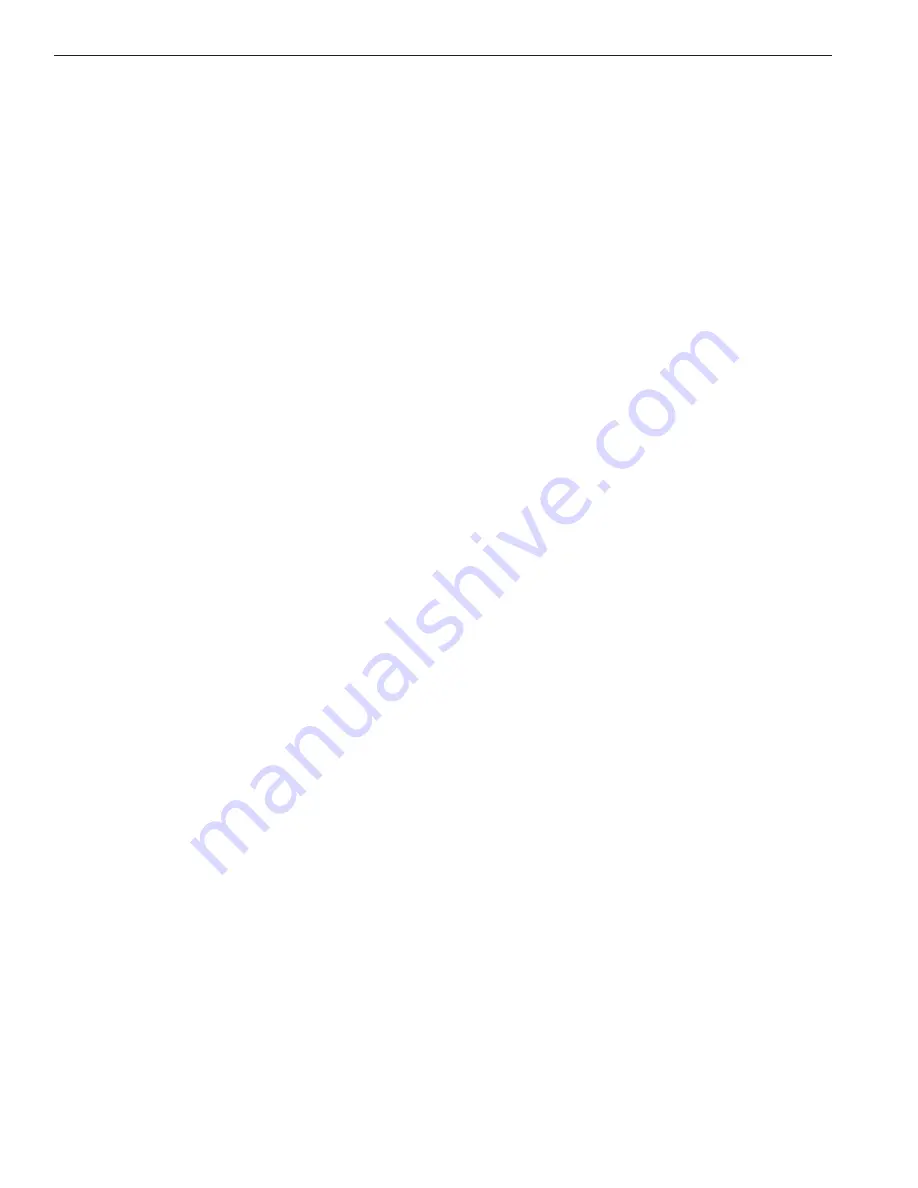
6
Non-cycling Refrigerated Dryer
MODELS D340IN, D40IN, D510IN, D680IN, D850IN, D100IN, D1190IN, D1360IN
http://air.ingersollrand.com
7.0 PRINCIPLES OF OPERATION
7.1 INTRODUCTION
Ingersoll Rand non-cycling dryers remove moisture, oil vapor
and other contaminants from compressed air by cooling the
air temperature to 36 deg.F (. deg.C). This cooling process
condenses the contaminants into liquid droplets which can
then be easily removed from the air. The major systems of
the dryers that contribute to its operation are the following:
Air System, Moisture Removal System, Refrigeration System
and the Controls System. The following paragraphs describe
each of the systems in greater detail.
7.2 AIR SYSTEM
This system consists of the dryer components which are
in contact with the compressed air. Referring to Figure
1 and following the bold “AIR FLOW” path indication, hot
saturated air from the air compressor enters the precooler/
reheater where the air temperature is reduced prior to
entering the chiller by the cool air exiting the air/moisture
separator. This precooling allows for the use of a smaller
refrigeration system. The air then goes into the chiller
section where it is further cooled to the desired dew point
through direct heat transfer with evaporating refrigerant.
The air continues to the separator where the moisture is
removed, thereby allowing the cool, dry air to return to the
precooler/reheater. As the air passes through the precooler/
reheater the air temperature is elevated by the warm, wet
inlet air. The air exiting the reheater portion of the dryer
should be approximately 15-0 deg.F lower than the inlet air
temperature based on standard conditions at full rated flow.
7.3 MOISTURE REMOVAL SYSTEM
Liquid droplets are removed from the air stream in the
separator. As the air and liquid mixture passes through the
separator it spins, slows down and then changes direction.
This causes condensate to fall out of the air stream and
collect in the bottom of the separator. The collected liquid is
removed from the separator by a timed electric drain which
is controlled by the Controller.
The Drain Open time and Drain Closed time are accessed
by depressing the appropriate button and using the up and
down arrows to change the value. The Drain Open value is
seconds; the Drain Closed value is minutes.
To obtain the optimum time values for operation of
the electric drain valve, set the drain closed time to
five minutes and the open time to ten seconds.
After running the unit under full rated flow for
•
•
approximately 30 minutes, verify that when the
electric drain opens, all of the accumulated liquid is
discharged and then followed by a small burst of air.
If a small amount of liquid and a large amount of air is
discharged, decrease the on-time setting or increase
the off-time setting. If there is all liquid and no air
has been discharged, increase the on-time setting or
decrease the off-time setting.
The on/off-time settings will vary accordingly to
seasonal conditions. During the summer when more
moisture is present in the air system, a shorter on-
time that increases the valve opening frequency is
required. A longer off-time may be used during the
winter months when moisture levels are lower.
7.4 REFRIGERATION SYSTEM
The Refrigeration System consists of all the components
which handle refrigerant R-404A. This is a hermetically
sealed closed-loop system. Referring to Figure 1 and
following the dot-dash “REFRIGERANT FLOW” path
indication, refrigerant is shown leaving the chiller evaporator
section, which in the process of removing heat is changed
from a low pressure liquid to a low pressure gas. This
gas enters the suction side of the compressor where it is
compressed into a high pressure gas. The high pressure gas
is cooled in the condenser section becoming a high pressure
liquid. It then goes through a permanent filter-dryer that
ensures the refrigerant system is free of contaminants. A
small diameter capillary tube or expansion valve meters
the refrigerant into the chiller’s evaporator. The pressure
is reduced upon entering the chiller evaporator where it
removes heat from the air system. When there are low loads
(low air flow rate or low inlet temperature), a hot gas valve
by-passes the condenser and throttling device. This valve
maintains a minimum evaporator pressure of 76 psig, which
corresponds to a chiller temperature of 34 deg.F, to prevent
freeze-up.
•
•