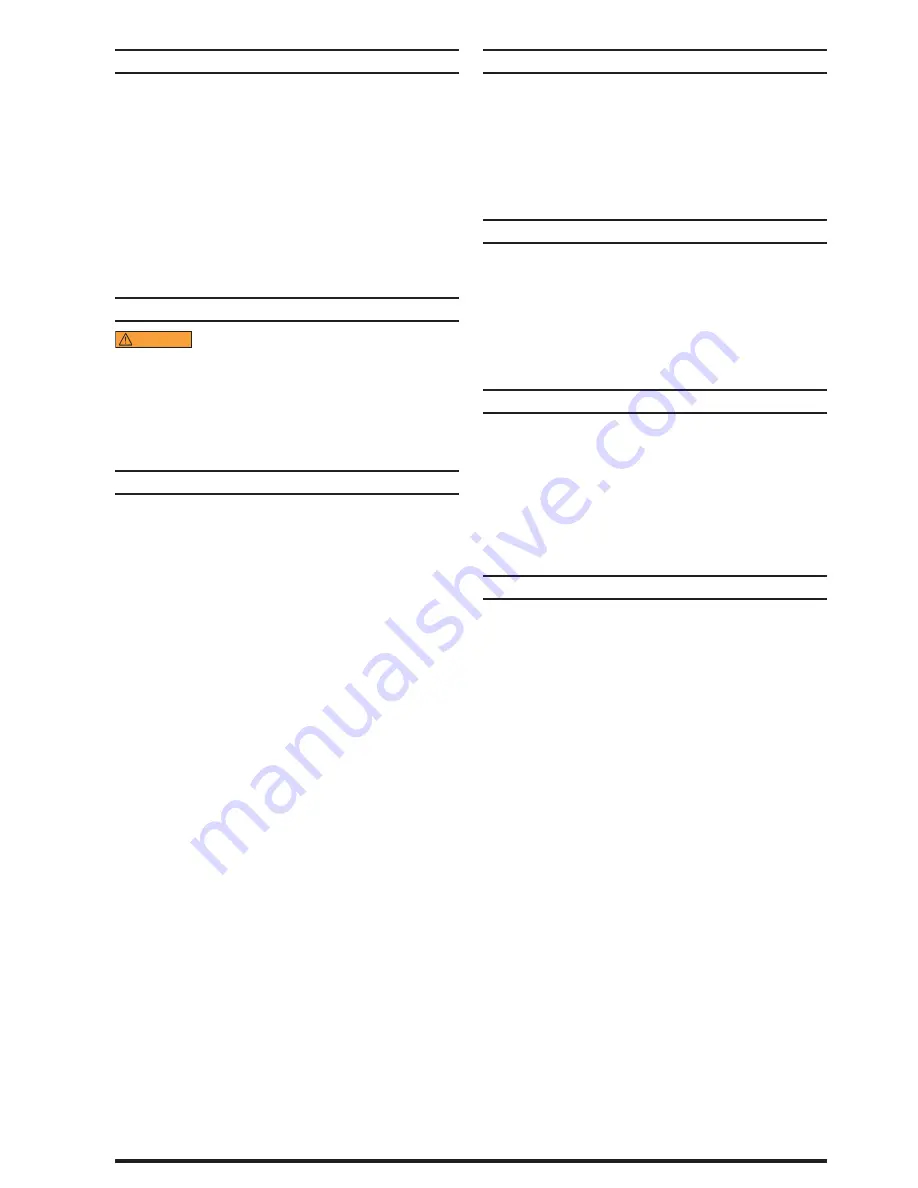
PD20X-XXX-XXX-B (en)
Page 3 of 8
y
Hytrel® and Viton® are registered trademarks of the DuPont Company
y
Loctite® is a registered trademark of Henkel Loctite Corporation
y
Kynar® is a registered trademark of Arkema Inc.
y
y
Santoprene® is a registered trademark of Monsanto Company, licensed to Advanced Elastomer Systems, L.P.
y
ARO® is a registered trademark of Ingersoll-Rand Company
y
y
Lubriplate® is a registered trademark of Lubriplate Division (Fiske Brothers Refi ning Company)
y
262™, 271™ and 572™ are trademarks of Henkel Loctite Corporation
y
PARTS AND SERVICE KITS
Refer to the part views and descriptions as provided on pages 4
through 7 for parts identifi cation and service kit information.
Certain ARO “Smart Parts” are indicated which should be avail-
able for fast repair and reduction of down time.
Service kits are divided to service two separate diaphragm
pump functions: 1. AIR SECTION, 2. FLUID SECTION. The Fluid
Section is divided further to match typical part Material Op-
tions.
MAINTENANCE
Provide a clean work surface to protect sensitive internal mov-
ing parts from contamination from dirt and foreign matter dur-
ing service disassembly and reassembly.
Keep good records of service activity and include the pump in
preventive maintenance program.
Before disassembling, empty captured material in the outlet
manifold by turning the pump upside down to drain material
from the pump.
FLUID SECTION DISASSEMBLY
Remove (61) outlet manifold and (60) inlet manifold.
Remove (22) balls, (19) “O” rings (if applicable) and (21) seats.
Remove (15) fl uid caps.
NOTE: Only PTFE diaphragm models use a primary diaphragm (7)
and a backup diaphragm (8). Refer to the auxiliary view in the Fluid
Section illustration.
4. Remove the (6) diaphragm washer, (7) or 7 / 8) diaphragms and
(5) backup washer.
NOTE: Do not scratch or mar the surface of (1) diaphragm rod.
FLUID SECTION REASSEMBLY
SERVICE NOTE: ARO pn 204214-T diaphragm assembly tool is rec-
ommended for use when reassembling the pump.
Reassemble in reverse order. Refer to the torque requirements
on page 5.
Clean and inspect all parts. Replace worn or damaged parts
with new parts as required.
Lubricate (1) diaphragm rod and (144) “U” cups with Lubriplate®
FML-2 grease (94276 grease packet is included in service kit).
For models with PTFE diaphragms: Item (8) Santoprene dia-
phragm is installed with the side marked “AIR SIDE” towards the
pump center body. Install the (7) PTFE diaphragm with the side
marked “FLUID SIDE” towards the (15) fl uid cap.
Re-check torque settings after the pump has been re-started
and run a while.
y
y
y
y
y
1.
2.
3.
y
y
y
y
y
GENERAL DESCRIPTION
The ARO diaphragm pump off ers high volume delivery even at low
air pressure and a broad range of material compatibility options are
available. Refer to the model and option chart. ARO pumps feature
stall resistant design, modular air motor / fl uid sections.
Air operated double diaphragm pumps utilize a pressure diff eren-
tial in the air chambers to alternately create suction and a positive
fl uid pressure in the fl uid chambers, valve checks insure a positive
fl ow of fl uid.
Pump cycling will begin as air pressure is applied and will continue
to pump and keep up with the demand. It will build and maintain
line pressure and will stop cycling once maximum line pressure is
reached (dispensing device closed) and will resume pumping as
needed.
AIR AND LUBE REQUIREMENTS
WARNING
EXCESSIVE AIR PRESSURE. Can cause pump dam-
age, personal injury or property damage.
A fi lter capable of fi ltering out particles larger than 50 microns
should be used on the air supply. There is no lubrication re-
quired other than the “O” ring lubricant which is applied during
assembly or repair.
If lubricated air is present, make sure that it is compatible with
the “O” rings and seals in the air motor section of the pump.
OPERATING INSTRUCTIONS
Always fl ush the pump with a solvent compatible with the ma-
terial being pumped if the material being pumped is subject to
“setting up” when not in use for a period of time.
Disconnect the air supply from the pump if it is to be inactive
for a few hours.
The outlet material volume is governed not only by the air sup-
ply, but also by the material supply available at the inlet. The
material supply tubing should not be too small or restrictive.
Be sure not to use hose which might collapse.
When the diaphragm pump is used in a forced-feed (fl ooded
inlet) situation, it is recommended that a “check valve” be in-
stalled at the air inlet.
Secure the diaphragm pump legs to a suitable surface to insure
against damage by vibration.
y
y
y
y
y
y
y