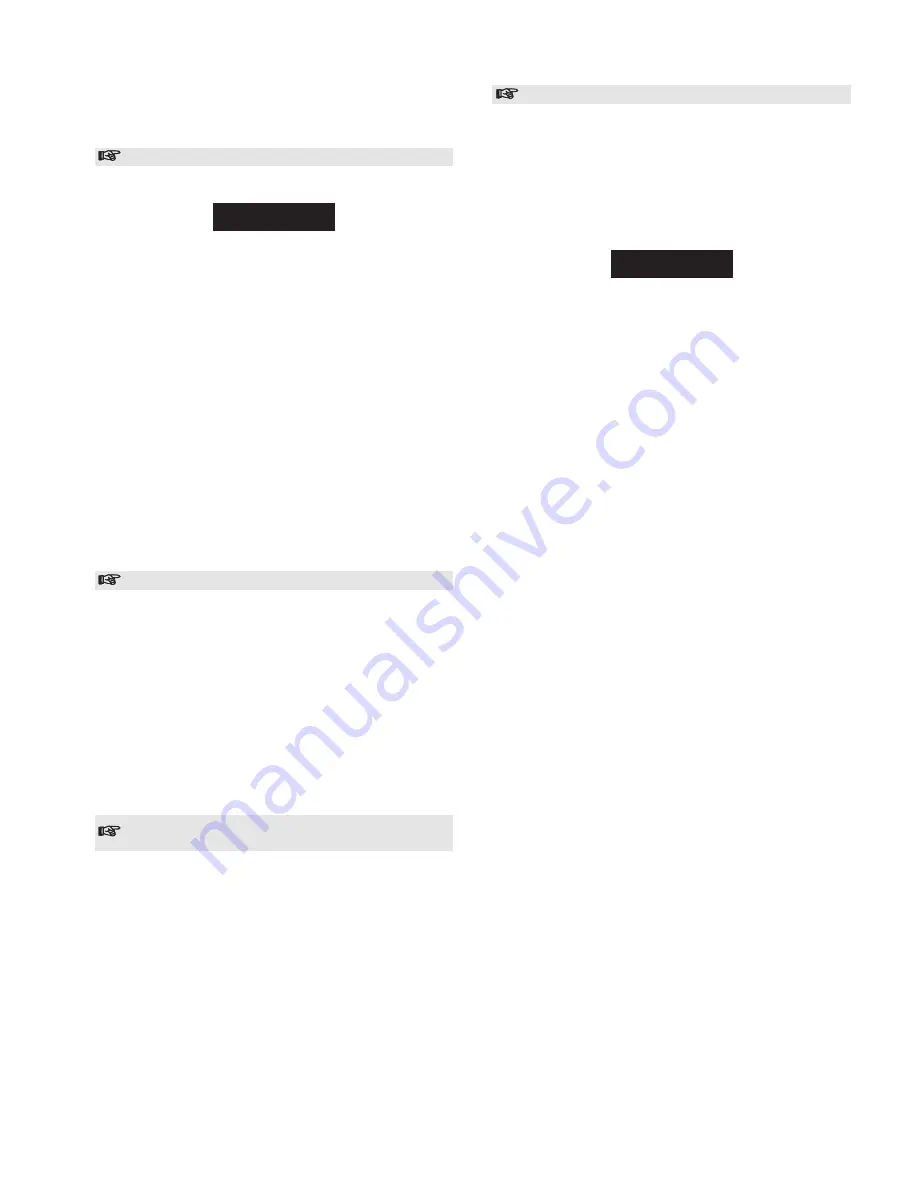
29
3.
Align bolt holes, with air inlet on motor housing facing up.
Apply Loctite
®
242 to capscrews (221) and insert through
motor flange into adapter (71) and tighten to 33-36 ft lb.
(45-49 Nm).
4.
Attach muffler assembly (234) to exhaust manifold (233).
Control Valve Assembly
Refer to Dwg. MHP1314.
NOTICE
• During assembly align parts using match marks made
during disassembly.
1.
Install seal rings (315) on each end of valve body (316).
2.
Insert valve bushing (314) into valve housing (311). Ensure
ports in bushing and flat cutout in valve body are properly
aligned with housing ports.
3.
Install valve body (316) into valve bushing (314).
4.
Install valve body retainer (305) with two capscrews (302)
and lockwashers (304). Torque capscrews to 25 ft lbs (34
Nm).
5.
If removed, reinstall spring retaining stud (306) and torque
to 25 ft lbs (34 Nm).
6.
Install spring (303) and handle (300) on square shaft of
valve body (316). The spring (303) ends must straddle the
spring retaining stud (306) on throttle handle (300). Install
roll pin (301).
7.
Check throttle handle moves fully left and right without
sticking or binding. Throttle handle should center, by
spring force, automatically when released.
Installation of Control Valve and Inlet Manifold
Refer to Dwg. MHP1314.
1.
Verify spool locating pin (613) is straight and installed in
manifold (606). Position gasket (611) and manifold/cover
assembly on motor housing. Manifold and cover are
bonded together and thermoplastic coated. Install four
capscrews (614) to clamp parts to motor housing (220).
Torque capscrews to 108-112 in lb. (12-13 Nm).
2.
Mount control valve assembly (260) and gasket (248) to
cover such that handle is toward winch drum. Install four
capscrews (331) and torque to 33-36 ft lb. (45-49 Nm).
3.
Connect brake line to swivel elbow fitting (319) on control
valve housing.
4.
Connect air supply line to control valve.
Installation of Remote Control Valve and Inlet
Manifold
Optional feature. Refer to Dwg. MHP1304.
1.
Verify spool locating pin (613) is straight and installed in
manifold (606). Position gasket (611) and manifold on
motor housing. Apply Loctite
®
242 to capscrew (614)
threads and install four capscrews to clamp manifold to
motor housing (220). Torque capscrews to 108-112 in lb.
(12-13 Nm).
2.
Apply Loctite
®
515 to valve assembly mounting surface
and install on cover (607). Apply Loctite
®
242 to capscrew
(615) threads and install four capscrews to clamp cover to
valve assembly. Torque capscrews to 55 ft lb (74 Nm).
3.
Apply Loctite
®
515 to manifold surface and install cover
and valve assembly. Position assembly such that valve
exhaust port is away from the winch drum. Install four
capscrews (608) and torque to 21 ft lb. (28 Nm).
4.
Connect brake line to connector fitting (621).
5.
Connect pendant hoses to valve fittings.
6.
Connect air supply line to control valve.
Reduction Gear Assembly
Refer to Dwg. MHP1313.
1.
Press caged needle bearings (57) into reducer housing (59).
With oil seal (58) lip facing towards reducer housing,
install oil seal in reducer housing.
2.
Install thrust washer (44) in groove in output planet carrier
(35).
3.
Determine planet gear (43) to carrier (35) end clearance for
each gear:
NOTICE
• Shim output carrier (35) planet gears for 0.005 to 0.032
inch (0.1 to 0.8 mm) end clearance between gear (43) and
carrier.
a.
If not noted during disassembly, determine planet gear
(43) end clearance. Place planet gear in carrier (35)
and insert pin (36) to hold in place. Slide gear against
one side of carrier wall. Measure the gap between
opposite side of carrier interior face and gear. Repeat
for each gear.
b.
Measure the width of two washers (38), (39) and (40).
Combine the amounts of the washers and subtract from
the amount of the gap determined in step a. Add or
remove washers as necessary to establish a 0.005 to
0.032 inch (0.1 to 0.8 mm) end clearance. Repeat for
each gear.
4.
Assemble and install planet gear assembly in the output
carrier (35):
a.
Cut two pieces of cardboard into 3 inch (76 mm)
squares. Place planet gear (43) on one of these pieces
and place pin (36) into hole in center of gear. Insert
eighteen roller bearings (41) between pin and gear.
Take care to ensure initial pins inserted do not tip
over.
b.
Insert spacer (42) followed by the second set of 18
roller bearings.
c.
Place half of the washers required to establish end
clearance (refer to Step 3b.) over pin and against gear
face. Grasp assembly, including cardboard, and flip
over onto second piece of cardboard. As gear slides
down pin onto bottom cardboard, allow pin to push
top piece of cardboard off.
d.
Place other half of the washers required to establish
end clearance (refer to Step 3b.) over pin and against
gear face. Grasp assembly carefully and move to
carrier.
e.
Slide assembled gear partially into position in carrier,
up to pin. Slowly remove pin taking care not to let
bearings tip over or fall. Carefully slide gear assembly
into carrier, aligning hole in gear with hole in carrier.
e.
Place output planet pin (36) into one end of output
carrier (35). Ensure end of pin, with hole, is inserted
such that it will line up with hole in carrier for roll pin
(37) installation.
f.
Slide pin (36) until hole in pin and hole in carrier are
aligned. Verify end clearance tolerance is 0.005 to
0.032 inch (0.1 to 0.8 mm). If required, add or remove
washers to adjust clearance. Secure pin to carrier using
roll pin (37). Carefully tap roll pin into place taking
care not to ‘mushroom’ the head. Tap until level with
top of carrier.
g.
Repeat procedure for remaining gears.
Содержание force5 GULF MAN-RIDER FA2A-GMR
Страница 8: ...8 ...
Страница 34: ...34 WINCH ASSEMBLY PARTS DRAWING ...
Страница 36: ...36 MOTOR ASSEMBLY PARTS DRAWING ...
Страница 40: ...40 CONTROL VALVE ASSEMBLY PARTS DRAWING ...
Страница 42: ...42 REMOTE PENDANT AND CONTROL VALVE ASSEMBLY PARTS DRAWING ...