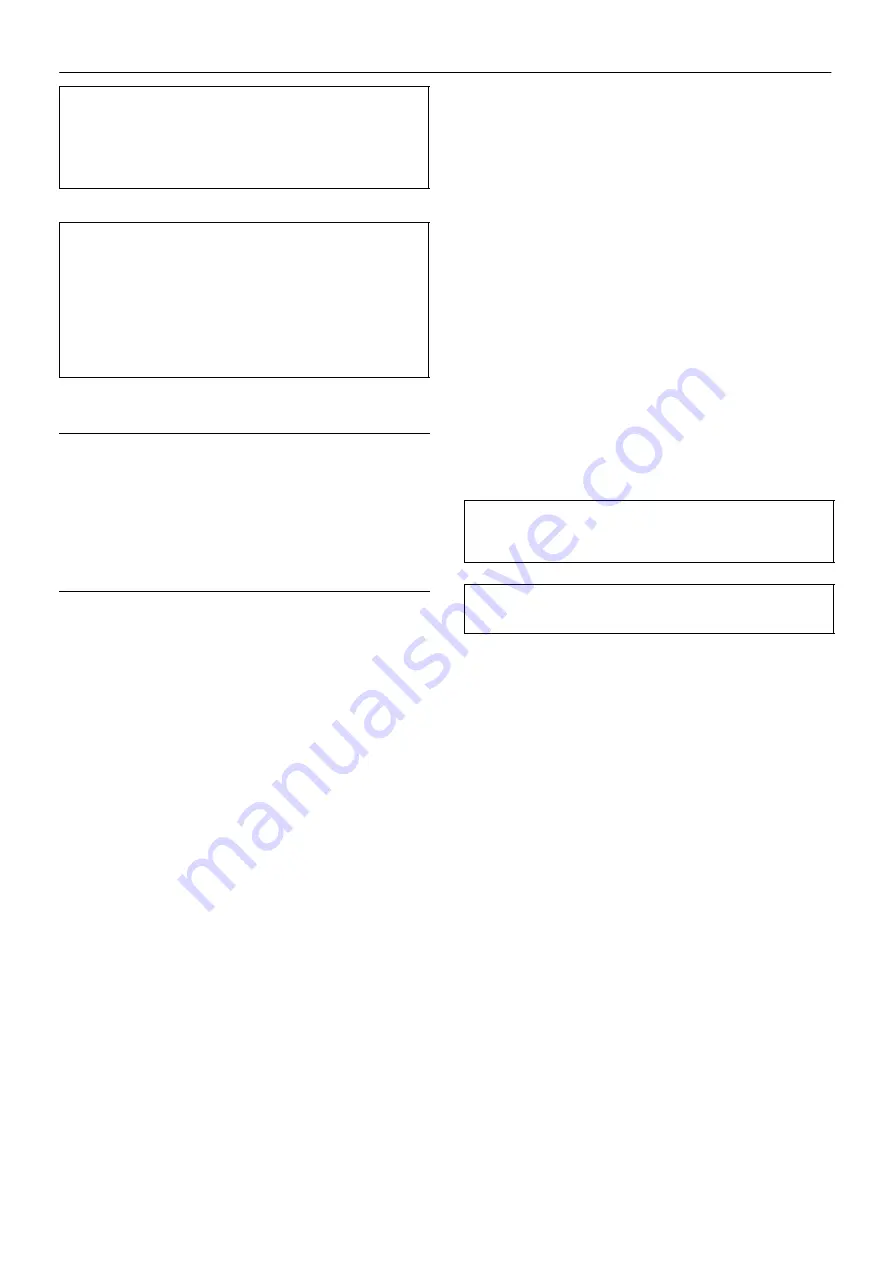
MAINTENANCE
23
M4 M5,5 M7,5 M11
CAUTION
Before working on the belt drive system, ensure that the machine
has been stopped and the electrical power supply isolated, as rotating
equipment can be dangerous. Replace all guards before restarting the
compressor. (Do not allow the belt to become contaminated with
coolant or debris).
CAUTION: Before beginning any work on the compressor, open,
lock and tag the main electrical disconnect and close the isolation
valve on the compressor discharge. Vent pressure from the unit
by slowly unscrewing the coolant fill cap one turn. Unscrewing
the fill cap opens a vent hole, drilled in the cap, allowing pressure
to release to atmosphere. Do not remove the fill cap until all
pressure has vented from the unit. Also vent piping by slightly
opening the drain valve. When opening the drain valve or the
coolant fill cap, stand clear of the valve discharge and wear
appropriate eye protection.
PULLEY ALIGNMENT
Any degree of pulley misalignment will result in a reduction of belt
life. Misalignment of the belt drive should not exceed
1
/
16
”.
Parallel misalignment occurs when the driven shafts are parallel,
but the two pulleys lie in different planes.
Angular misalignment occurs when the two shafts are not parallel.
ALIGNING THE PULLEYS
An easy and effective method of checking alignment in both
directions between the driver and driven pulleys itilises an accurate
straight edge.
Lay the straight edge across the face of the driver (motor) pulley and
check alignment of the driven (airend) pulley. Then lay the straight edge
across the driven pulley and check that the driver pulley is aligned.
Misalignment should not exceed
1
/
16
” when measuring the gap
between the straight edge and the rim of the opposite pulley in each
direction.
This alignment is factory set and should only require resetting if the
drive motor or airend is removed. The following steps should be taken
to ensure proper alignment of all components.
The drive belt must be removed to verify alignment.
Holding the straightedge against the back of the airend pulley,
measure the amount of misalignment seen on the motor pulley. If this
is more than
1
/
16
”, the motor sheave must be removed for repositioning.
To remove the pulley:
1. First, mark the position of the pulley bush on the motor shaft.
2. Remove the two allen headed screws that hold the motor pulley and
pulley bush.
3. Oil the thread and point of the screw.
4. Re–install one of the screws in the hole that has threads on the
bushing side.
5. Slowly tighten the screw until the pulley is pressed from the bush
(Lightly tapping the bush may assist removal).
6. Remove the screw from the hole.
7. Move the bush either in or out on the motor shaft depending upon
the measurement taken earlier.
8. Taking care not to move the bush on the shaft, align the pulley so
that two half holes make complete holes with threads on the pulley side.
9. Oil the threads and points of the screws.
10.Insert the screws into the holes with threads on the pulley side.
11. Slowly and evenly tighten all pulley retaining screws. Torque to 175
lb.in.
12.Hammer against the large end of the bush using a hammer and
block or sleeve to avoid damage. Continue to torque screws until the
specified wrench torque no longer turns the screw after hammering. Fill
the other holes with grease to exclude dirt.
13.Re–check for correct alignment.
14.Re–fit the drive belt as described below.
DRIVE BELT
CAUTION: Ensure that the compressor is isolated from the
compressor air system by closing the isolation valve and
bleeding pressure from the drain valve.
CAUTION: Ensure that the main power disconnect switch is
locked open and tagged.
If installing or removing the belt on a new unit at start–up, the motor
support shipping bolt must first be removed. This bolt is only used to
brace the motor during shipment and will not be reinstalled once the belt
is put into place.
Use only genuine Ingersoll–Rand replacement parts to ensure the
correct belt size and length. Incorrectly sized belts can lead to
overloading of bearings and eventual airend or motor failure.
DISASSEMBLY
Belt tension is maintained due to a cantilevered motor support. The
weight of the motor holds the belt tight.
1. Remove the front of the belt/fan guard on the back of the unit by
removing the six retaining screws.
2. Carefully lift the back of the motor support bracket and place a block
of wood underneath.
3. Remove the belt from the airend pulley and the motor pulley.
INSTALLATION / INSPECTION
Inspect the pulley grooves for foreign material or rubber build–up.
Clean and degrease the pulleys before installing the drive belt to ensure
long belt life.
1. Carefully lift the back of the motor support bracket and place a block
of wood underneath.
2. Install the belt on the airend pulley and the motor pulley. When
installing a new belt, do not force the belt over the pulley grooves.
3. Remove the block of wood from under the bracket.
Содержание SSR M11
Страница 15: ...GENERAL INFORMATION 13 M4 M5 5 M7 5 M11 ...
Страница 34: ......
Страница 35: ......
Страница 36: ...Printed in the United Kingdom ...