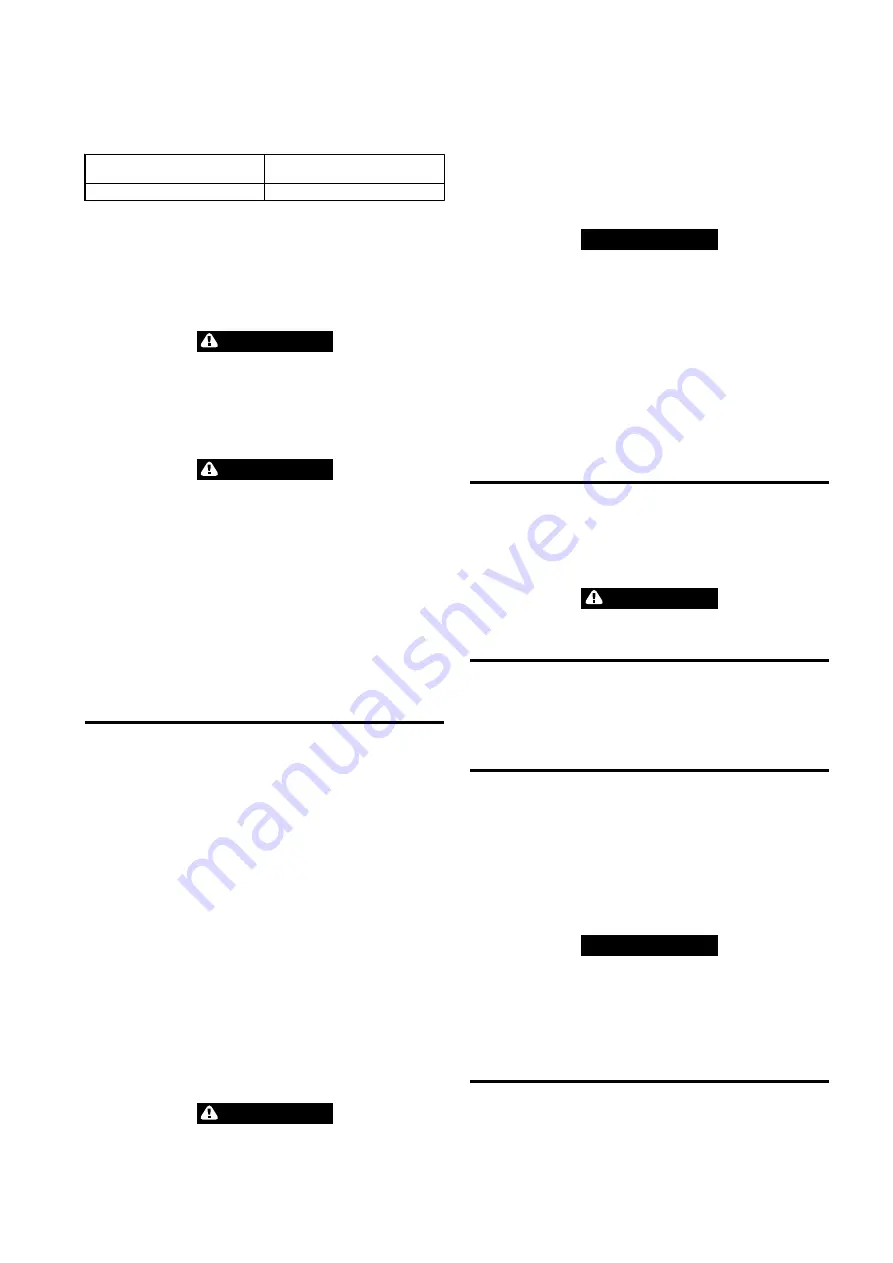
When considering wire rope requirements the actual working load must include not
only the static or dead load but also loads resulting from acceleration, retardation
and shock load. Consideration must also be given to the size of the winch wire rope
drum, sheaves and method of reeving. Wire rope construction must be 10 mm EIPS 6
X 19 IWRC with a minimum breaking strength of 15,690 lbs (69.8 kN) right lay to
assist spooling. Refer to Table 4 ‘Wire Rope Size’ on page 5.
Table 4: Wire Rope Size
Wire Rope Anchor
Part No.
Size
382–30543
3/8 inch (10 mm)
Note:
Wire rope diameter is fixed if grooved drum option is used.
n
Installing Wire Rope
Refer to Dwg. MHP2753 on page 11.
A.
Dead End of Wire Rope;
B.
Wire Rope Anchor.
1. Cut wire rope to length in accordance with wire rope manufacturer’s instructions.
2. Feed end of wire rope through drum anchor pocket hole.
3. Forming a loop, wrap loop around anchor, approximately 22 inches (559 mm) of
wire rope. Ensure dead end of wire rope is facing away from the drum flange.
4. Pull wire rope anchor into position in drum anchor pocket.
WARNING
• Install wire rope to come off drum in an underwound position. Improper
installation of wire rope can result in failure of disc brake to hold load and
prevent overload device operation.
• Do not allow wire rope to come in contact with drum guard panels during
winch operation. Wire rope could become worn and damaged. Adjust drum
guard panels to clear wire rope travel angle. Refer to ‘Drum Guard’ section
on page 5 and warning label 71459937.
CAUTION
• Make sure first wrap of wire rope is tight and lays flush against drum flange.
• Ensure correct wire rope anchor is used.
n
Safe Wire Rope Handling Procedure
-
Always use gloves when handling wire rope.
-
Never use wire rope that is frayed or kinked.
-
Never use wire rope as a sling.
-
Always ensure wire rope is correctly spooled and the first layer is tight against
drum.
-
Always follow wire rope manufacturer’s recommendation on use and
maintenance of wire rope.
n
Wire Rope Spooling
To compensate for uneven spooling and the decrease in line pull capacity as the drum
fills up, use as short a wire rope as practical. When rewinding apply tension to the
end of the wire rope to eliminate line slack. This helps achieve level winding and
tight spooling.
n
Air Supply
Air supply must be clean, free from moisture and lubricated to ensure optimum motor
performance. Foreign particles, moisture and lack of lubrication are primary causes
of premature motor wear and breakdown. Using an air filter, lubricator and moisture
separator will improve overall winch performance and reduce unscheduled downtime.
Air consumption is 62 scfm (1.75 cu.m/min) at rated operating pressure of 90 psig
(6.3 bar/630 kPa) at Emergency Stop Valve 1/2 inch NPT inlet. Exceeding 90 psi (6.3
bar/630 kPa) may cause inadvertent activation of the overload device. If air supply
varies from what is recommended, winch performance will change.
Install air line lubricator, filter and regulator as close as possible to air inlet on motor.
Lubricator must be located no more than 10 ft (3 m) from motor. Air line accessories
package comes standard, mounted to drum guard panel on opposite side of operator.
Refer to Dwg. MHP0191 on page 11,
A.
Air Out;
B.
Lubricator;
C.
Regulator;
D.
Air
In;
E.
Filter.
n
Air Lines
The inside diameter of the winch air supply lines must not be less than the size shown
in Table 2 ‘General Specifications’ on page 3. Prior to making final connections, all
air supply lines should be purged with clean, moisture free air or nitrogen before
connecting to winch inlet. Supply lines should be as short and straight as installation
conditions will permit. Long transmission lines and excessive use of fittings, elbows,
tees, globe valves, etc. cause a reduction in pressure due to restrictions and surface
friction in the lines.
n
Air Line Lubricator
Always use an air line lubricator with these motors. Lubricator must have an inlet and
outlet at least as large as the inlet on motor.
CAUTION
• Lubricator must be located no more than 10 ft (3 m) from the motor.
• Shut off air supply before filling air line lubricator.
Air line lubricator should be replenished daily and set to provide 6 to 9 drops per
minute of ISO VG 32 (SAE 10W) oil. A fine mist will be exhausted from the throttle
control valve when the air line lubricator is functioning properly.
n
Air Line Filter
It is recommended that an air line strainer/filter be installed before the lubricator,
to prevent dirt from entering motor. Strainer/filter should provide 20 micron filtration
and include a moisture trap. Clean strainer/filter periodically to maintain its operating
efficiency.
n
Air Pressure Regulator
An air pressure regulator is install between lubricator and filter as shown.
NOTICE
• Do not adjust regulator for a CE marked product, these are preset at factory.
Adjustment of regulator will effect overload settings and product may no
longer conform to CE regulations.
• Not all products are CE approved, refer to products data (name) plate to see
if this applies.
n
Moisture in Air Lines
Moisture that reaches the air motor through air supply lines is a primary factor in
determining the length of time between service overhauls. Moisture traps can help
to eliminate moisture. Other methods, such as an air receiver which collects moisture
before it reaches the motor, an aftercooler at the compressor that cools the air to
condense and collect moisture prior to distribution through the supply lines are also
helpful.
n
Mufflers
Ensure mufflers are installed in exhaust ports of control valve and motor. Check
mufflers periodically to ensure they are functioning correctly.
n
Drum Guard
A drum guard is standard on all
MR
and
MR-CE
winches.
Refer to the Product Parts Information Manual.
Drum guard panels must be adjusted to suit wire rope departure angle. To reposition
drum guard panels remove nuts and slide out crossbar. Position panels to avoid wire
rope contact and install crossbar and nuts.
WARNING
• Do not allow wire rope to come in contact with drum guard panels during
winch operation. Wire rope could become worn and damaged. Adjust drum
guard panels to clear wire rope travel angle.
n
Slack Line Detector
Adjustments
Refer to Dwg. MHP3149 on page 11 and MHP3147.
Prior to initial use adjust slack line as follows:
1. Payout wire rope to the desired position with no slack in wire rope.
2. Loosen capscrew located in center of cam actuator (208).
3. Tighten capscrew once adjustment to slack arm has been made.
n
Limit Switch
Operate winch in both directions to activate limit switches. Limit switches should
engage at established s/- 2 ft (0.7 m), and prevent winch operation until
reset by shifting winch operating direction.
n
Adjustments
Refer to Dwg. MHP2688 on page 11,
A.
Center Nut;
B.
Payout;
C.
Haul-In.
To adjust set points:
Follow instructions in the order they appear for limit switch adjustment
(use two
people to make adjustments):
NOTICE
• These adjustments are for underwound wire rope applications only.
1. Remove cap from limit switch cover.
2. Unscrew center nut slightly.
3.
PAYOUT:
Rotate (1) screw clockwise while slowly paying out until winch shuts
off.
4.
HAUL-IN:
Rotate (2) screw counterclockwise while slowly hauling in until winch
shuts off.
5. Tighten center nut.
6. Reinstall cap on limit switch cover and tighten.
n
Motor
For optimum performance and maximum durability of parts, provide recommended air
supply as measured at motor inlet. Refer to Table 2 ‘General Specifications’
on page 3. The air motor should be installed as near as possible to compressor or air
receiver.
Form MHD56470 Edition 4
5
Содержание FA150KGi Series
Страница 14: ...SERVICE NOTES 14 Form MHD56470 Edition 4...
Страница 16: ...www ingersollrandproducts com...